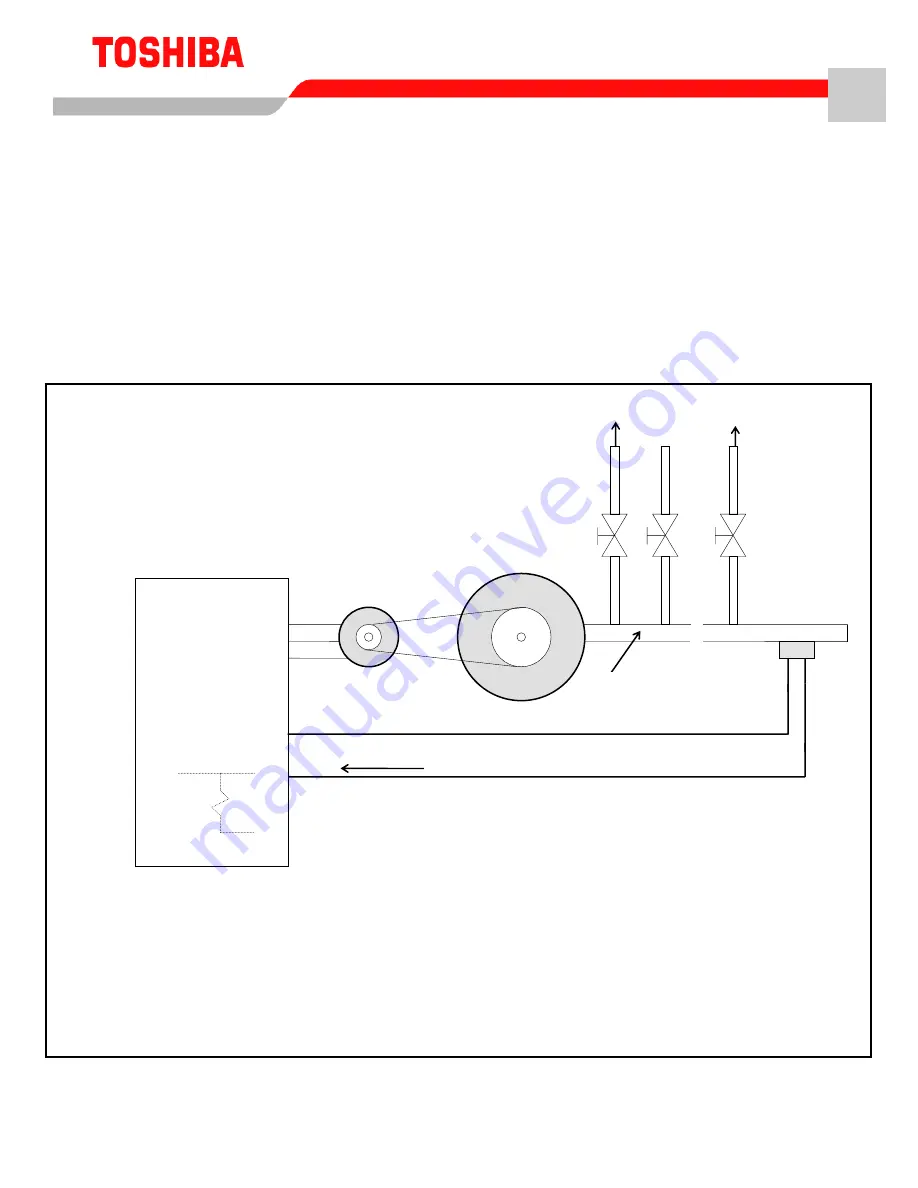
*
For additional assistance, please contact Toshiba Adjustable Speed Drive Marketing Dept. at (800) 872-
2192
48
PID
Introduction
The built-in PID of the G3 can be used to maintain a constant process variable such as flow, pressure,
temperature, and level. In the example below, the drive is used to vary the speed of the motor/pump to
maintain a constant pressure at the output of the pump. As the valves on the output of the pump are
opened, the pressure goes low. The drive senses this via a 4-20 mA feedback signal and speeds up to
increase pressure up to the desired level. The drive will slow the motor/pump down as the valves close.
The rate at which the drive responds to changes is adjustable via three parameters (Proportional Gain,
Integral Time, and Differential Time) and will have to be field-tuned. Later in this guideline, PID
applications will be discussed in general.
Connections
Check your transducer’s schematic for connection information.
The above diagram is typical for a loop-
powered transducer.
Separately powered
isolated
transducers feed into the ‘IV’ and “CC” terminals. If your transducer is not
isolated, order an isolated input board. The inputs to the standard G3 are not isolated;
do not
connect the ‘CC’
terminal to ground.
Set SW1 (to the right of the phone jack on the control board) in the ‘I’ position.
22
Output Flow
//
//
D/A
G3
4-20 mA feedback
Transduce
Area in which constant
pressure is desired
IV
500
6
CC
MOTOR
PUMP
P24
VALVES