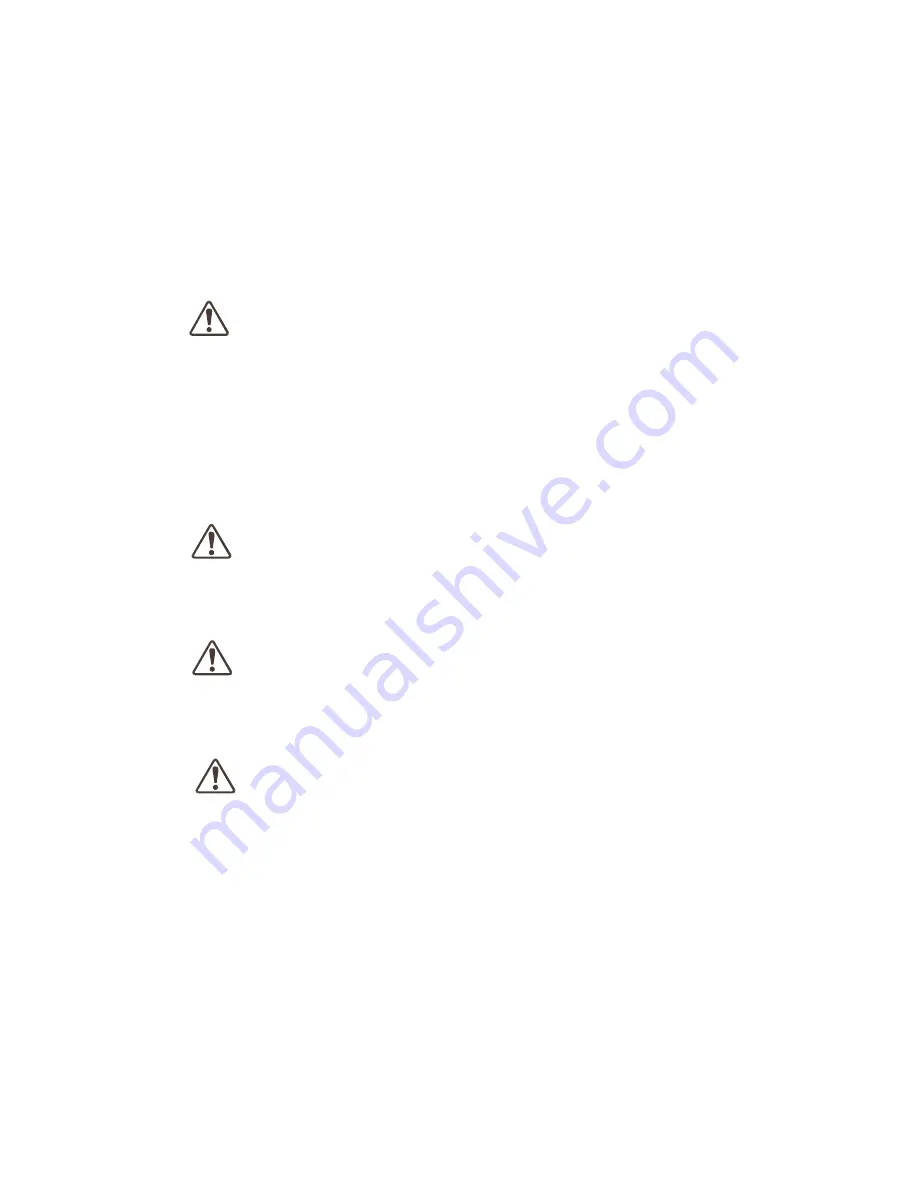
ACE-tronics G9 ASD Installation and Operation Manual
1
General Safety Information
DO NOT attempt to install, operate, maintain, or dispose of this equipment until you have read and
understood all of the product safety information and directions that are contained in this manual.
Safety Alert Symbol
The Safety Alert Symbol is comprised of an equilateral triangle enclosing an exclamation mark. This
indicates that a potential personal injury hazard exists.
Signal Words
Listed below are the signal words that are used throughout this manual followed by their descriptions and
associated symbols. When the words
DANGER
,
WARNING,
or
CAUTION
are used in this manual they
will be followed by important safety information that must be carefully adhered to.
The word
DANGER
preceded by the safety alert symbol indicates that an imminently hazardous situation
exists that, if not avoided, will result in serious injury to personnel or loss of life.
The word
WARNING
preceded by the safety alert symbol indicates that a potentially hazardous situation
exists that, if not avoided, could result in serious injury to personnel or loss of life.
The word
CAUTION
preceded by the safety alert symbol indicates that a potentially hazardous situation
exists that, if not avoided, may result in minor or moderate injury.
The word
CAUTION
without the safety alert symbol indicates a potentially hazardous situation exists
that, if not avoided, may result in equipment and property damage.
DANGER
WARNING
CAUTION
CAUTION
Buy: www.ValinOnline.com | Phone 844-385-3099 | Email: [email protected]