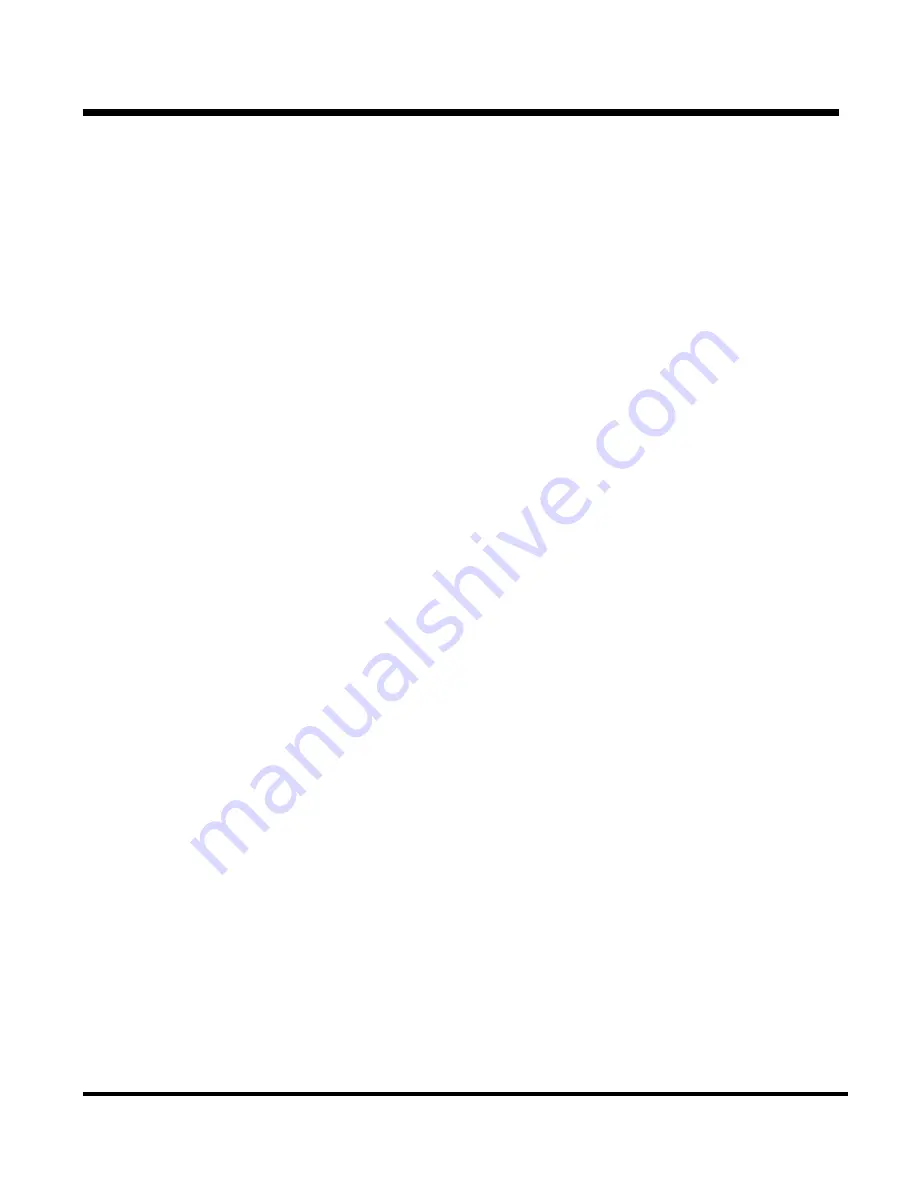
Section 2 – SR-2 Hardware Description
REFRIGERATION CONTROL
COMPONENTS
These components are used by the microprocessor
to sense conditions or control operation of the
refrigeration system. The microprocessor
determines the necessary requirements by
considering the setpoint, the software, the
programmable feature and OptiSet
®
settings, and
the information supplied by the sensors.
Discharge Pressure Transducer (DPT)
This transducer supplies the compressor discharge
pressure to the microprocessor. The sense wire is
connected to the microprocessor at J3 via the DPI
wire. The DPP and DPN wires supply power to the
sensor. This sensor is installed on ETV-equipped
units only.
Suction Pressure Transducer (SPT)
This transducer supplies the compressor suction
pressure to the microprocessor. The sense wire is
connected to the microprocessor at J3 via the SPI
wire. The SPP and SPN wires supply power to the
sensor. This sensor is installed on ETV equipped
units only.
High Pressure Cutout Switch (HPCO)
The high pressure cutout switch is located on the
discharge manifold of four cylinder compressors.
The switch is closed with normal pressures and
opens with excessive pressures to shut the unit
down and prevent damage.
Pilot Solenoid (PS)
The microprocessor energizes (opens) the Pilot
Solenoid to shift the 3 way valve to the heat position
during heat or defrost mode operation. The normally
closed Pilot Solenoid is located near the 3 way
valve. The pilot solenoid is energized and LED 8 is
lit when the microprocessor energizes the Pilot
Solenoid Smart FET. This supplies power via the 26
wire to the pilot solenoid. The circuit is protected by
the Smart FET.
Electronic Throttling Valve (ETV)
The Electronic Throttling Valve is capable of opening
and closing incrementally and is installed between
the evaporator
and the compressor.
The ETV is controlled directly by the microprocessor
Smart FET outputs. As the temperature approaches
setpoint, the ETV begins to close, throttling the
suction gas returning to the compressor and thus
reducing cooling capacity. As the box temperature
approaches setpoint, the ETV becomes more nearly
closed. This feature provides very smooth and
steady temperature control. Modulation is only
operational in Continuous mode. The circuit is
protected by the ETV Smart FETs.
2-24
31 January 2005
Summary of Contents for SR-2 SmartReefer2
Page 4: ......
Page 7: ...Tab goes here and the next page should be GREEN Section 1 Safety...
Page 8: ......
Page 10: ...Section 1 SR 2 Safety Information 1 2 18 January 2005...
Page 14: ...Section 1 SR 2 Safety Information 1 6 18 January 2005...
Page 15: ...Tab goes here and the next page should be GREEN Section 2 Hardware Description...
Page 16: ......
Page 48: ...Section 2 SR 2 Hardware Description 2 32 31 January 2005...
Page 49: ...Tab goes here and the next 2 pages should be GREEN Section 3 Software Description...
Page 50: ......
Page 96: ...Section 3 SR 2 Software Description 3 46 31 January 2005...
Page 97: ...Tab goes here and the next page should be GREEN Section 4 Operation...
Page 98: ......
Page 181: ...Tab goes here and the next 2 pages should be GREEN Section 5 Diagnostics...
Page 182: ......
Page 266: ...Section 5 SR 2 Diagnostics 5 84 02 February 2005...
Page 267: ...Tab goes here and the next page should be GREEN Section 6 Service Procedures...
Page 268: ......
Page 270: ...Section 6 SR 2 Service Procedure Index Page 2 01 February 2005...
Page 282: ...Section 6 SR 2 Service Procedure A01B Page 6 P41RA01B 31 January 2005...
Page 298: ...Section 6 SR 2 Service Procedure A02A Page 12 P41RA02A 02 February 2005...
Page 318: ...Section 6 SR 2 Service Procedure A03B Page 4 P41RA03B 30 January 2005...
Page 338: ...Section 6 SR 2 Service Procedure A15A Page 4 P41RA15A 30 January 2005...
Page 360: ...Section 6 SR 2 Service Procedure A46B Page 8 P41RA46B 30 January 2005...
Page 366: ...Section 6 SR 2 Service Procedure A48A Page 6 P41RA48A 30 January 2005...
Page 376: ...Section 6 SR 2 Service Procedure A50A Page 6 P41RA50A 31 January 2005...
Page 394: ...Section 6 SR 2 Service Procedure F08A Page 4 P41RF08A 30 January 2005...
Page 398: ...Section 6 SR 2 Service Procedure F09A Page 4 P41RF09A 30 January 2005...
Page 402: ...Section 6 SR 2 Service Procedure G03A Page 4 P41RG03A 31 January 2005...
Page 406: ...Section 6 SR 2 Service Procedure H04A Page 4 P41RH04A 30 January 2005...
Page 407: ...Tab goes here and the next page should be GREEN Section 7 Service Information...
Page 408: ......
Page 410: ...Section 7 SR 2 Information 7 2 02 February 2005...
Page 419: ...Tab goes here and the next page should be GREEN Section 8 Schematics and Wiring Diagrams...
Page 420: ......
Page 422: ...Section 8 SR 2 Drawings 8 2 01 February 2005...
Page 424: ...Section 8 SR 2 Drawings 8 4 01 February 2005...
Page 425: ...8 5...
Page 426: ...8 6...
Page 427: ...8 7...
Page 428: ...8 8...
Page 429: ...8 9...
Page 430: ...8 10...
Page 431: ...8 11...