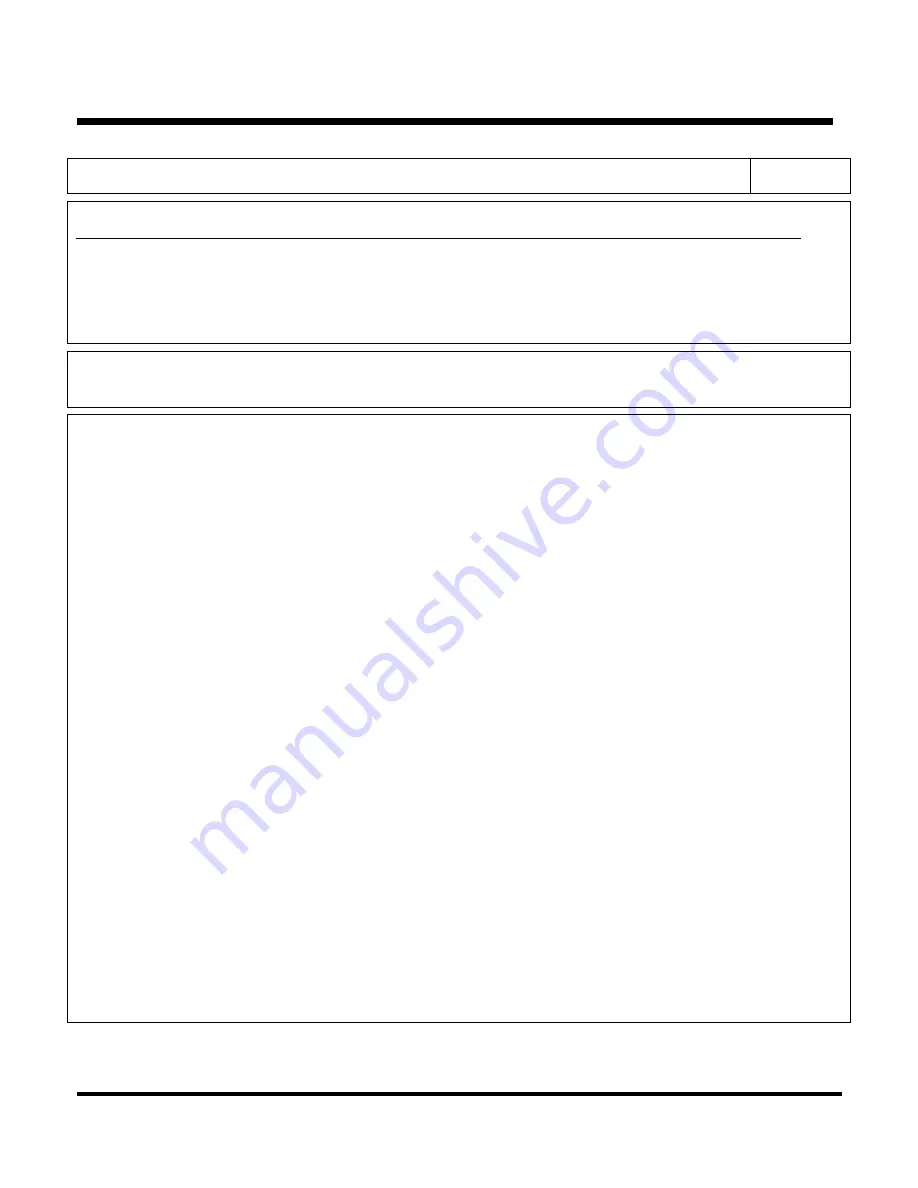
Section 5 – SR-2 Diagnostics
204 CHECK DISPLAY DISCHARGE AIR SENSOR
Page 2 of 2
How Alarm is Cleared
THIS ALARM CAN ONLY BE CLEARED FROM THE MAINTENANCE MENU or GUARDED ACCESS MENU.
When the alarm is cleared the return air sensors, discharge air sensors and evaporator coil sensor must all read
within a specified number of degrees of each other. If they do not, it is assumed that the sensor reading is not
accurate and the alarm code is not cleared. If the sensor is over or under range when the alarm clear is attempted,
the alarm will not be cleared. If Alarm Code 92 Sensor Grades Not Set is present, the sensor grade must be set
before the alarm can be cleared.
Programmable Features
This is a graded sensor. The sensor grade must be correctly set in the Guarded Access Menu.
Diagnostic Procedure
Download and review the ServiceWatch data logger using Technician Level to determine the conditions at the time
the alarm was set.
Alarm Code 204 (Sensor was out of range) Only
1. Display the sensor reading, using the Sensor Menu. If the display shows [----], the sensor is defective and
should be replaced. If the condition still exists, check the sensor circuit for an open wire or short to ground.
See Service Procedure D01A. Check the microprocessor using Service Procedure A01A.
2. If the display is normal proceed as shown below.
Alarm Code 204 and Alarm Code 13 (Sensor drifted or was reading erratically)
1. Review the ServiceWatch data logger and check the sensor reading at the time the alarm was set. Also,
review the history to see if previous alarm codes exist that would indicate an intermittent problem. If the
sensor appears to have read incorrectly, it should be replaced.
2. Be sure the sensor grades are set to the actual sensor grade and are not transposed.
3. Check for an airflow obstruction and correct sensor mounting.
4. If the problem reoccurs, check the sensor connector, as shown in Service Procedure D01A.
5. Check the sensor circuit, as shown in Service Procedure D01A.
Alarm Code 204 and Alarm Code 92 (Sensor grade set to 5H)
1. Verify and set the sensor grade.
Alarm Code 04, Alarm Code 204 and Alarm Code 13 set (Dual sensors don’t agree)
1. Review the ServiceWatch data logger and check the senor readings at the time the alarm was set. Also,
review the history to see if previous alarm codes exist that would indicate the problem sensor. If a sensor
appears to have read incorrectly, it should be replaced.
2. Check for an airflow obstruction and correct sensor mounting.
3. Be sure the sensor grades are set to the actual sensor gradeand are not transposed.
4. If the offending sensor cannot be determined, immerse both discharge air sensors simultaneously in an ice
bath to determine which sensor is inaccurate.
If all the Sensor Codes (02, 03, 04, 05, 06, 11 and 12, 203, & 204) are set
1. Be sure the 35 pin microprocessor sensor connector J3 is connected securely.
2. Check the microprocessor, as shown by Service Procedure A01A.
5-83
02 February 2005
Summary of Contents for SR-2 SmartReefer2
Page 4: ......
Page 7: ...Tab goes here and the next page should be GREEN Section 1 Safety...
Page 8: ......
Page 10: ...Section 1 SR 2 Safety Information 1 2 18 January 2005...
Page 14: ...Section 1 SR 2 Safety Information 1 6 18 January 2005...
Page 15: ...Tab goes here and the next page should be GREEN Section 2 Hardware Description...
Page 16: ......
Page 48: ...Section 2 SR 2 Hardware Description 2 32 31 January 2005...
Page 49: ...Tab goes here and the next 2 pages should be GREEN Section 3 Software Description...
Page 50: ......
Page 96: ...Section 3 SR 2 Software Description 3 46 31 January 2005...
Page 97: ...Tab goes here and the next page should be GREEN Section 4 Operation...
Page 98: ......
Page 181: ...Tab goes here and the next 2 pages should be GREEN Section 5 Diagnostics...
Page 182: ......
Page 266: ...Section 5 SR 2 Diagnostics 5 84 02 February 2005...
Page 267: ...Tab goes here and the next page should be GREEN Section 6 Service Procedures...
Page 268: ......
Page 270: ...Section 6 SR 2 Service Procedure Index Page 2 01 February 2005...
Page 282: ...Section 6 SR 2 Service Procedure A01B Page 6 P41RA01B 31 January 2005...
Page 298: ...Section 6 SR 2 Service Procedure A02A Page 12 P41RA02A 02 February 2005...
Page 318: ...Section 6 SR 2 Service Procedure A03B Page 4 P41RA03B 30 January 2005...
Page 338: ...Section 6 SR 2 Service Procedure A15A Page 4 P41RA15A 30 January 2005...
Page 360: ...Section 6 SR 2 Service Procedure A46B Page 8 P41RA46B 30 January 2005...
Page 366: ...Section 6 SR 2 Service Procedure A48A Page 6 P41RA48A 30 January 2005...
Page 376: ...Section 6 SR 2 Service Procedure A50A Page 6 P41RA50A 31 January 2005...
Page 394: ...Section 6 SR 2 Service Procedure F08A Page 4 P41RF08A 30 January 2005...
Page 398: ...Section 6 SR 2 Service Procedure F09A Page 4 P41RF09A 30 January 2005...
Page 402: ...Section 6 SR 2 Service Procedure G03A Page 4 P41RG03A 31 January 2005...
Page 406: ...Section 6 SR 2 Service Procedure H04A Page 4 P41RH04A 30 January 2005...
Page 407: ...Tab goes here and the next page should be GREEN Section 7 Service Information...
Page 408: ......
Page 410: ...Section 7 SR 2 Information 7 2 02 February 2005...
Page 419: ...Tab goes here and the next page should be GREEN Section 8 Schematics and Wiring Diagrams...
Page 420: ......
Page 422: ...Section 8 SR 2 Drawings 8 2 01 February 2005...
Page 424: ...Section 8 SR 2 Drawings 8 4 01 February 2005...
Page 425: ...8 5...
Page 426: ...8 6...
Page 427: ...8 7...
Page 428: ...8 8...
Page 429: ...8 9...
Page 430: ...8 10...
Page 431: ...8 11...