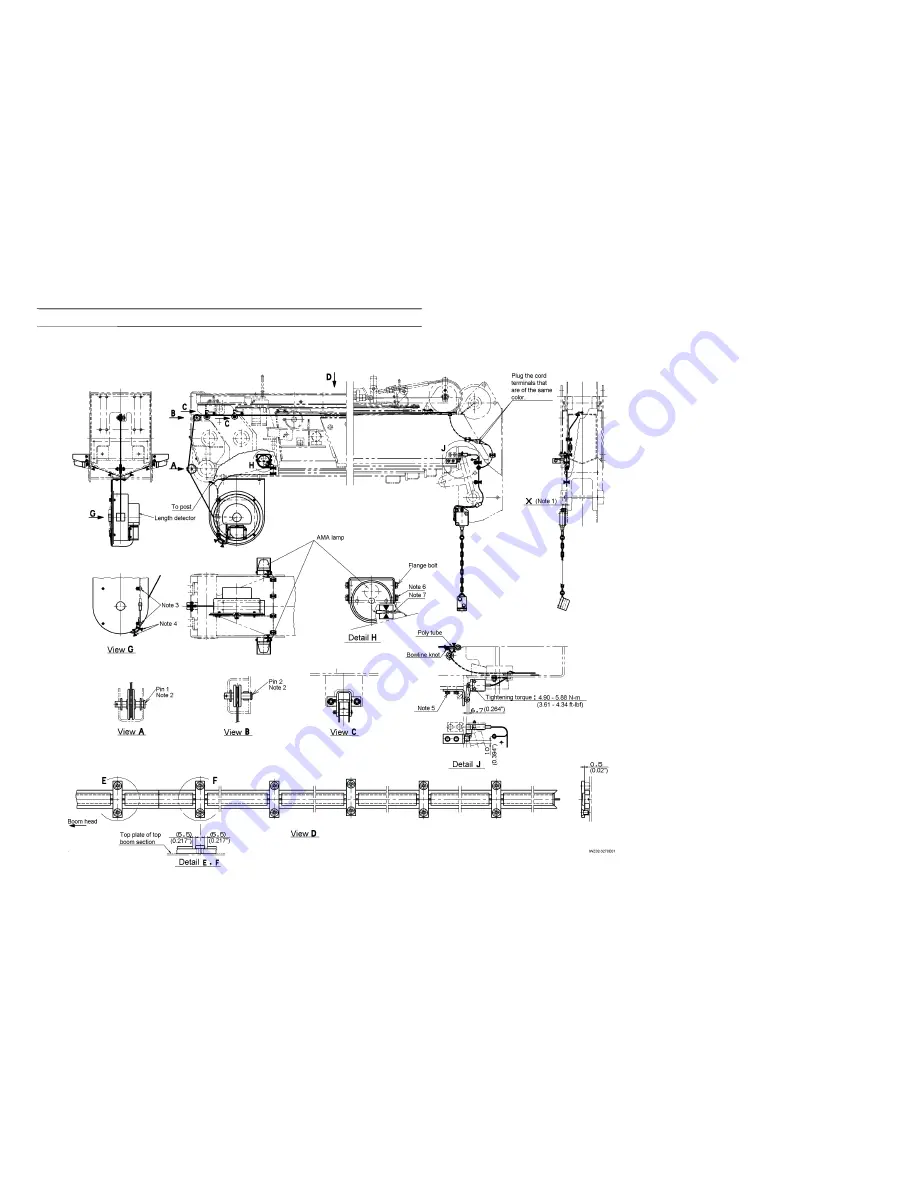
12
WZ02-3270E
12
Location of Electrical Parts
Z - 8
Z - 8
Z - 8
Z-8
Location of Electrical Parts
1. Boom
△
3
313-618-50000
Note:
1. Reduce size X as much as possible within the range where
the switch can be smoothly rotated.
2. Never apply grease to pins 1 and 2.
3. Clamp the wiring of the metal connector. ( In upper part, fix the
wiring from the post.)
4. Tighten both wirings for the SWP connector and the wirings
for the metal connector.
5. Adjust the switch to operate at 5 – 8mm (0.2 – 0.32in) before
the top boom retracted completely.
Apply LOCKTITE 262T on threads when install bolts.
6. Tighten the ground terminal and the flange bolt together.
(Only on right-side of boom)
7. Connect plug of lamp assy harness to the plug receptacles of
post side, and clamp remainder materials with fasteners.
Summary of Contents for TM-2000-1
Page 118: ...H 1 H 1 AMA Load Moment Indicator 1 W301 0270E H 1 AMA Load Moment Indicator 1 Structure...
Page 148: ...V 2 V 2 Radio control Valve 7 W135 0180E 1 2 Electric circuit...
Page 150: ...V 2 V 2 Radio control Valve 9 W135 0180E 1 4 Cross section...
Page 177: ...Location of Hydraulic Parts Z 7 Z 7 Z 7 10 WZ07 1810E 10 3 Outrigger 4 316 481 21001...
Page 183: ...16 WZ02 3270E 16 Location of Electrical Parts Z 8 Z 8 Z 8 4 Operation box 4 316 558 02000...
Page 185: ...18 WZ02 3270E 18 Location of Electrical Parts Z 8 Z 8 Z 8 5 2 Sub harness 1 316 557 30000...
Page 186: ...19 WZ02 3270E 19 Location of Electrical Parts Z 8 Z 8 Z 8 6 Frame Rear 0 314 803 36000...
Page 187: ...20 WZ02 3270E 20 Location of Electrical Parts Z 8 Z 8 Z 8 7 Vehicle 0 319 329 00000...
Page 188: ...Location of Electrical Parts Z 8 Z 8 Z 8 21 WZ02 3270E 21 8 Angle limit alarm 0 314 803 40000...
Page 190: ...Harness Z 9 Z 9 Z 9 23 WZ04 2600E 23 2 Harness Operation box 2 1 Harness 1 3 316 558 02300...
Page 191: ...Harness Z 9 Z 9 Z 9 24 WZ04 2600E 24 2 2 Harness 2 3 316 558 02100...
Page 192: ...Harness Z 9 Z 9 25 WZ04 2600E 2 3 Switch 3 313 612 23400...
Page 193: ...26 WZ04 2600E 26 Harness Z 9 Z 9 Z 9 3 Harness Radio controls 0 316 558 03600...