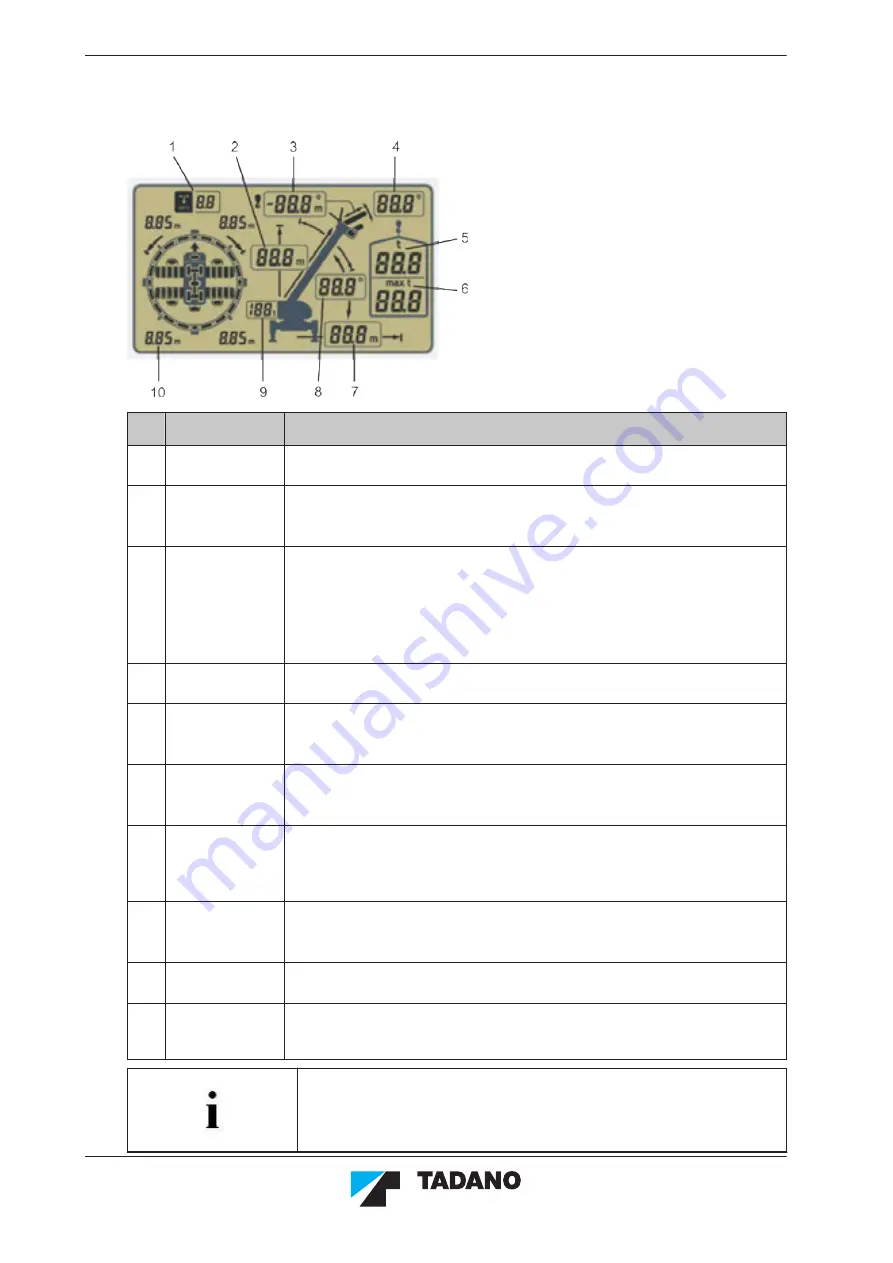
Numerical display
No. Display
Description
1
Wind speed dis‐
play
Indicates the wind speed.
2
Boom length
display
Indicates the boom length in the normal mode.
When the "Safety working range" function is activated or deactivated, the
corresponding height limits are displayed.
3
Luffing fly jib
length display
Indicates the luffing fly jib length (if the luffing fly jib mode is activated).
If you press the <Rope falls> key, "Pxx" will be displayed ("xx" stands for
the number of rope falls).
The lifting height is shown when the "Lifting height" switch is activated.
When the "Safety working range" function is activated or deactivated, the
upper limiting value for the boom angle is displayed.
4
Luffing fly jib an‐
gle display
Indicates the offset angle of the luffing fly jib (if the luffing fly jib mode is
activated).
5
Load display
Indicates the load in the normal mode.
In most display modes (e.g. in the luffing fly jib mode), "- - -" is displayed
here.
6
Rated load dis‐
play
Indicates the rated load in the normal mode.
In most display modes (e.g. in the luffing fly jib mode), "- - -" is displayed
here.
7
Working radius
display
Indicates the working radius in the normal mode.
In most display modes (e.g. in the luffing fly jib mode), "- - -" is displayed
here. When the "Safety working range" function is activated or deactivat‐
ed, the limiting value for the working radius is displayed.
8
Boom angle dis‐
play
Indicates the boom angle in the normal mode.
When the "Safety working range" function is activated or deactivated, the
lower limiting value for the boom angle is displayed.
9
Counterweight
display
Indicates the selected counterweight.
10
Outrigger beam
length display
(1–4)
No function in case of ATF 130G-5.
Numeric units are changed depending on the displayed information.
3 Operation
100
ATF 130G-5 2146097
2014-09
Summary of Contents for ATF 130G-5
Page 2: ......
Page 8: ...Table of Contents 8 ATF 130G 5 2146097 2014 09...
Page 30: ...2 General safety instructions 30 ATF 130G 5 2146097 2014 09...
Page 31: ...2 General safety instructions ATF 130G 5 2146097 2014 09 31...
Page 32: ...2 General safety instructions 32 ATF 130G 5 2146097 2014 09...
Page 33: ...2 General safety instructions ATF 130G 5 2146097 2014 09 33...
Page 50: ...2 General safety instructions 50 ATF 130G 5 2146097 2014 09...
Page 51: ...2 General safety instructions ATF 130G 5 2146097 2014 09 51...
Page 64: ...2 General safety instructions 64 ATF 130G 5 2146097 2014 09...
Page 68: ...3 1 3 Operating elements 3 Operation 68 ATF 130G 5 2146097 2014 09...
Page 101: ...3 Operation ATF 130G 5 2146097 2014 09 101...
Page 188: ...3 8 2 Outrigger Alarm displays 3 Operation 188 ATF 130G 5 2146097 2014 09...
Page 228: ...1 Counterweight cylinder 3 Operation 228 ATF 130G 5 2146097 2014 09...
Page 229: ...3 Operation ATF 130G 5 2146097 2014 09 229...
Page 236: ...Counterweight variant 31 7 t 69886 5 lbs 3 Operation 236 ATF 130G 5 2146097 2014 09...
Page 239: ...Counterweight variant 42 3 t 93255 5 lbs 3 Operation ATF 130G 5 2146097 2014 09 239...
Page 240: ...Mounting instruction 3 Operation 240 ATF 130G 5 2146097 2014 09...
Page 466: ...3 Operation 466 ATF 130G 5 2146097 2014 09...
Page 471: ...Boom 4 Crane testing instructions ATF 130G 5 2146097 2014 09 471...
Page 472: ...Stinger 4 Crane testing instructions 472 ATF 130G 5 2146097 2014 09...
Page 473: ...Boom end 4 Crane testing instructions ATF 130G 5 2146097 2014 09 473...
Page 474: ...Intermediate section 4 Crane testing instructions 474 ATF 130G 5 2146097 2014 09...
Page 484: ...4 Crane testing instructions 484 ATF 130G 5 2146097 2014 09...
Page 491: ...5 1 9 Wiring diagram 5 Rectifying the faults ATF 130G 5 2146097 2014 09 491...
Page 492: ...5 Rectifying the faults 492 ATF 130G 5 2146097 2014 09...
Page 493: ...5 Rectifying the faults ATF 130G 5 2146097 2014 09 493...
Page 494: ...5 Rectifying the faults 494 ATF 130G 5 2146097 2014 09...
Page 502: ...7 Service and Maintenance 502 ATF 130G 5 2146097 2014 09...
Page 510: ...7 0 General instructions 4 4 ATF130G 5 2010 12 0260_EN_FA046_7_00_00_00_FA036 DOC Notes...
Page 512: ...7 1 Maintenance intervals 2 14 ATF130G 5 2010 12 G 0265_EN_FA046B_7_01_00_00_FA029 doc Notes...
Page 521: ...Maintenance intervals 7 1 ATF130G 5 2010 12 0265_EN_FA046B_7_01_00_00_FA029 doc 11 14 Notes...
Page 522: ......
Page 523: ...Maintenance intervals 7 1 ATF130G 5 2010 12 0265_EN_FA046B_7_01_00_00_FA029 doc 13 14 Notes...
Page 524: ...7 1 Maintenance intervals 14 14 ATF130G 5 2010 12 0265_EN_FA046B_7_01_00_00_FA029 doc Notes...
Page 536: ...7 2 Engine 12 12 ATF130G 5 2013 11 0270_EN_FA046B_7_02_00_00_FA029 ab FZ 066 doc Notes...
Page 566: ...7 7 Electrical system 12 12 ATF130G 5 2010 12 0295_EN_FA046B_7_07_00_00_FA029 DOC Notes...
Page 570: ...7 8 Crane cab 4 4 ATF130G 5 2010 12 0300_EN_FA046_7_08_00_00_FA029 DOC Notes...
Page 580: ...7 10 Compressed air system 6 6 ATF130G 5 2010 12 0307_EN_FA046_7_10_00_00 DOC Notes...
Page 588: ...8 Annex Manufacturer s documents 588 ATF 130G 5 2146097 2014 09...
Page 602: ...8 Annex Manufacturer s documents 602 ATF 130G 5 2146097 2014 09...
Page 614: ...8 Annex Manufacturer s documents 614 ATF 130G 5 2146097 2014 09...
Page 615: ...Application Letter EAI S MTU C I Agriculture 2011 001...
Page 616: ...Application Letter EAI S MTU C I Agriculture 2011 001...
Page 617: ...Application Letter EAI S MTU C I Agriculture 2011 001...
Page 618: ...Application Letter EAI S MTU C I Agriculture 2011 001...
Page 619: ...Application Letter EAI S MTU C I Agriculture 2011 001...
Page 620: ...Application Letter EAI S MTU C I Agriculture 2011 001...
Page 622: ...8 Annex Manufacturer s documents 622 ATF 130G 5 2146097 2014 09...
Page 632: ...8 Annex Manufacturer s documents 632 ATF 130G 5 2146097 2014 09...