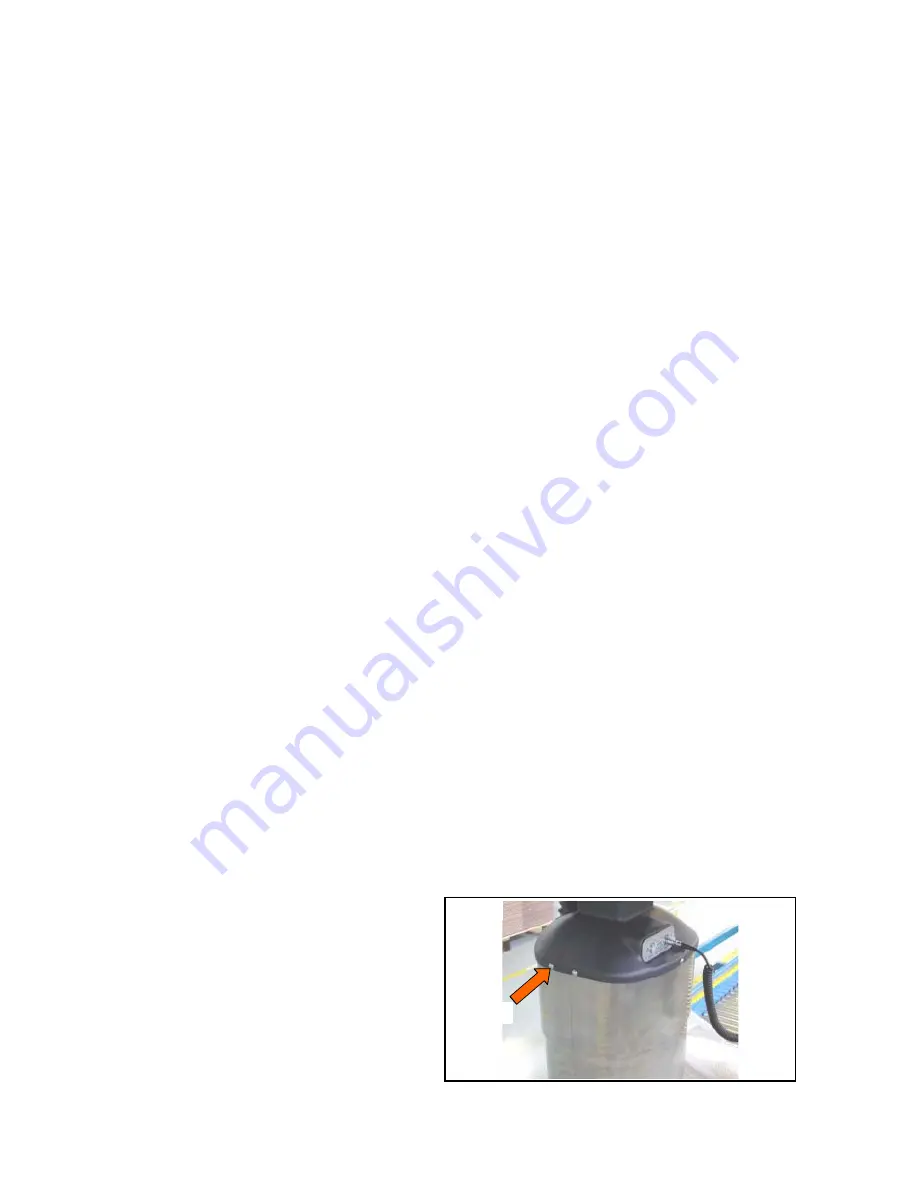
7-2
764333-268
0.001 inches. Some components may fail in a
hazardous way if subjected to particles greater than
100 microns, or 0.004 inches.
Precautions must be taken when servicing the
hydraulic system. Working in the field is not the ideal
situation, but being aware of the need for maintaining
system cleanliness, using common sense and good
practices, and being dedicated to contamination
control should lead to success. However, if
contamination is suspected, purge system as indicated
in
7.2.2 Work Place
The Operating Room would be the ideal place to
perform hydraulic service, but a maintenance area or
some other “back room” is the more probable location.
Avoid, at all costs, working in or next to a room where
any woodworking is carried out. Almost as bad is an
area where metal work, especially grinding, is done.
The airborne particles generated by these or other
similar operations are devastating and uncontrollable.
If you have no choice, at least ensure no such activities
have been performed there for several hours and none
occur during servicing.
Try to work in a place with no nearby doors through
which people are continually passing. The less people-
traffic around you, the better. Stay away from heating
and cooling vents that also put particulates into the air.
7.2.3 Tools
Tools, gauges, hydraulic plugs, caps, etc., must be
extremely clean during servicing. Clean tools with a
lint-free cloth if possible. Hands and fingernails must
also be clean when handling hydraulics. Scrub
fingernails with a brush.
Always place tools and parts on a clean surface as work
is being done. And, of course, no smoking, eating or
drinking when working with hydraulics.
7.2.4 General Procedures
Wipe all components to be serviced, and areas adjacent
to them, with a clean, lint-free cloth.
•
Breaking connections -
If connection is to remain
broken for any length of time, both ends of connection
must be plugged or capped with clean parts. If this is
impractical, at least cover open port with a clean, lint-
free cloth. A rubber band can be used to hold cloth in
place.
•
Removing components -
When a component is
removed, place it on, and cover it with a clean, lint-
free towel.
•
Handling parts -
Try to handle all hydraulic
components by touching only those surfaces which
do not interact with hydraulic system oil.
•
Assembling -
Examine all surfaces coming into
contact with hydraulic system oil (wetted surfaces).
Any visible particles (i.e., 0.002 inch or more in
diameter) must be removed. Also examine O-rings
and O-ring seats for scratches and/or tears, as well
as contamination.
Be careful any critical surfaces do not unnecessarily
touch anything during assembly.
Ensure all fittings, valves, etc., are torqued per
specifications.
•
Completing work -
Clean external surfaces of work
area as before. Any leaks are more easily detected
if all areas are clean before checking.
• Perform sensor calibration after servicing
articulating components.
When the work is complete, verify the table functions
normally ... not only the function that was repaired,
but all functions.
7.3 TABLE COLUMN COVER
ASSEMBLY
To gain access to most of the Cmax Surgical Table
hydraulic and electrical components, the Table
Column Cover (or shroud) and/or Table Base Cover
must be removed. Remove the stainless-steel Table
Column shroud as follows:
1. Lower table for easier access.
2. Remove and save six top cover screws
3. Raise table to highest position to gain access to
lower cover screws.
4. Pry open covers with flat screwdriver.
5. Remove and save four lower cover screws (see
Figure 7-2).
6. Remove and set safely aside in place to prevent
damage.
Figure 7-1. Table Column Top Cover Screws
w
Screw
Summary of Contents for Cmax
Page 1: ......
Page 4: ......
Page 65: ......
Page 142: ...Page 3 of 14 ...
Page 148: ...Page 9 of 14 ...
Page 149: ...Page 10 of 14 ...
Page 155: ...Page 2 of 2 Figure 1 Second Spacer ...
Page 164: ......
Page 211: ......
Page 212: ......
Page 213: ......
Page 214: ......
Page 215: ......
Page 216: ......
Page 217: ......