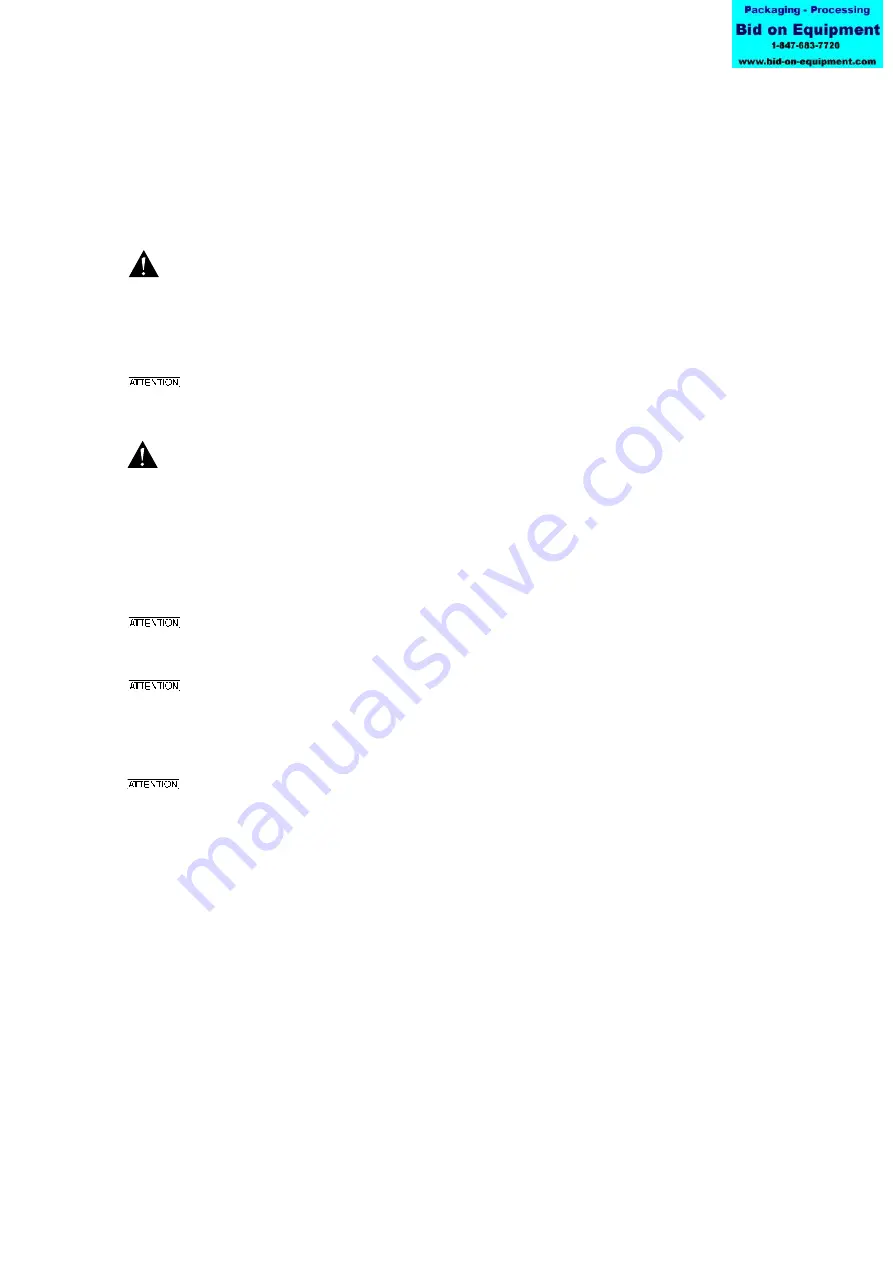
17
A.0500.251 – IM-TL/13.00 EN (08/2009)
2.3 System design and installation
When a pump is to be incorporated in a system, it is considered good practice to, as
far as possible, minimise the length of the pipes and the number of pipe fittings (tees,
unions, bends etc.) and the restrictions. When designing the suction lines, particular care
should be taken. These should be as short and straight as possible, using a minimum of
pipe fittings to achieve a good product flow to the pump. Always consider the following
when designing a system:
1. Ensure there is space enough around the pump to allow for:
a) Routine check and maintenance of the complete pump unit, seal area, drive motor,
etc.
b) Good ventilation for the drive to avoid overheating.
2. Both the suction and the discharge ports must be provided with valves. During check-
up procedures or maintenance work, the pump must be isolated from the system.
3. The system design, pipes and other equipment must have independant supports to
avoid heavy loads on the pump. In the case of pipe work or other equipment relying
on the pump fixings for support, there is a big risk for serious damage to the pump.
4. For positive displacement pumps as TopLobe it is recommended to install some
safeguards, for example:
a) Built-on safety relief valves
b) External pressure relief valve system for recirculation to tank or suction side of
the pump.
c) Torque device in the system, mechanical or electrical.
d) Rupture disc in the discharge pipework.
If the system can be ruined by reversed flow direction, safeguards must be considered
for both directions of rotation/flow.
5. It is considered good practice to thoroughly clean all pipework and associated
equipment from the suction port to the discharge port before installation of pump.
This is to avoid the risk of debris entering the pump and causing damage.
6. If possible, pressure gauges should be placed at the suction port and the discharge
port of the pump, so that the system pressures can be monitored. These gauges give a
clear indication of changes in the operating conditions. If a relief valve is
incorporated in the system the gauges will be necessary for setting and checking the
function of the valve.
7. It is very important that the suction condition at the pump inlet meets the NPSH
required of the pump. Failure to observe this can cause cavitation, which leads to a
noisy operation, reduced flow and mechanical damage on the pump and associated
equipment.