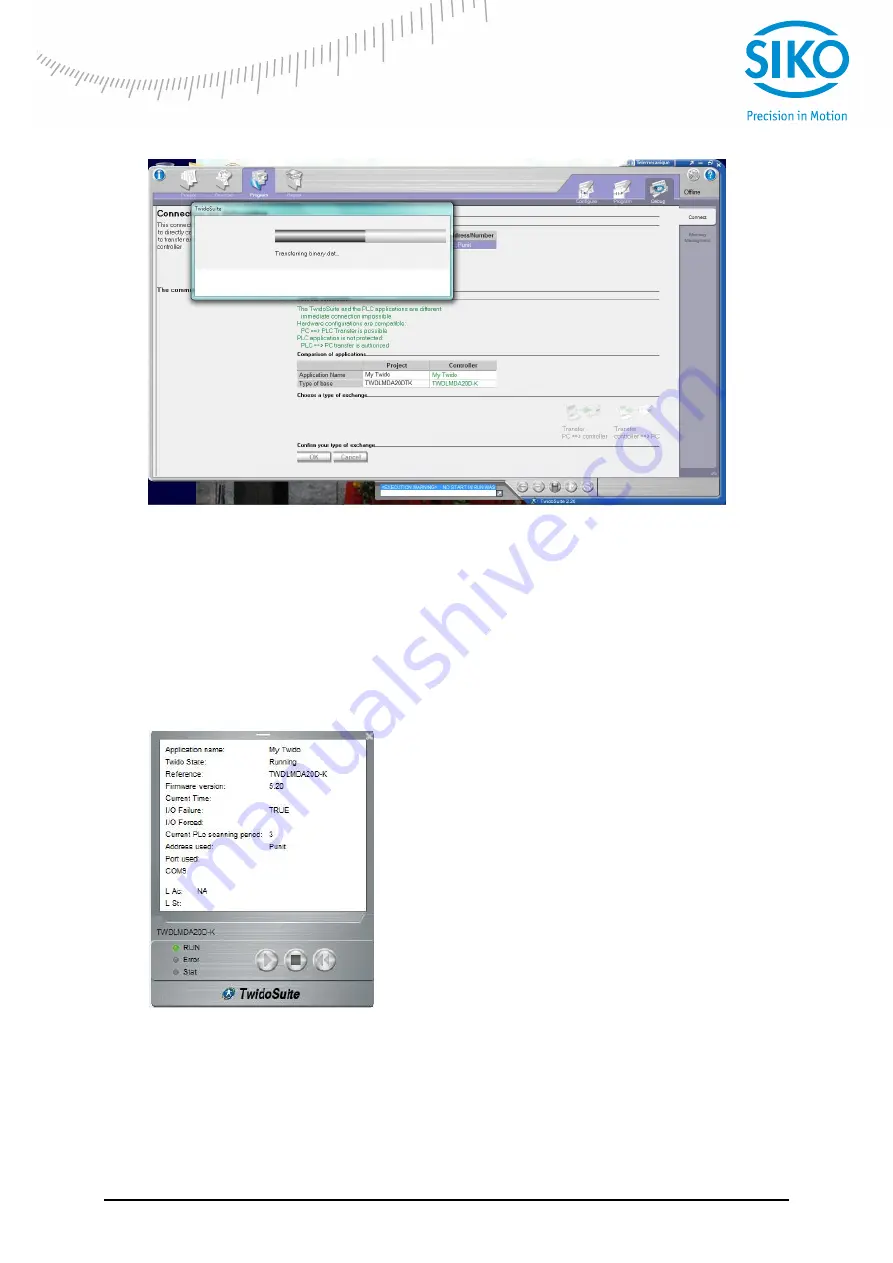
IK360 -CAN
x
Date: 23.01.2017 Page 24 of 41 Art.no. 86089 Mod. Status 10/17
Creating a backu
p of the controller parameters before going into online mode…….
Once the controller goes into the online mode, the PDOs cannot be changed. But, we can
program the SDOs as need arises.
6.5
Run
Once debugged, the controller goes into online mode. After we can program the SDOs if
needed and then run the controller.
Upon start up, we can create an animation table to monitor the necessary controller parameters
and the system variables, which contain the position value. Now we will program the PLC in
order to obtain the position values.