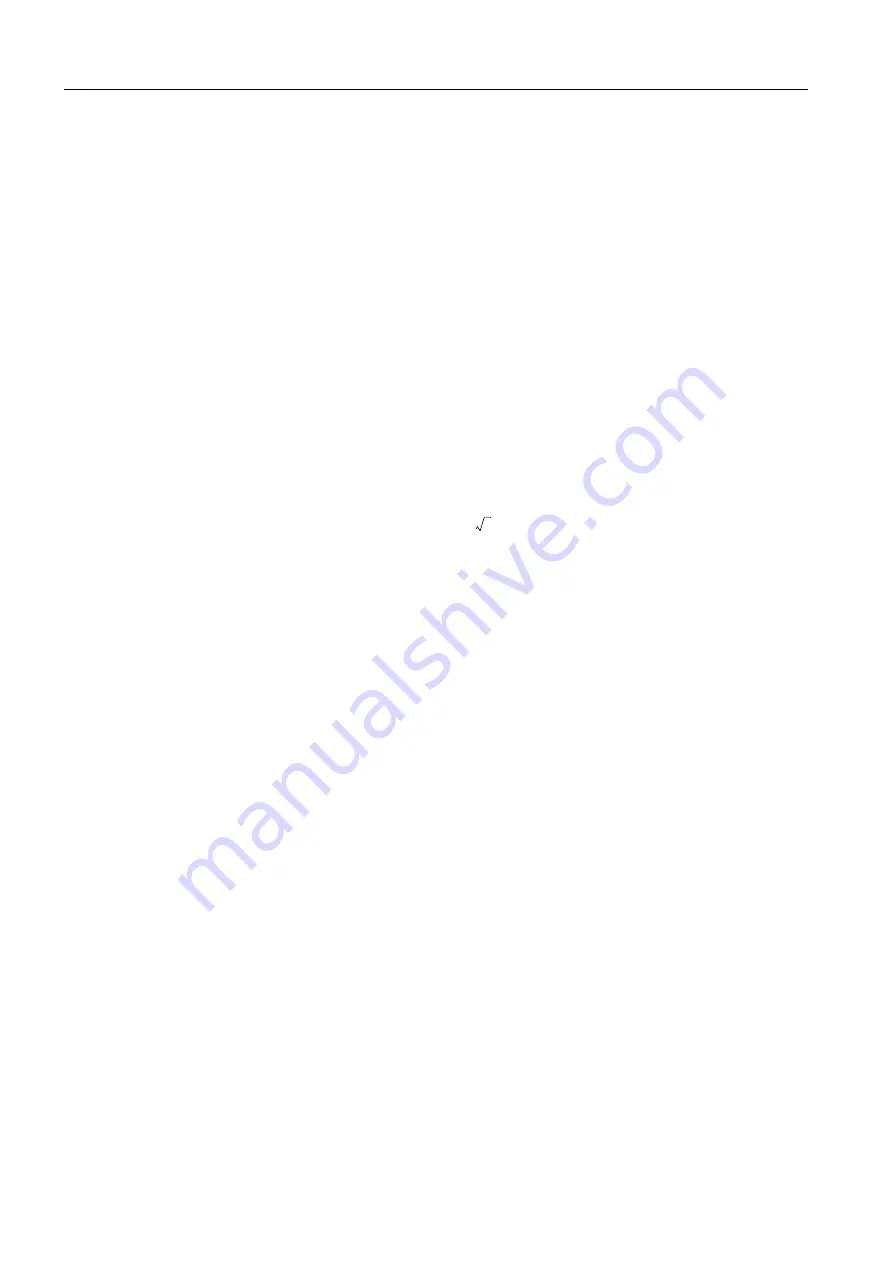
3RU11, 3RB10, and 3RB12 overload relays
SIRIUS System Manual
4-10
GWA 4NEB 430 0999-02b
Heavy starting
Heavy starting is when the motor requires longer than 10 seconds to reach
the nominal speed. Given such long starting times, the switching devices
and capacities have to be configured appropriately because the thermal load
increases. The permissible AC-3 currents of motor contactors only take into
account 10-second starts. In the case of longer starting times, derating
must be carried out or a larger contactor used. You can determine the corre-
sponding configuration on the basis of the tables of different starting times
and motor currents in part 4 of the low-voltage switching technology (NSK)
catalog.
Setting ranges with
thermal overload relays
The setting ranges can be used up to the maximum value when there are
temperatures of up to 60 °C inside the cubicle. At temperatures of 60 °C to
70 °C, derating is required. In other words, the maximum permissible set
value must be reduced. The reduction at 70 °C is 13 % and thus so negligi-
ble that due to the overlapping of the different current setting ranges no
gaps occur between the setting ranges. A uniform current range of 0.11 to
87 A can thus also be used at 70 °C.
Overload relays in star-
delta combinations
When overload relays are used in star-delta combinations, it must be taken
into consideration that only
of the motor current flows through the
line contactor. An overload relay built onto the line contactor must be set to
this level (i.e. 0.58 of the motor current). A second overload relay must be
built onto the star contactor if your load is to receive optimal protection in
star operation as well. The star current is
of the rated current of the
motor. The corresponding overload relay must be set to this current. The
3RB12 electronic overload relays with internal ground fault detection are not
suitable for use in star-delta combinations, since transient current spikes
occur at switchover from star to delta operation. These can result in the trig-
gering of ground fault detection.
3RU11 thermal overload relays
Description
• Tripping class 10
• For motor currents of up to 100 A
• For three-phase, single-phase, or DC motors
• Insensitive to "untidy" power systems
Thermal, time-delayed overload relays are the usual way of providing motor
protection with overload relays. The technology has been tried and tested
and continuously improved over a period of decades. They are reasonably
priced and provide reliable protection, particularly in the case of normal
starting times (class 10) and motor ratings of up to 45 kW (100 A).
Thermal overload relays work with bimetals and heater coils through which
the motor current flows. Thermal overload relays record true root-mean-
square values and direct currents as a result of their current measuring
method (Joule heat). Compatible heating coils and bimetals are used for the
different setting ranges. Single-phase and direct-current motors can also be
protected against overload by looping the motor line. Thermally time-
delayed overload relays can also be used after frequency converters.
1
3
⁄
1 3
⁄