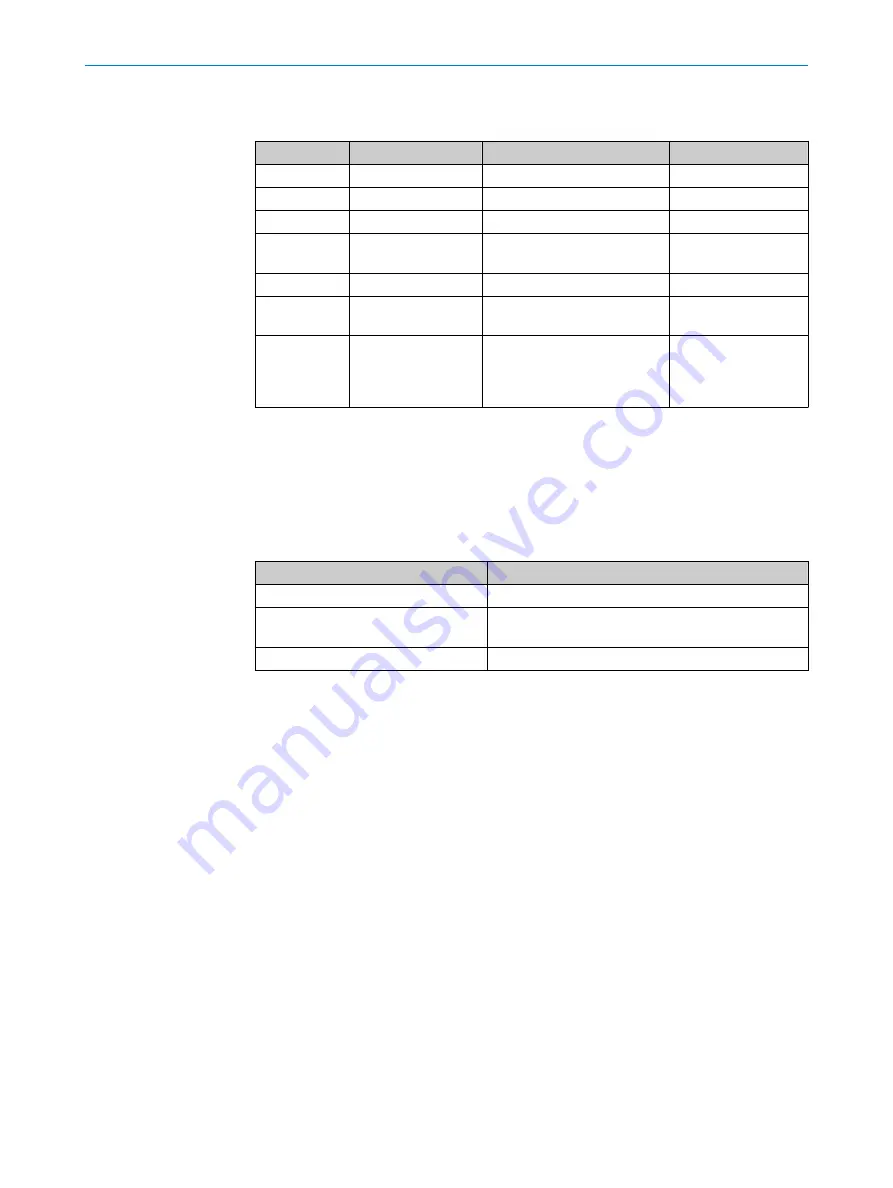
Recommended components for the interface circuit are set out in
.
Table 5: Components of the interface circuit with two core cable (integrated in cable)
Component
Part
Manufacturer
C1
Ceramic capacitor
100 nF
C2
Ceramic capacitor
2.2 µF, 16 V
C3, C4
Ceramic capacitor
470 nF, 50 V
L1, L2
Choke coils
744043101, 100 µH
ELL6SH101M, 100 µH
Würth Elektronik
Panasonic
R1, R2
Resistors
56R
U2
RS485 transceiver
SN65LBC176A
SN75LBC176A
Texas Instruments
Texas Instruments
TR1
Transformer
PE-68386NL
78602/1C
B78304B1030A003
78602/1C
Pulse Engineering
Murata
Epcos
Epcos
4.1.3
Motor feedback voltage supply
Motor feedback systems with HIPERFACE DSL
®
have been developed for operation with
a supply voltage of 7 to 12 V. The voltage supply is measured at the encoder plug con‐
nector.
below describes the specification for the power supply.
Table 6: Voltage supply
Parameter
Value
Switch-on voltage ramp
Max. 180 ms from 0 to 7 V
Inrush current
Max. 3.5 A (0 to100 µs)
Max. 1 A (100 µs to 400 µs)
Operating current
Max. 250 mA at 7 V
4.1.4
Interface circuit design recommendations
show the two different interface circuits depending on the chosen
system configuration. The following recommendations help in attaining a system design
optimized for transmission robustness.
•
During PCB design a good RF isolation for the interface circuit shall be achieved
against the motor power circuit.
•
The two sides of the transformer TR1 have to be well separated from each other to
avoid crosstalk.
•
Inside the servo controller the DSL-signal lines shall be routed as short as possible
and with good symmetry in the differential part. To avoid or reduce signal distur‐
bances by EMC-noise it is recommended to place this circuit as close as possible
to the connection point of the DSL-lines.
•
During PCB layout design also assess and avoid potential EMC-noise coupling
from brake lines as well as the brake power supply circuit.
•
For the encoder power supply via L1/L2 a star connection to a very low impedance
point is important. Both inductances shall be well matched to each other to avoid
differential mode noise. Self-resonance frequency should be of at least 10 MHz. A
common mode filter between L1/L2 and the supply voltage can improve robust‐
ness.
•
The DSL-line impedance is matched balanced by 2 x 56 Ohm. C2 grounds remain‐
ing common mode noise after the transformer; RF parts shall be used or different
types paralleled to get low impedance on a broader frequency range. PCB design
HARDWARE INSTALLATION
4
8017595/ZTW6/2018-01-15 | SICK
T E C H N I C A L I N F O R M A T I O N | HIPERFACE DSL
®
17
Subject to change without notice