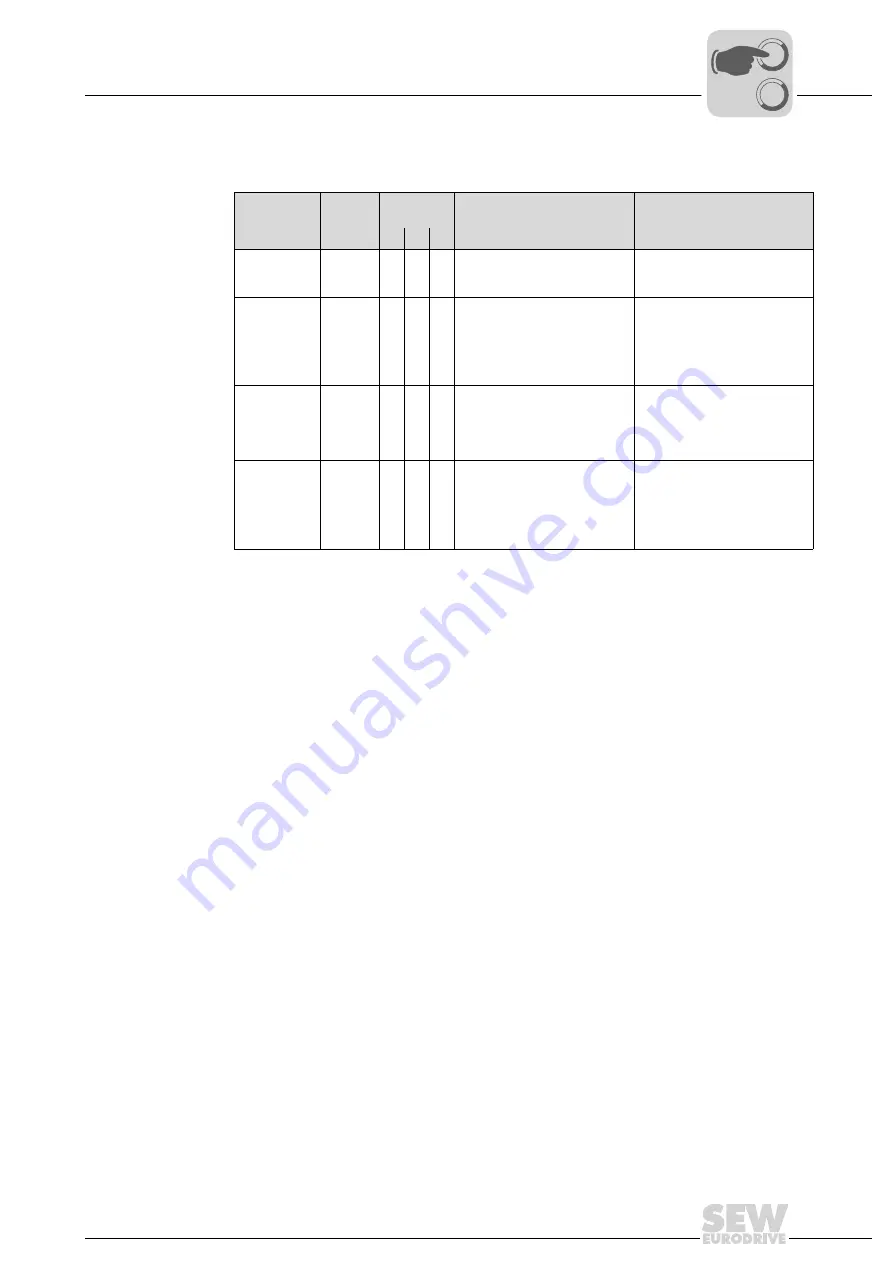
8
Operation
MOVIFIT® SC operating displays
Operating Instructions – MOVIFIT
®
SC
113
BUS-F LED (red)
The BUS-F LED displays the physical state of the bus node. The functionality is
described in the following table:
Status
LED
Function
level
Meaning
Troubleshooting
C
T
S
Error active
state
Off
•
•
The number of bus errors is
within the normal range
(error active state)
–
DUP-MAC
test
Flashing
red
(125 ms
cycle)
•
•
The unit is performing a
DUP-MAC check and
cannot send any messages
because no other partici-
pants are connected to the
bus (error passive state).
•
Switch on at least one
more station if no other
stations are switched on
Error
passive state
Flashing
red
(1 s
cycle)
•
•
The number of physical bus
errors is too high. No more
error telegrams are actively
written to the bus (error
passive state).
•
Check the wiring and the
terminating resistors if this
error occurs during opera-
tion (i.e. during ongoing
communication)
Bus-Off state
Red
•
•
Bus-Off state
•
The number of physical bus
errors has increased
despite a switch to the
error-passive state. Access
to the bus is deactivated.
•
Check the wiring, termi-
nating resistors, baud rate
and addresses (MAC-ID)
•
Valid for selected function level:
C = Function level "Classic"
T = Function level "Technology"
S = Function level "System"
0
0
I
Summary of Contents for MOVIFIT SC series
Page 2: ...SEW EURODRIVE Driving the world ...
Page 146: ......