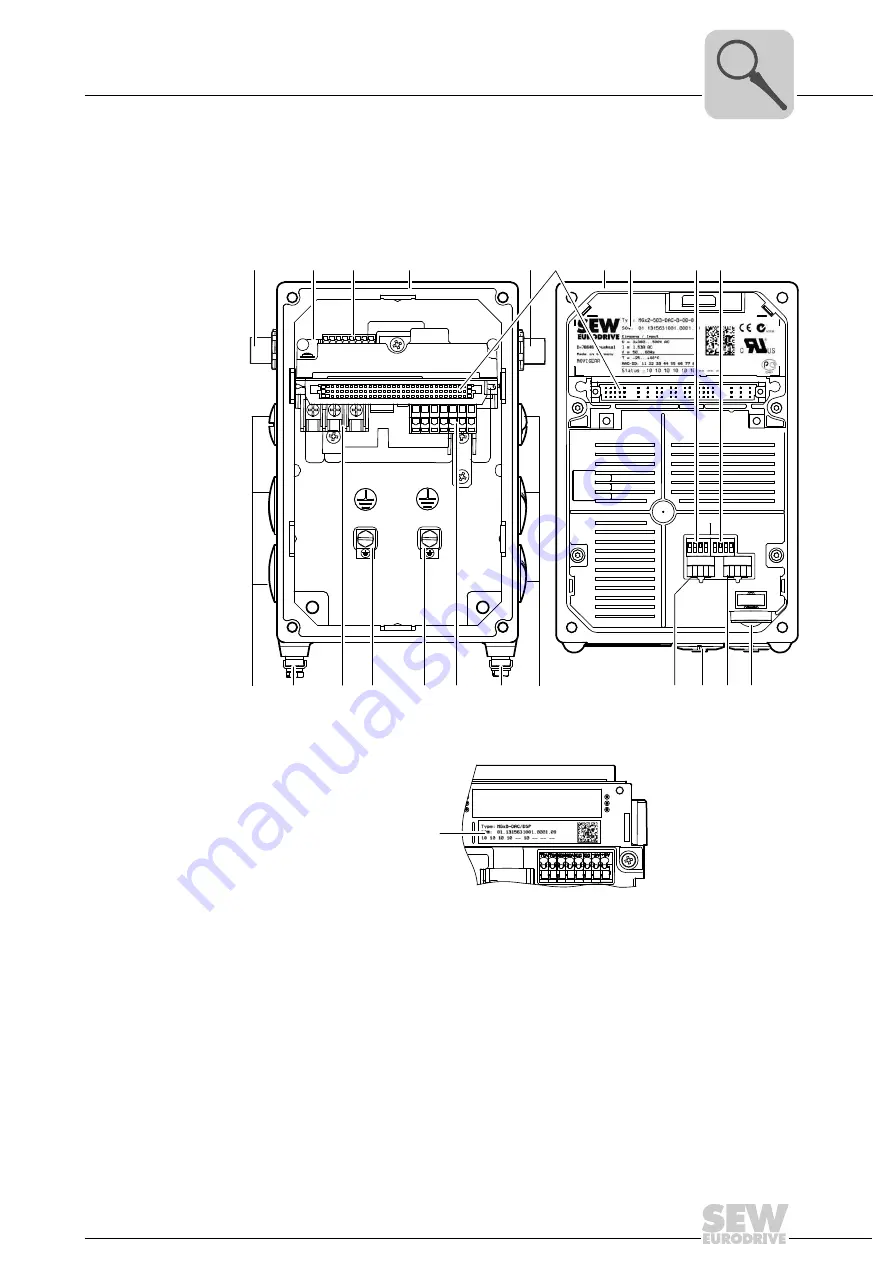
Operating Instructions – MOVIGEAR® DAC-B
17
3
MOVIGEAR
®
electronics
Unit Design
3.6
MOVIGEAR
®
electronics
3.6.1
MOVIGEAR
®
electronics cover (inside) and connection box
The following figure shows the connection box and the bottom side of the MOVIGEAR
®
electronics cover:
2366107275
[1]
AS-Interface connection
[2]
Nameplate of drive unit, see following detailed view
2584957963
[3]
AS-Interface terminals (wired to plug connector)
[4]
Connection ring
[5]
AS-Interface sensors
[6]
Plug connector connection unit for MOVIGEAR
®
electronics cover
[7]
MOVIGEAR
®
electronics cover
[8]
Electronics cover nameplate
[9]
DIP switches S1/1 – S1/4
[10] DIP switches S2/1 – S2/4
[11] Cable glands
[12] Screw for PE connection
[13] Supply system connection L1, L2, L3
[14] Electronics terminal strips
[15] Switch t1 for integrator ramp (green)
[16] Diagnostic interface (below screw fitting)
[17] Setpoint switch f2 (white)
[18] Setpoint potentiometer f1 with screw plug
34567
34567
ON
ADE04SA
1
2
3
4
ON
ADE04SA
1
2
3
4
t1
S1
S2
f2 f1
1 2 3 4
1 2 3 4
[3]
[4]
[2]
[1]
[5]
[12]
[11]
[12]
[12]
[12]
[11]
[14]
[13]
[10]
[9]
[6]
[7]
[8]
[15] [16] [17] [18]
[2]
Summary of Contents for MOVIGEAR DAC B
Page 2: ...SEW EURODRIVE Driving the world...
Page 257: ......