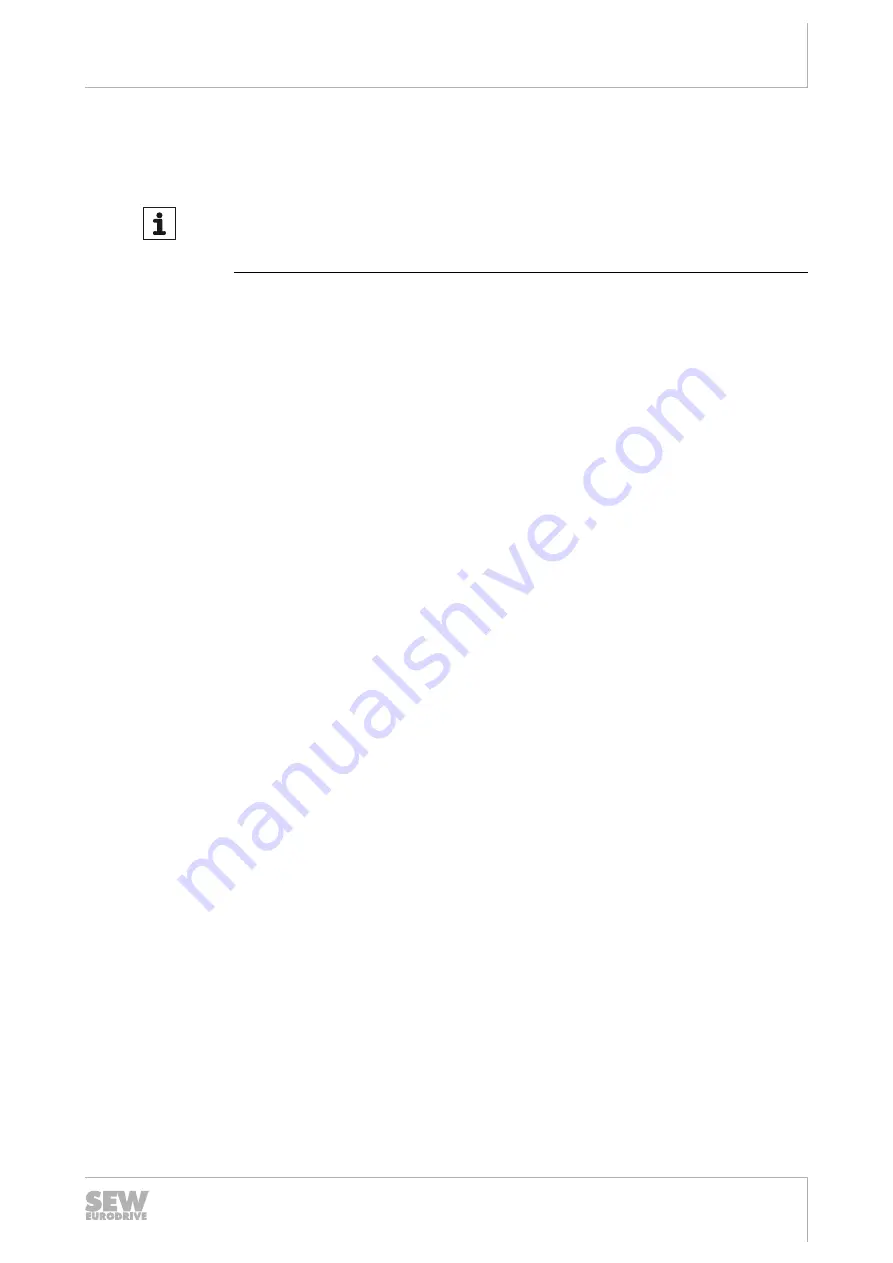
6
Electrical installation
Wiring check
Manual – EtherCAT
®
Interfaces, Field Distributors
65
6.12
Wiring check
INFORMATION
For ensuring the isolation and the effectiveness of preventive measures, you have to
perform the checks of the valid and applicable standards (e.g. EN 60204-1 or
EN 61800-5) after any wiring work for installation, conversion, repair, etc.
In order to prevent injury to persons or damage to the plant, check the wiring as des-
cribed below before you connect the voltage supply for the first time:
•
Remove all fieldbus interfaces from the connection module.
•
Disconnect all MOVIMOT
®
inverters from the connection module (only with MFZ.7,
MFZ.8, MFZ.9).
•
Disconnect all plug connectors of the motor connection (hybrid cable) from the
field distributor.
•
Check the insulation of the wiring in accordance with applicable national stand-
ards.
•
Check the grounding.
•
Check the insulation between the supply system cable and the DC 24 V cable.
•
Check the insulation between supply system cable and communication cable.
•
Check the polarity of the DC 24 V cable.
•
Check the polarity of the communication line.
•
Check the mains phase sequence.
•
Ensure equipotential bonding between the fieldbus interfaces.
6.12.1
After the wiring check
•
Connect and fasten all motor connections (hybrid cable).
•
Plug in and fasten all fieldbus interfaces.
•
Install and fasten all MOVIMOT
®
inverters (only with MFZ.7, MFZ.8, MFZ.9).
•
Install all connection box covers.
•
Seal any plug connections not in use.
25809148/EN – 01/2019