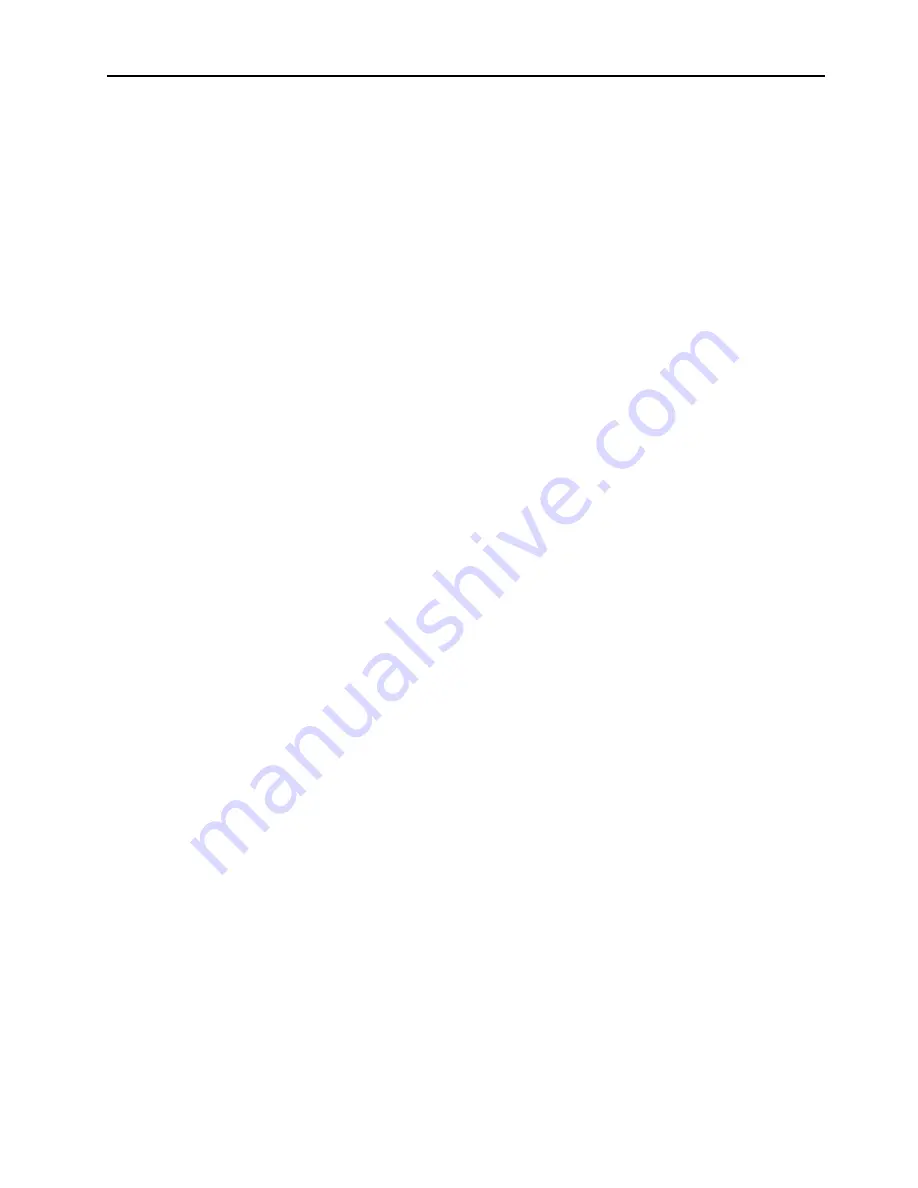
l
F.8L Falco Construction Manual
9–5
Revision 4, March 1, 2002
The method you will use is to complete the assembly to a point at which the plywood skin has
been glued on the top or bottom of the wing and the second skin has been cut and fitted
accurately but has not yet been glued down. All glue lines for attaching the second skin must be
located, marked off, and protected from contamination with finish either by covering them
temporarily with masking tape or by special care in applying the finish. Finish is then applied to
all interior surfaces except the glue lines and allowed to dry. The masking tape, if used, is then
removed and the second skin is carefully glued in place.
Any inaccuracy in locating and adjusting glue lines may produce weak glue joints. The normal
practice for homebuilders is to mark off the last skin to be installed with a pencil. This is
normally held in place with “alignment pins”, a nice way of saying
nails
. Two small nails can be
used to accurately locate the skin at exactly the required position.
Care should be exercised in the choice of materials used for marking the wood. Grease-pencil and
marking crayons containing wax are 4harmful to the finish. Ordinary soft graphite pencils and
common stamp-pad inks made with water-soluble dyes may be used safely.
Flush-driven nails or screws left in the exterior surface to be finished are likely to prove points of
premature failure of the finish, and this would also apply to the interior finish. The finish usually
cracks over the junction of wood and metal and the failure progresses from the crack. This
requires that the nail or screw heads be taped after application of varnish.
Nail holes left from nail-strip gluing or countersunk nails or screws should be filled before further
finish is applied. Holes in woods on which the wood filler is applied should be filled sufficiently to
protect the wood and the durability of the finish, but filler alone will not make them level enough
to be entirely concealed from view. Very small holes may be leveled after the application and
sanding of a surfacer. On woods having no pores large enough to require wood filler, and where
slight depressions in the finish over nail holes will be acceptable, wood filler may be applied over
the areas in which there are nail holes only. This may be done most easily on the bare wood
before varnish is applied.
When seams in face veneers of plywood have been well glued with water-resistant glue, they have
no effect on the behavior of the finish. The finish should remain as intact over the seam as it does
over the parts of the surface having no seams, except where glue squeeze-out occurs.
Under Metal Fittings
One of the most critical places is under metal fittings. Whenever a wood airplane has rot, it is
almost always under such a fitting. The fittings are always there for a purpose—to carry a load.
This load causes the fitting to move, if it can. This causes the finish to crack. Worse yet is the
fact that water is frequently trapped between a fitting and the wood. Moisture will collect in such
a place by capillary action.
The best solution is to bed the fitting down in a substance that will exclude moisture from
becoming trapped between the fitting and the wood. The type of sealant to be used will depend
on the nature of the fitting. Does the fitting ever have to be removed?
If the fitting is permanently installed in the airplane (such as the channel-nuts) then epoxy may
be brushed over the entire part. If the fitting may be removed on very infrequent occasions, then
a pliable adhesive may be used. Silicon rubber RTV compound is a good choice. 3M makes a
long list of suitable sealers.
Summary of Contents for F.8L Falco
Page 1: ...F 8L Falco Construction Manual...
Page 7: ...l F 8L Falco Construction Manual Revision 4 March 1 2002...
Page 21: ...l F 8L Falco Construction Manual 1 8 Revision 4 March 1 2002...
Page 29: ...l F 8L Falco Construction Manual 2 8 Revision 4 March 1 2002...
Page 43: ...l F 8L Falco Construction Manual 5 4 Revision 4 March 1 2002...
Page 65: ...l F 8L Falco Construction Manual 9 6 Revision 4 March 1 2002...
Page 81: ...l F 8L Falco Construction Manual 10 16 Revision 4 March 1 2002...
Page 109: ...l F 8L Falco Construction Manual 15 4 Revision 4 March 1 2002...
Page 133: ...l F 8L Falco Construction Manual 17 10 Revision 4 March 1 2002...
Page 145: ...l F 8L Falco Construction Manual 18 12 Revision 4 March 1 2002...
Page 173: ...l F 8L Falco Construction Manual 21 10 Revision 4 March 1 2002...
Page 229: ...l F 8L Falco Construction Manual 23 40 Revision 4 March 1 2002...
Page 387: ...l F 8L Falco Construction Manual 28 26 Revision 4 March 1 2002...
Page 393: ...l F 8L Falco Construction Manual A 6 Revision 4 March 1 2002...