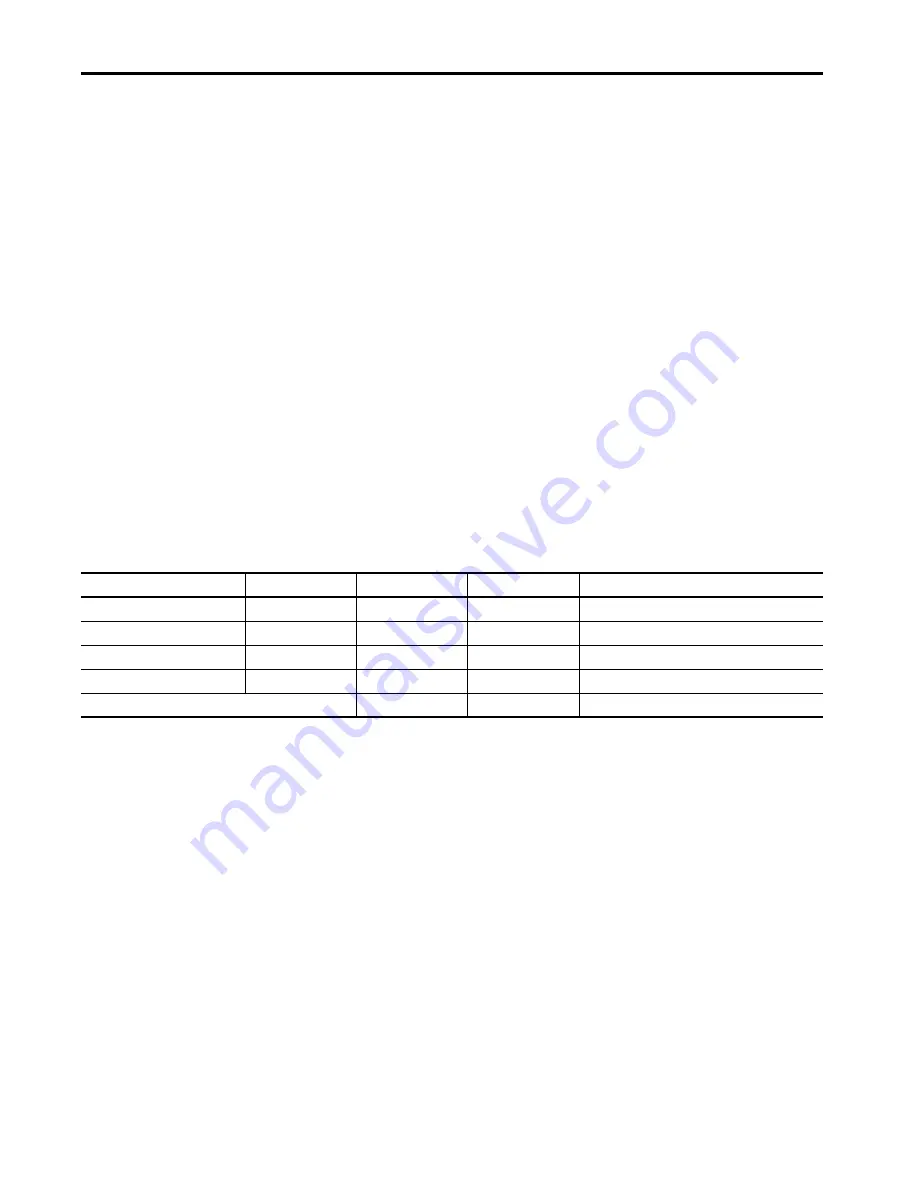
Rockwell Automation Publication IASIMP-QS005H-EN-P - April 2016
23
Risk Assessment and System Design
Chapter 1
Safety Specification Example for Robot Cell Application
To adequately describe the system, its equipment, sequence of operation, operating modes, and the detailed functional
and physical specifications of each station must be documented.
Load Station #1
An analysis of Load Station #1 yields the following information.
Part weight:
3 lbs
Loading Frequency:
8…12 parts per minute
Task:
The operator removes parts from the transfer rack and places the part into Load Station #1 (A). When the part is
in position, the operator initiates the part ready sequence. The operator is also responsible for repositioning any miss-
picked parts, moving empty racks out of the way, and moving full racks into position for loading. Maintenance personnel
adjust and repair fixtures, as needed.
The part fixture has sensors to indicate that the part is loaded properly. A stack light annunciates proper part loading
with a green light and improper loading with a red light.
Table 4 - Proposed Architecture for Load Station #1
Components
Standard Inputs
Safety Inputs
Safety Outputs
Comments
Floor mat
2
E-stop device
2
Robot safety enable 2
2
Robot safety contactors
1 or 2
2
for contactor feedback
Total:
7
2