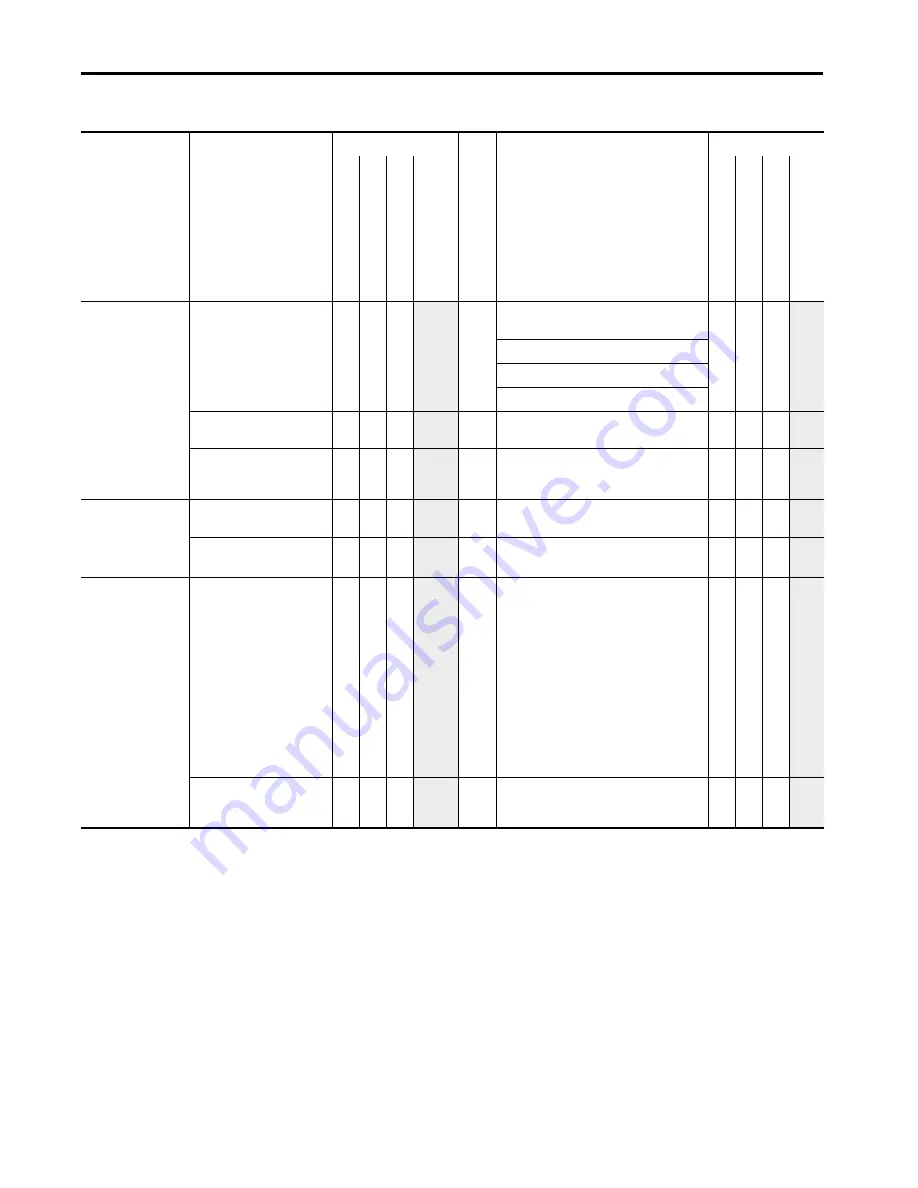
20
Rockwell Automation Publication IASIMP-QS005H-EN-P - April 2016
Chapter 1
Risk Assessment and System Design
Table 2 - Risk Assessment Worksheet - Load Part at Load Station #1
Steps
Potential Incidents or
Accidents
Prior to Safeguards
Curr
ent S
af
eguards
Recommendations
With Safeguards
Se
ve
ri
ty o
f Inj
u
ry
Fr
equ
enc
y (
Exp
osu
re
)
Avo
id
an
ce
Ri
sk
R
educ
tio
n
Ca
te
go
ry
(1)
Se
ve
ri
ty o
f Inj
u
ry
Fr
equ
enc
y (
Exp
osu
re
)
Avo
id
an
ce
R
es
idual Ri
sk<F
1)
1. Remove part from
the transfer rack.
Ergonomic exposure due to part
pick location.
S2
F2
A2
R1
Evaluate cart design for pick elevation and
modify, if necessary.
S1
F2
A1
R3A
Train workers on proper lifting technique.
Job rotation.
Awareness posters on proper lifting technique.
Cuts to hands or arms due to
sharp edges on parts.
S2
F2
A2
R1
PPE: Hand and arm protection such as protective
gloves and sleeves.
S1
F1
A1
R4
Crushing or cuts due to cart tip-
over hazard.
S2
F1
A2
R2B
Evaluate cart design for stability and correct if
required. Verify that the cart does not move
while unloaded.
S1
F1
A1
R4
2. Move part to
loading station on
stacklight
indication:
OK to load.
Slips or tripping due to debris
on the floor.
S2
F2
A1
R2A
Enforce housekeeping procedures for floor
cleaning.
S2
F1
A1
R3B
Slips or tripping due to raised
edges or floor discontinuity.
S2
F2
A1
R2A
Verify that the floor area does not have any
discontinuities higher than 3/16 in.
S2
F1
A1
R3B
3. Place part into
loading fixture. Part
loading is complete
upon stacklight
indication: Part
position OK.
Mechanical impact: Pinch or
Crush hazard due to robot
motion.
S2
F2
A2
R1
Inhibit robot motion while person is in the
hazardous area.
a. Use hard guards to reduce hazardous area.
b. Use floor mat, light curtain, area scanner,
or automatic gate to sense when a person
is in the hazardous area or prevent
exposure to the hazardous area.
c. Implement robot zone control with
annunciation to allow for part loading
when robot does not present a hazard.
Use base safety limit switches to define
the zone.
d. Install a properly-rated safety control
system.
S1
F1
A1
R4
Eye injury due to compressed
air or airborne debris from the
environment.
S2
F1
A2
R2B
PPE: Safety glasses to protect eyes.
S1
F1
A1
R4
(1) Risk Ratings of R1, R2A, R2B, R3, R4 correspond to the Safety Control Circuit Performance requirements of ANSI/RIA R15.06-1999. An R1 rating represents a control reliable circuit with continuous
checking for electrical and fluid power circuits. See the standard for a complete definition of performance requirements for the related risk ratings.