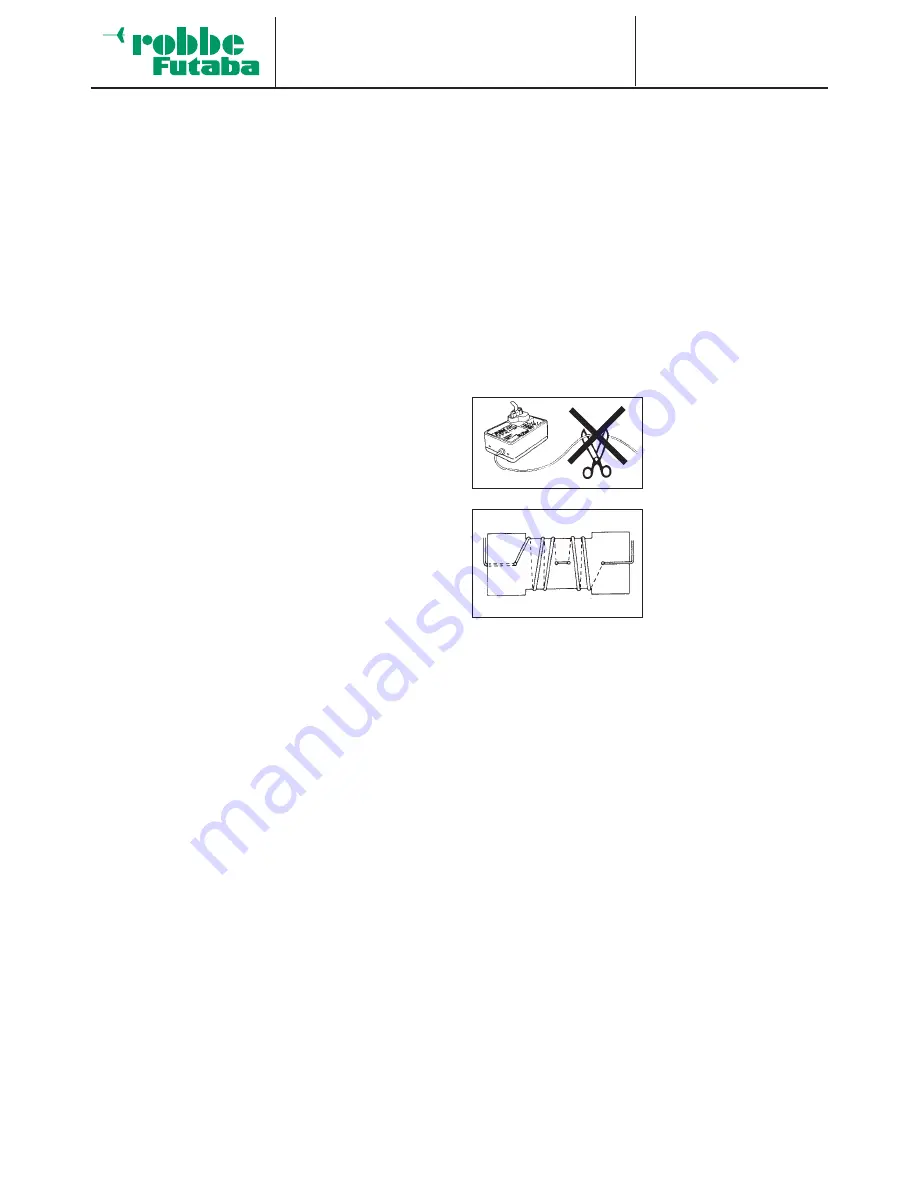
Tips and notes
F X - 4 0
20.
TIPS ON INSTALLING THE RECEIVING SYSTEM
20.1 INSTALLING AND USING RECEIVERS
In the last few years the technical equipment carried in our
models has undergone enormous changes. These include
brushless motors and controllers, Lithium flight batteries, tele-
metry systems, GPS systems etc. etc., to mention just a few
broad categories.
At the same the materials used in our models have altered,
with the widespread introduction of carbon fibre into the
modelling world. More and more carbon parts, Lithium batte-
ries and brushless motors are now employed, with the aim of
producing strong, lightweight, high-performance models. In
model helicopters the toothed-belt drive system for the tail
rotor has virtually become standard.
At the design stage the installation of the servos, motor and
flight battery is generally laid down, but the receiver is often
left to last, and has to be squeezed into whatever space
remains. At the same time we all assume that the RC system
will provide completely reliable control of the final model /
power system configuration.
However, this is not a safe assumption on its own, as there are
vast numbers of possible combinations of metal, plastic and
carbon components, and many of them - especially in con-
junction with toothed-belt drive systems - can have a more or
less pronounced adverse effect on quality of reception. Com-
bining the various electrically conductive and non-conductive
materials can cause potential spark points where static char-
ges build up at the junction between different materials, and
these can have a massive effect on reception.
Although the receiver position is very important to reception
quality, it is not the only problem area: another crucial aspect
is the deployment of the aerial. Neither is it true that all recei-
vers are the same: small, slim, lightweight types are required
for some applications, whereas top priority for other types of
model is a large number of channels. The result is that the
range of receivers available commercially is extremely broad,
and every receiver type features its individual characteristics in
respect of sensitivity to the transmitter signal and rejection of
potential interference (electro-smog).
Reception quality is also affected by the number of servos in
the model, and the length and position of their cables. In some
aircraft large parts of the fuselage or fuselage reinforcements
are manufactured from conductive materials (carbon fibre, alu-
minium foil, metal), and these substances shield the transmit-
ter signal, resulting in a significant loss of reception quality.
The same applies to fuselages which are finished in heavily
pigmented or metallic paints.
Pushrods, carbon rovings and servo leads running parallel to
the receiver aerial affect the electrical field around the aerial,
and also tend to absorb the transmitter energy. This has the
overall effect of markedly reducing the energy of the transmit-
ter signal which the receiver aerial is able to exploit.
Even the weather has its part to play: in fine, dry weather con-
ditions air humidity is reduced, and this tends to produce more
electro-static charge in the model than in damp conditions. On
humid days, on the other hand, the ground reflects a greater
proportion of the transmitted energy. This can have the effect
of generating “reception dead-spots” - varying according to
the aerial angle and the distance to the model - because the
transmitted signals broadcast via the air and reflected from the
ground tend to cancel each other out or amplify each other
(timing differences of the two waves). Indoor flying - in sports
halls, for example - often takes place in buildings of steel or
steel-reinforced concrete construction, where multiple reflec-
tions (roof - floor - walls) can very often generate “reception
dead-spots”.
It is impossible for radio manufacturers to test out all these
combinations of models, materials, aerial angles, aerial posi-
tions etc., especially since the errors are cumulative: several
minor “imperfections” can add up, generating serious interfe-
rence. Only the individual modeller or model flyer can test and
eradicate these conditions for himself.
The following list contains a few elementary notes on
methods of obtaining optimum reception characteristics:
20.2 RECEIVER AERIAL:
The receiver aerial is connec-
ted permanently to the recei-
ver. Never shorten or extend
the aerial. If possible deploy it
in an L-shape.
If this is not possible, we
recommend that you deploy
the aerial in an S-shape by
winding the wire onto a small
plate made of card, plywood
or plastic, as shown in the
sketch here, and locate it as
close to the receiver as possi-
ble. This does not reduce the receiver’s effective range.
Avoid aerial damage by fitting a tension relief and guide, e.g. a
short piece of fuel tubing, where the wire exits the fuselage. It
is essential to ensure that the aerial cannot foul the propeller.
It is also of fundamental importance to heed the following
points relating to receiver aerial positioning:
• If possible deploy the aerial in an L-shape to avoid attitude-
dependent problems.
• Do not deploy the aerial parallel to electrically conductive
materials, such as cables, metal “snakes”, control cables,
carbon pushrods etc., or along the inside or outside of elec-
trically conductive fuselages.
• Cables connected to the receiver (servos, batteries etc.)
should not be of the same length as the aerial, nor half its
length, nor whole-number multiples of it. For example:
receiver aerial length 1 m; avoid the following cable lengths:
0.5 m, 1 m, 2 m, 3 m etc.
• Keep the aerial as far away as possible from:
• High-current speed controller cables and motor cables;
• Sparkplugs and glowplugs, ignition units and onboard
glowplug energisers;
• Locations where static charges are likely to build up, such
as toothed belts, turbines etc.;
• If the fuselage is made of a material with shielding qualities,
run the aerial directly out of the fuselage;
• Do not attach the end of the aerial to an electrically conduc-
tive material (metal, carbon fibre);
• Whip aerials must never be attached to electrically conduc-
tive materials (carbon, aluminium etc.). High-speed models
are particularly susceptible to the build-up of static charges
due to high airspeeds. On such models the whip aerial must
not be attached to the surface of the fuselage.
98