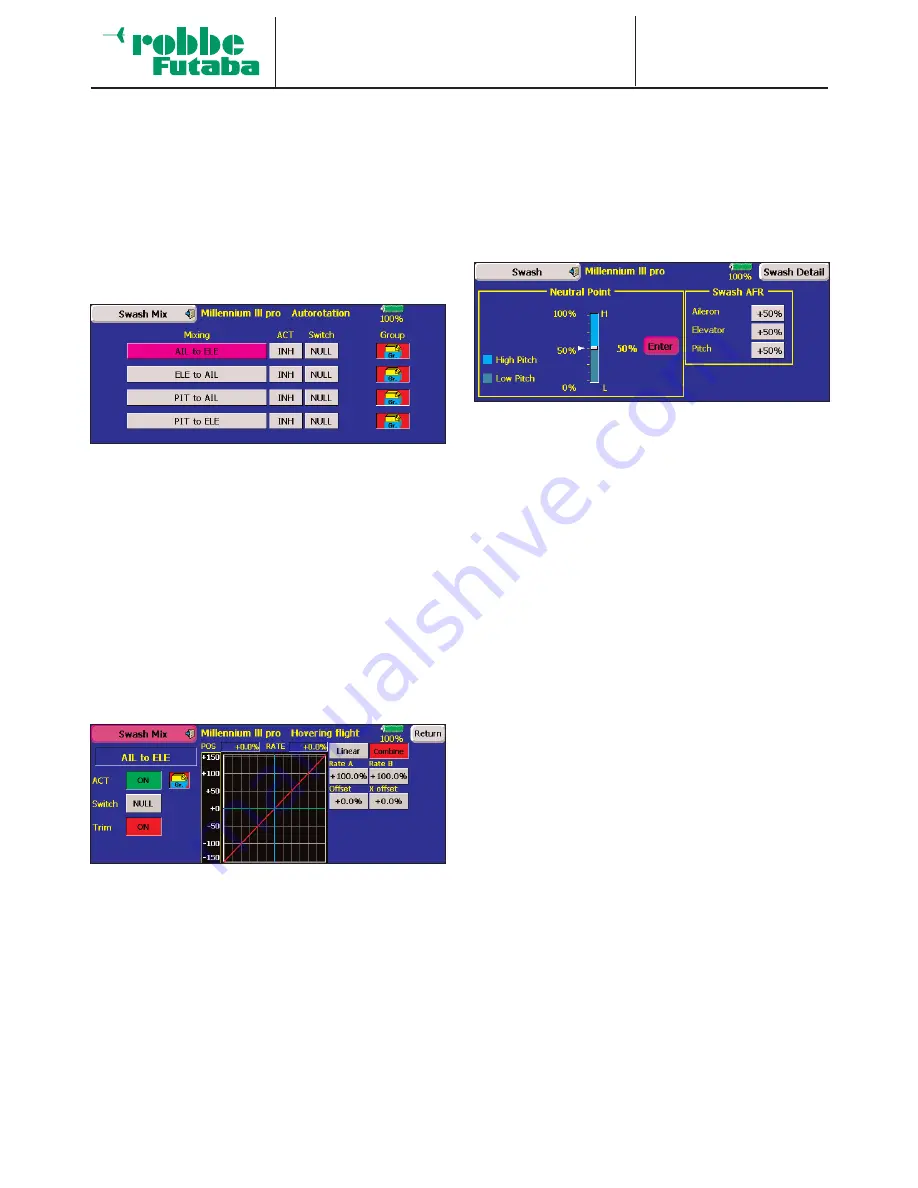
Model menu
Swashplate mixer
F X - 4 0
19.5 SWASHPLATE MIXER
(virtual swashplate rotation)
This function is used to set up the swashplate accurately over
its full travel. All the basic functions (roll-axis (aileron), pitch-
axis (elevator) and collective pitch) can be superimposed on
each other. Four mixers are required for this, and for each one
a mixer curve can be activated and a trigger switch defined.
With the ‘Helicopter’ model type already selected, mark the
‘Swash Mix.’ option in the Model menu. The screen now looks
like this:
First each mixer has to be activated by marking the correspon-
ding ‘Status’ field; the same field then displays ‘On’ or ‘Off’
according to the position of the switch. The effects and
method of setting the ‘Glob’ or ‘Sepa’ mode have already
been described; select your preference in the ‘Mode’ column.
Move to the ‘Switch’ column and select a switch and its direc-
tion of operation in the usual way.
The mixer function is actually set up with the help of the asso-
ciated curve in the sub-menu: mark the appropriate line in the
‘Mix’ column, and the curve display appears. The curve can
then be programmed using the familiar procedure: the first
step is to select the curve type, after which you can program
the values required. The method of programming a mixer
curve is exactly as described in Section 17.2 on page 57; ple-
ase refer back to that section if you are not sure.
The display for setting up a ‘Roll -> pitch-axis’ curve is shown
in the screen shot above. The left area shows the selected
‘Glob’ or ‘Sepa’ mode, together with the assigned trigger
switch and its current status, according to the switch’s physi-
cal position.
Virtual swashplate rotation
Virtual swashplate rotation of 45° is required, and for this we
need to activate the first two mixers ‘Roll -> pitch-axis’ and
‘Pitch-axis ? roll’ with trim ‘On’, in each case with a mixer rate
of 100%. The default in this field is ‘Off’. Mark the button field
to reverse the setting.
If you find there are minor discrepancies in the swashplate lin-
kage, preventing the helicopter from flying in a straight line, it
is possible to correct this by setting up slightly different set-
tings in the individual mixer functions.
SET-UP EXAMPLE: SWASHPLATE MIXER
Programming the swashplate mixer can be a complex proce-
dure, so the next section describes a complete example in
order to clarify the process. At the same time the associated
mechanical procedures are explained.
For a model helicopter with an electronic three-point swash-
plate linkage (e.g. H-3 120°), the first step is to mark the
‘Swashplate’ option in the base menu.
In the Swashplate (AFR) field you will find all the values for roll,
pitch-axis and collective pitch are set to +50% by default.
These are standard values which suit most model helicopters.
Once you have installed the servos in the helicopter and instal-
led the mechanical linkages, the next process is to set them up
accurately relative to each other. At this point a very useful aid
is the ‘Servo monitor’ option, which you can access from the
Base menu.
The top right corner of the screen shows the ‘Servo test’ func-
tion. Mark this field, and the display changes to show the Neu-
tral test. Mark the field to the left of this, which now changes to
‘Test on’. All servos move to their neutral position and stay at
that setting. Another option is to centre the collective pitch
stick with the help of the collective pitch display on the trans-
mitter’s home screen, where the value is displayed with an
accuracy of 0.1%.
Mount the servo output arms and discs on the servos as sta-
ted in the building instructions provided by the model helicop-
ter manufacturer. Take care to position the servo output arms
at right-angles to the servo case. Connect the pushrods in
such a way that the rods are at right-angles to the servo output
arms relative to the helicopter chassis. Adjust the pushrods
from the servo output arms to the swashplate until the swash-
plate is at the correct height, and is at right-angles to the main
rotor shaft when viewed from all sides. Now operate the col-
lective pitch and cyclic pitch controls at the transmitter, and
check that the swashplate moves in the correct directions. If
the direction of collective movement is incorrect, alter the cor-
responding value in the ‘Swashplate (AFR)’ field to -50%; this
reverses the direction of movement of the swashplate.
The next step is to check the roll (aileron) and pitch-axis (ele-
vator) functions; if necessary, change the values for AFR to
negative. Now operate the collective pitch stick: if one or more
servos rotate in the wrong direction, call up the ‘Servo reverse’
menu and change the direction of rotation of the relevant servo
or servos, then repeat the ‘direction’ test in the ‘Swashplate
AFR’ menu. Now move the collective pitch stick to each end-
point in turn, working slowly and carefully in order to avoid the
servos striking their end-stops. If the servo travels are exces-
sive, reduce the set AFR value in this menu until the swash-
plate runs to a point just short of the maximum travel dictated
by the mechanical system. With the rotor blades fitted, you
can read off the collective pitch angle using a collective pitch
gauge.
90