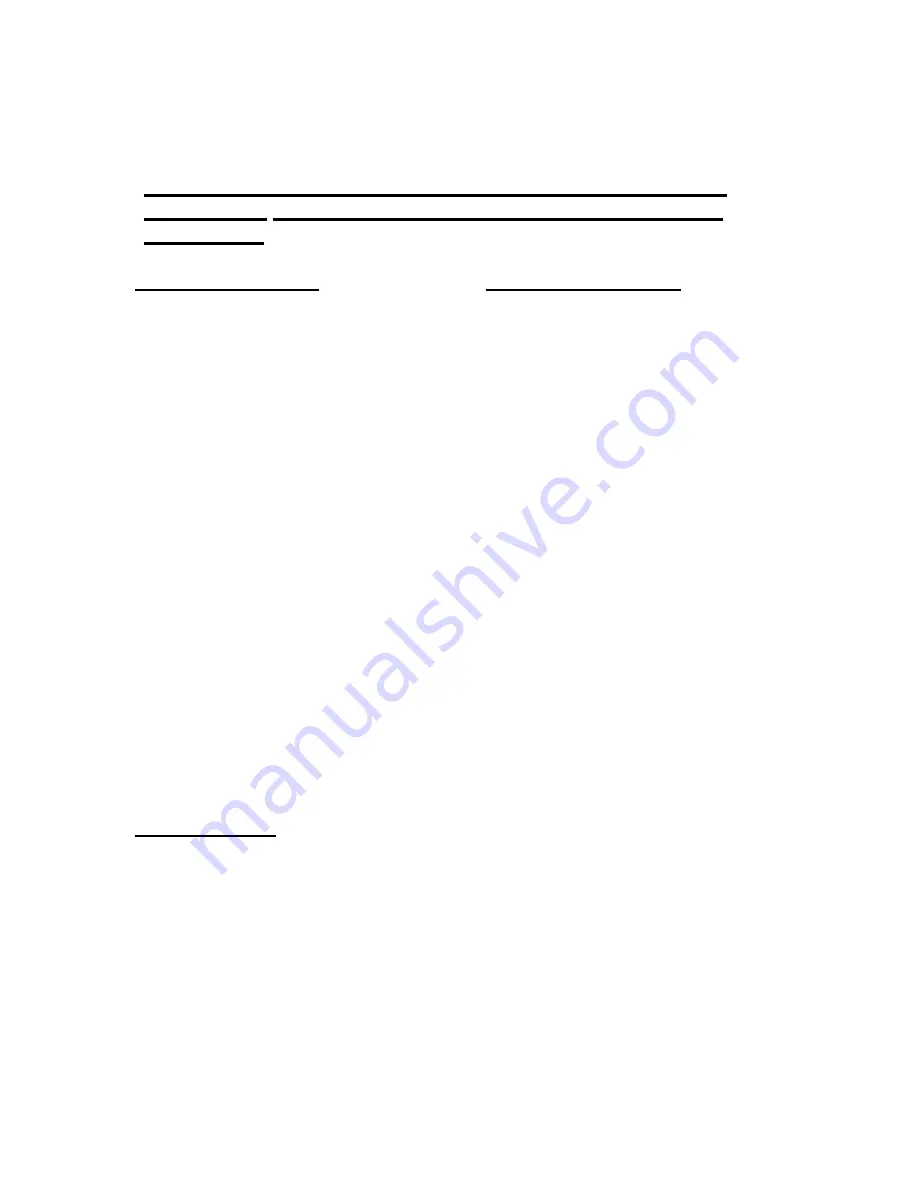
09/01/2013
RANS S-20 RAVEN
TEXT MANUAL
00-27
NUMBERING AND PLACARDS
WHAT ARE THE SPECIAL REQUIREMENTS AS FAR AS
ATTACHING NUMBERS AND PLACARDS TO HOMEBUILT
AIRCRAFT?
DISPLAY OF MARKS
(Reference is FAR Part 45.23)
After you obtain the registration
of your aircraft, the Registration
numbers or marks must be affixed
to the aircraft in some permanent
fashion. The marks must be
legible and have no
ornamentation. They must
contrast in color with the
background.
The marks displayed on the
aircraft shall include the letter “N”
signifying U.S. Registry, followed
by the registration number issued
for the aircraft.
In addition, amateur-built
(Experimental) aircraft must have
displayed on that aircraft near
each entrance to the cabin or
cockpit, in letters not less than 2"
not more than 6" in height, the
word, EXPERIMENTAL”.
LOCATION OF MARKS ON FIXED
WING AIRCRAFT (Reference is
FAR Part 45.25)
(b) (1) If displayed on the vertical tail
surfaces, horizontally on both
surfaces, horizontally on both
surfaces of a single vertical tail or on
the outer surfaces of a multi-vertical
tail. However, an aircraft on which
marks at least 3" high may be
displayed and in accordance with
45.29 (b)(1), the marks may be
displayed vertically on the vertical
tail surface.
(2) If displayed on the fuselage
surfaces, horizontally on both sides
of the fuselage between the trailing
edge of the wing and the leading
edge of the horizontal stabilizer.
However, if engine pods or other
appurtenances are located in this
area and are an integral part of the
fuselage side surfaces, the operator
may place the marks on those pods
or appurtenances.
SIZE OF MARKS
FAR 45.29 (b) (1) (iii) states “Marks at least 3" high may be displayed on an
aircraft for which an experimental certificate has been issued under 21.191 (d) or
21.191 (g) for operating as an exhibition aircraft or as an amateur-built aircraft
when the maximum cruising speed of the aircraft does not exceed 180 knots
Calibrated Air Speed (CAS). And (c) characters must be two-thirds as wide as
they are high except “1" which must be one-sixth as wide as it is high and the
letters “M” and “W” which may be as wide as they are high. And (d), Characters
must be formed by solid lines one-sixth as thick as the character is high. (e)
Spacing. The space between each character may not be less than one-fourth of
the character width.