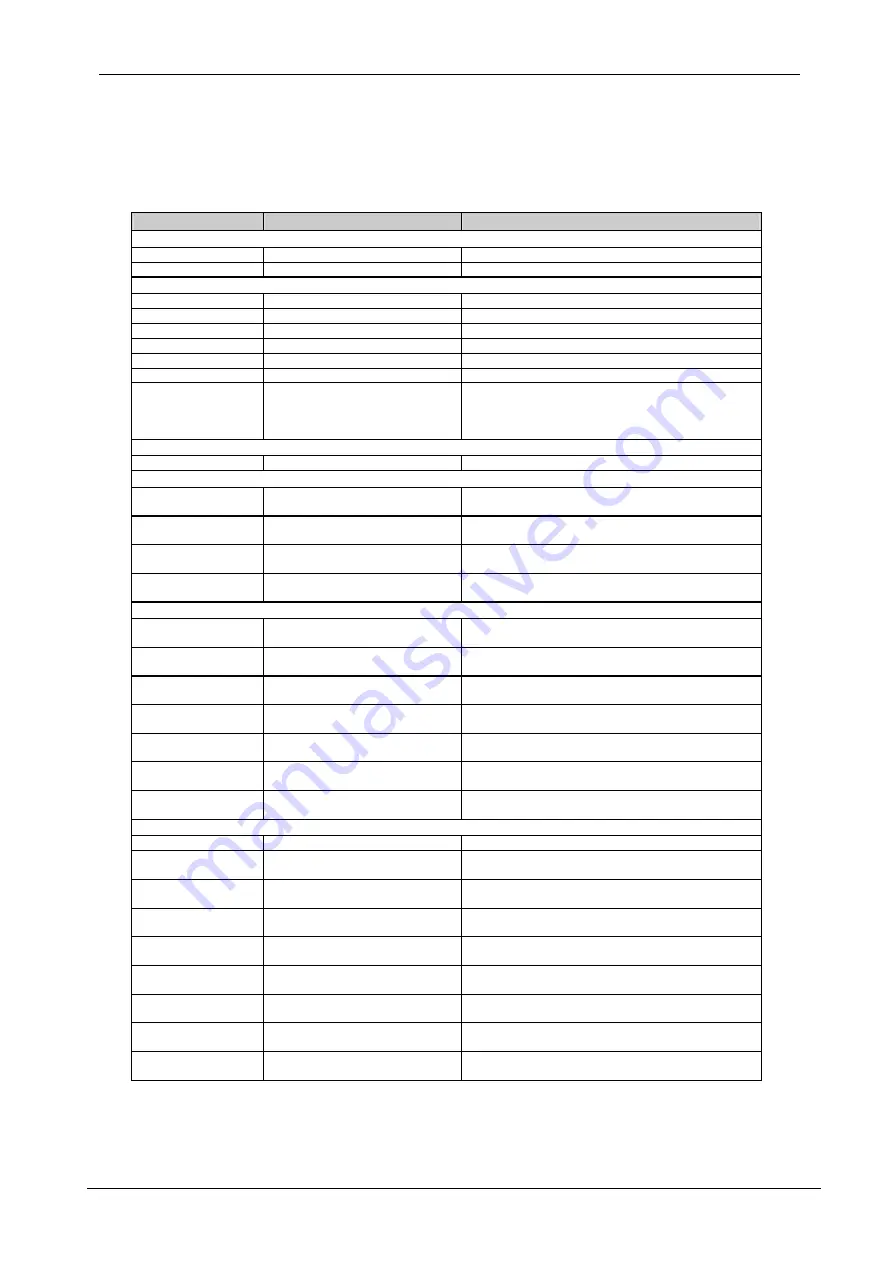
SDRIVE 700
POWER ELECTRONICS
112
COMMONLY USED CONFIGURATIONS
12.6.
Pressure Group Control with Eight Pressure References
12.6.1.
Parameters Configuration
Parameter
Name / Description
Value
G1: Options Menu.
4 LANG=ENGLISH
G1.4
/ Language selection
ENGLISH
7 PROG = STANDAR
G1.7
/ Program activation
STANDAR
G2: Motor Nameplate.
1 MTR CURR=00.00A
G2.1
/ Motor rated current
__A (Set according to motor nameplate).
2 MTR VOLT=400V
G2.2
/ Motor rated voltage
__V (Set according to motor nameplate).
3 MTR PWR=00.0kW
G2.3
/ Motor rated power
__kW (Set according to motor nameplate).
4 MTR RPM=1485
G2.4
/ Motor rpm
__rpm (Set according to motor nameplate).
5 MTR PFA=0.85
G2.5
/ Cosine Phi
__ (Set according to motor nameplate).
6 MTR FRQ=50Hz
G2.6
/ Motor frequency
__Hz (Set according to motor nameplate).
7 MTR COOL=40%
G2.7
/ Motor cooling at zero speed
Use the following values as a reference:
Submersible pumps
Î
20%
Self-cool motor
Î
40%
Force-cooled motor
Î
100%
G3: References.
1 REF1 SPD=PID
G3.1
/ Speed reference source 1
PID
Î
The reference value is set for PID functionality.
G4: Inputs – S4.1: Digital Inputs.
5 DIGITL IN 1=50
G4.1.5
/ Multi-function Digital Input 1
configuration
50
Î
PMP START/STP (Automatic starting of the system).
6 DIGITL IN 2=63
G4.1.6
/ Multi-function Digital Input 2
configuration
63
Î
SETPONT PIN1 (low bit configuration for the selection of
multiple setpoints).
7 DIGITL IN 3=64
G4.1.7
/ Multi-function Digital Input 3
configuration
64
Î
SETPONT PIN2 (middle bit configuration for the selection of
multiple setpoints).
8 DIGITL IN 4=65
G4.1.8
/ Multi-function Digital Input 4
configuration
65
Î
SETPONT PIN3 (high bit configuration for the selection of
multiple setpoints).
G4: Inputs – S4.3: Analogue Input 2.
1 SENSOR 2 ?=S
G4.3.1
/ To enable sensor of Analogue
Input 2
Y=YES
Î
Ii allows enabling the sensor of the analogue input 2
that will be used for PID feedback.
2 SENSOR 2=Bar
G4.3.2
/ Selection of sensor 2 units
Bar
Î
These units must be set according to type of sensor that
user will use in the installation.
3 AIN2 FORMAT=mA
G4.3.3
/ Analogue Input 2 Format
mA
Î
These units must be set according to the type of sensor that
user will use in the installation.
4 4mA
G4.3.4
/ Minimum range of Analogue Input
2
+4mA
Î
These units must be set according to the type of sensor
that user will use in the installation.
5 Smi2=+0.0Bar
G4.3.5
/ Minimum range of sensor 2
+0.0Bar
Î
This range must be set according to the type of sensor
that user will use in the installation.
620mA
G4.3.6
/ Maximum range of Analogue Input
2
+20mA
Î
These units must be set according to the type of sensor
that user will use in the installation.
7 Sma2=+10.0Bar
G4.3.7
/ Maximum range of sensor 2
+10.0Bar
Î
This range must be set according to the type of
sensor that user will use in the installation.
G25: Pump Control – S25.1: Setpoints.
1 CONTROL MODE=1
G25.1.1
/ Control mode
1
Î
Pumps. The drive will start in pump control mode.
5 SETPT1=1.0Bar
G25.1.5
/ Local setpoint 1 for the PID
1.0Bar
Î
It allows user to set the value of the speed reference 1
for the equipment. (Set according to the requirements of the applic.)
6 SETPT2=2.0Bar
G25.1.6
/ Local setpoint 2 for the PID
2.0Bar
Î
It allows user to set the value of the speed reference 2
for the equipment. (Set according to the requirements of the applic.)
7 SETPT3=3.0Bar
G25.1.7
/ Local setpoint 3 for the PID
3.0Bar
Î
It allows user to set the value of the speed reference 3
for the equipment. (Set according to the requirements of the applic.)
8 SETPT4=4.0Bar
G25.1.8
/ Local setpoint 4 for the PID
4.0Bar
Î
It allows user to set the value of the speed reference 4
for the equipment. (Set according to the requirements of the applic.)
9 SETPT5=5.0Bar
G25.1.9
/ Local setpoint 5 for the PID
5.0Bar
Î
It allows user to set the value of the speed reference 5
for the equipment. (Set according to the requirements of the applic.)
10 SETPT6=6.0Bar
G25.1.10
/ Local setpoint 6 for the PID
6.0Bar
Î
It allows user to set the value of the speed reference 6
for the equipment. (Set according to the requirements of the applic.)
11 SETPT7=7.0Bar
G25.1.11
/ Local setpoint 7 for the PID
7.0Bar
Î
It allows user to set the value of the speed reference 7
for the equipment. (Set according to the requirements of the applic.)
12 SETPT8=8.0Bar
G25.1.12
/ Local setpoint 8 for the PID
8.0Bar
Î
It allows user to set the value of the speed reference 8
for the equipment. (Set according to the requirements of the applic.)