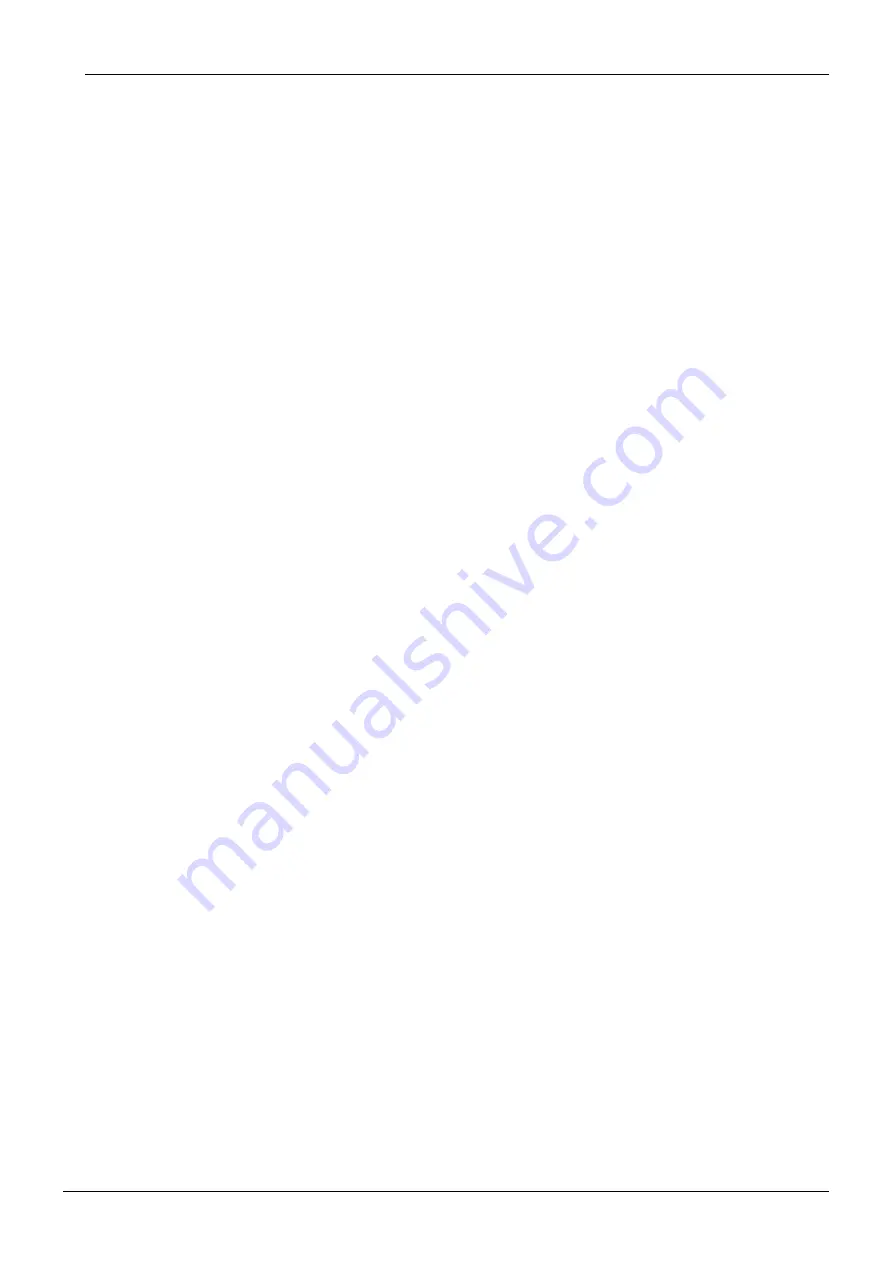
Chapter C - SERVICE MODE
Planmeca Compact i C-19
SERVICE MODE DETAILED DESCRIPTION
Technical Manual
n 5
Show scaler electronics ID-code (n id-code) and
connection point of the scaler electronics (--n-) or (---n)
The (optionally) installed scaler electronics module is identified by a jumper wire on its con-
nector that plugs to the MCB. It is important for the MCB to know the type of scaler electronics
installed. This service mode allows you to check what type of scaler electronics is installed
and that the identification works properly. It is also possible to check if the scaler electronics is
installed on the MCB or at the IMUX.
The location of the scaler electronics is indicated on the display by pressing the S-key with
delay. If the display (--n-) is shown then the electronics is connected to IMUX or (---n) then the
electronics is connected to MCB.
0
No scaler electronics module installed
1
AMDENT scaler module installed
2
EMS scaler module installed
3
SATELEC scaler module installed
6
Newtron scaler module installed
4-5, 7 reserved
n 6
Show service door switch signal (n door status)
This is the signal from the microswitch that indicates the door status (1 = door open, 0 = door
closed). An open circuit, broken wire or loose connector is interpreted as the door would be
continuously open. During this condition the chair cannot be run, except for in the service
mode when the control system temporarily ignores this signal.
n 7
Show mains frequency (nn.n Hz)
There is no other use for this service mode than checking the condition of a part of the MCB
electronics. If everything is OK the display should be stable within ±2 digits. Severe mains
voltage transients can up-set the display temporarily, and would also cause the OP-light to
flicker. If this display is stable but the OP-light flickers occasionally, it’s probably caused by a
bad bulb socket.
n 8
Show (optional) assistant syringe hose ID (n id-code)
If no hose is connected (or if the assistant syringe option is not installed) the display should
show a dash “-”. If any other instrument than a syringe is connected then the display should
show 0 (zero). If a valid syringe (hose) is connected then the display shows the syringe hose
ID-code (e.g. 20).
n 9
Show (optional) assistant syringe hose sense signal (nnn
signal)
Same as above but this is the direct signal from the assistant syringe hose identification cir-
cuitry. The display range is 0-255. 255 indicated an open circuit, 0 indicated a short, any other
values represent the signal. The display should be fully stable within one digit.
n 10
Show MCB heatsink temperature (nn °Celsius or
°Fahrenheit)
The temperature is measured inside the black aluminum block on the MCB. During normal
circumstances the temperature should stay below 55°C. The temperature can rise above this
level if the fixing screws (that attach the heatsink to the aluminum box) are missing. To protect
against overheating the CPU turns off those loads that contribute to the power dissipation
(OP-light and IPS) if the temperature rises above 60°C, The error E15 is then also displayed.
Summary of Contents for Compact I
Page 1: ...technical manual 10007462_23 EN...
Page 2: ......
Page 20: ...Chapter A GENERAL TECHNICAL DATA A 12 Planmeca Compact i EMC INFORMATION Technical Manual...
Page 212: ...Chapter H FOOT CONTROL H 18 Planmeca Compact i ADJUSTMENTS Technical Manual...
Page 213: ...Planmeca Compact i I 1 Chapter Technical Manual I DIAGRAMS...
Page 214: ...Chapter I DIAGRAMS I 2 Planmeca Compact i Technical Manual...
Page 216: ......
Page 218: ......
Page 220: ......
Page 222: ......
Page 224: ......
Page 226: ......
Page 228: ......
Page 230: ......
Page 232: ......
Page 234: ......
Page 236: ......
Page 238: ......
Page 240: ......
Page 242: ......
Page 243: ......