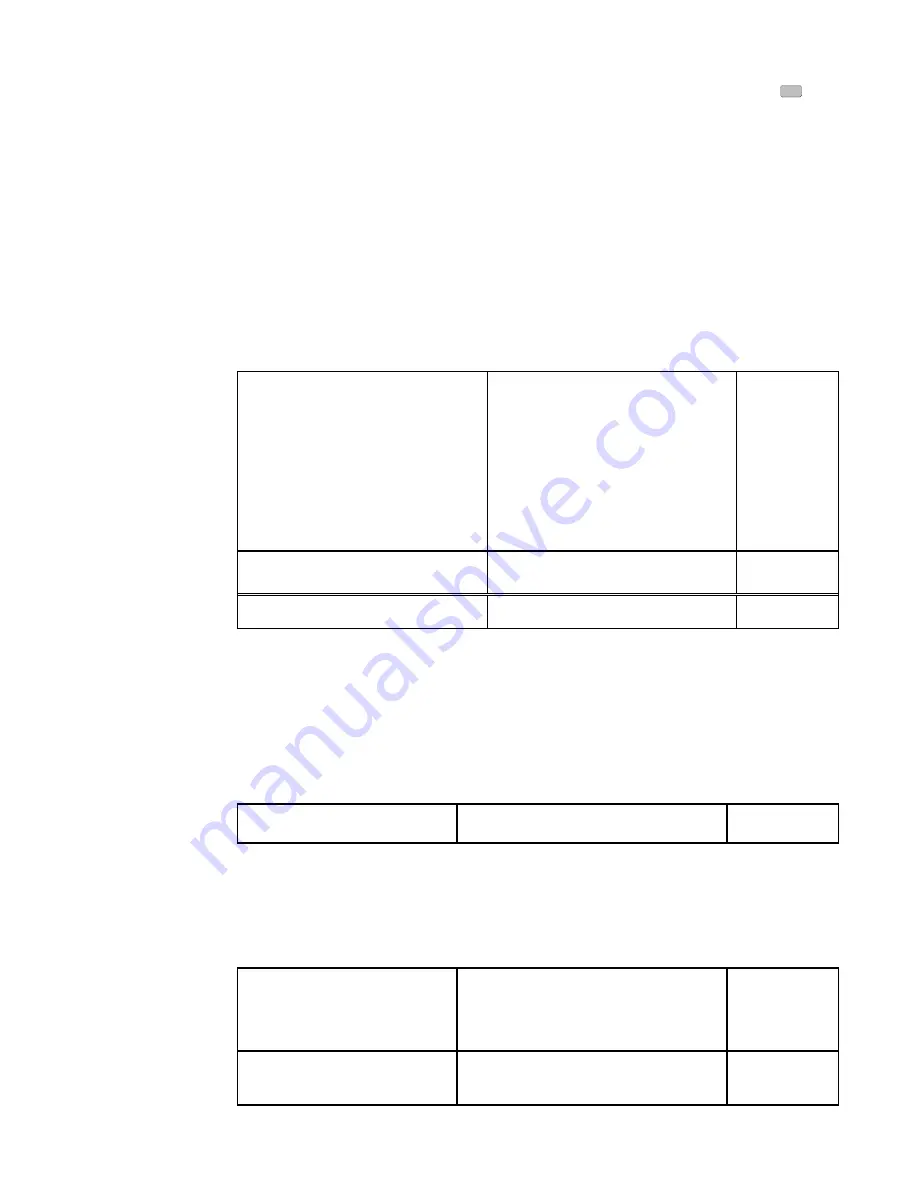
Function Parameters
9-7
AC10 Inverter
Should you intend to check any display item for four-line LCD press “M” key and press
<<
key
to check.
Refer to the following table for each specific value unit and its indication:
Whatever the value of F131 is set to, corresponding target frequency will flash under stopped
status.
Target rotary speed is an integral number. If it exceeds 9999, add a decimal point to it.
Current display A *.* Bus voltage display U*** Output voltage display *** Temperature
H***Linear speed L***. If it exceeds 999, add a decimal point to it. If it exceeds 9999, add
two decimal points to it, and the like.
PID given value o*.* PID feedback value b*.* Yarn length * centre frequency *.**
output power *.* output torque *.*
Note: when count value is displayed and it exceeds 99999, only 5 digits are displayed and
add a decimal point to it i.e., 123456 is displayed in the form of 12456..
F132 Display items of stop
Setting range:
0: Frequency/function-code
2: Target rotary speed
4: PN voltage
8: PID feedback value
16: Temperature
32: Count values
64: PID given value
128: Yarn length
256: Centre frequency
512: Setting torque
Mfr’s value:
0+2+4
=
6
F133 Drive ratio of driven system
Setting range: 0.10
~
200.0
Mfr’s value:
1.00
F134 Transmission-wheel radius
0.001
~
1.000 (m)
Mfr’s value:
0.001
Calculation of rotary speed and linear speed:
For example, If inverter’s max frequency F111=50.00Hz, numbers of motor poles F804=4, drive
ratio F133
=
1.00, transmission-shaft radius R=0.05m, then
Transmission shaft perimeter: 2πR =2×3.14×0.05=0.314 (meter)
Transmission shaft rotary speed: 60× operation frequency/ (numbers of poles pairs × drive ratio)
=60×50/ (2×1.00) =1500rpm
Endmost linear speed: rotary speed × perimeter=1500×0.314=471(meters/second)
F136 Slip compensation
Setting range: 0
~
10
Mfr’s value: 0
Under V/F controlling, rotary speed of motor rotor will decrease as load increases. Be assured
that rotor rotate speed is near to synchronization rotary speed while motor with rated load, slip
compensation should be adopted according to the setting value of frequency compensation.
Note: During the process of Flycatching, slip compensation function is invalid. After
Flycatching is finished, this function is valid.
· F137 Modes of torque
compensation
Setting range:
0: Linear compensation;
1: Square compensation;
2: User-defined multipoint compensation
3: Auto torque compensation
Mfr’s value: 3
F138 Linear compensation
Setting range: 1
~
20
Mfr’s value:
subject to
inverter model
TC-Hydraulik - R
ü
sdorfer Str. 8 - 25746 Heide - Lars Lornsen - T: +49 481 909 - 34 - [email protected] - www.tc-hydraulik.de