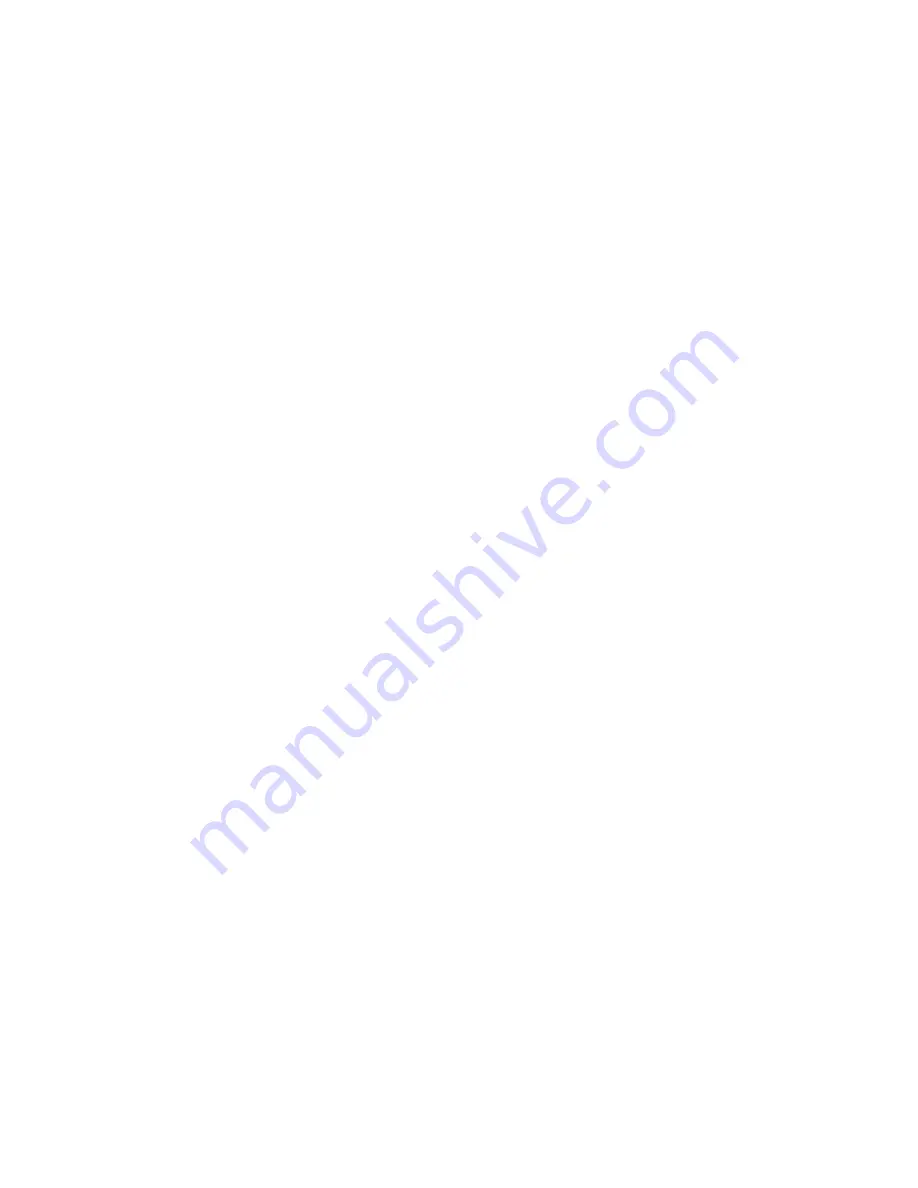
8-3
Operation and Simple Running
AC10 Inverter
8.2.5
Switching of the parameters displayed under stopped status
Under stopped status, inverter has five parameters of stopped status, which can be switched
over repeatedly and displayed with the key “M”. These parameters are displaying: keypad
jogging, target rotary speed, PN voltage, PID feedback value, and temperature. Please refer to
the description of function code F132.
8.2.6
Switching of the parameters displayed under running status
Under running status, eight parameters of running status can be switched over repeatedly and
displayed with the keys “M”. These parameters are displayed: output rotary speed, output
current, output voltage, PN voltage, PID feedback value, temperature, count value and linear
speed. Please refer to the description of function code F131.
8.2.7
Operation process of measuring motor parameters
The user shall input the parameters accurately as indicated on the nameplate of the motor prior
to selecting operation mode of vector control and auto torque compensation (F137=3) of V/F
control mode. Inverter will match standard motor stator resistance parameters according to the
parameters indicated on the nameplate. To achieve better control performance, the user may
start the inverter to measure the motor stator resistance parameters, so as to obtain accurate
parameters of the motor controlled.
The motor parameters can be tuned through function code F800.
For example: If the parameters indicated on the nameplate of the motor controlled are as
follows: numbers of motor poles are 4; rated power is 7.5kW; rated voltage is 400V; rated
current is 15.4A; rated frequency is 50.00HZ; and rated rotary speed is 1440rpm, operation
process of measuring the parameters shall be done as described in the following:
In accordance with the above motor parameters, set the values of F801 to F805 correctly: set
the value of F801 = 7.5, F802 = 400, F803 = 15.4, F804 = 4 and F805 = 1440 respectively.
1. In order to ensure dynamic control performance of the inverter, set F800=1, i.e. select
rotating tuning. Make sure that the motor is disconnected from the load. Press the “I” key on the
keypad, and the inverter will display “TEST”, and it will tune the motor’s parameters of two
stages. After that, the motor will accelerate according to the acceleration time set at F114 and
maintain for a certain period. The speed of motor will then decelerate to 0 according to the time
set at F115. After auto-checking is completed, relevant parameters of the motor will be stored in
function codes F806~F809, and F800 will turn to 0 automatically.
2. If it is impossible to disconnect the motor from the load, select F800
=
2, i.e. stationary tuning.
Press the “I” key, the inverter will display “TEST”, and it will tune the motor’s parameters of two
stages. The motor’s stator resistance, rotor resistance and leakage inductance will be stored in
F806-F808 automatically, and F800 will turn to 0 automatically. The user may also calculate and
input the motor’s mutual inductance value manually according to actual conditions of the motor.
TC-Hydraulik - R
ü
sdorfer Str. 8 - 25746 Heide - Lars Lornsen - T: +49 481 909 - 34 - [email protected] - www.tc-hydraulik.de