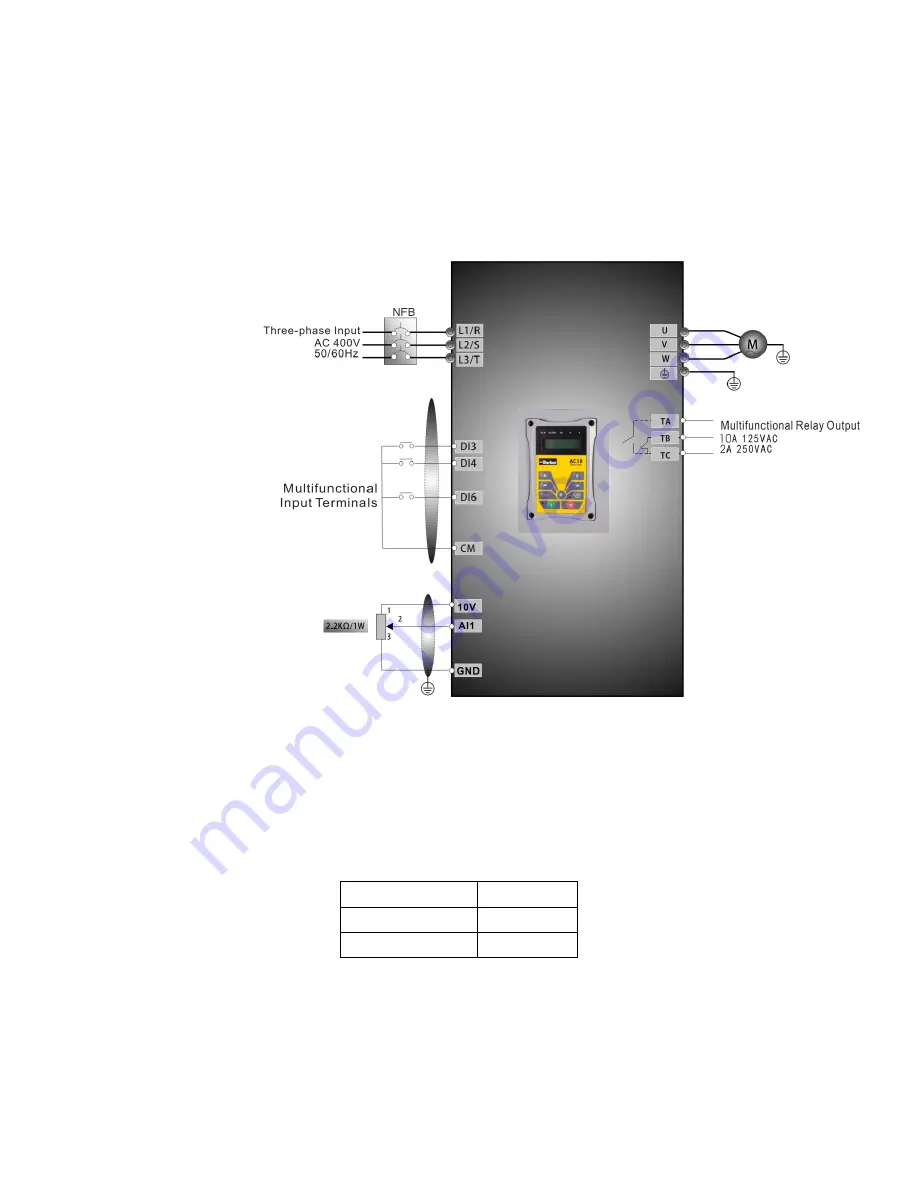
Operation and Simple Running
8-8
AC10 Inverter
8.3.4
Setting the frequency with analog terminal and controlling the
operation with control terminals
i.
Connect the wires in accordance with
Figure 8-3
. After having checked the wiring
successfully, switch on the mains supply, and power on the inverter. Note: 2K
~
5K
potentiometer may be used for setting external analog signals. For the cases with
higher requirements for precision, a precise multiturn potentiometer is
recommended, and adopt shielded wire for the wire connection, with near end of
the shielding layer grounded reliably.
Figure 8-3
Wiring Diagram 3
ii.
Press the “M” key, to enter the programming menu.
iii.
Study the parameters of the motor: the operation process is the same as that of
example 1. (Refer to 8.3.1 for tuning of the motor).
iv.
Set functional parameters of the inverter:
Function code
Values
F203
1
F208
1
v.
(5) There is a red two-digit coding switch SW1 near the control terminal block, as
shown in Figure 4-4. The function of coding switch is to select the voltage signal
(0
~
5V/0
~
10V) or current signal of analog input terminal AI2, current channel is
default. In actual application, select the analog input channel through F203. Turn
switches 1 to ON and 2 to ON as illustrated in the figure, and select 0
~
20mA
current speed control. Other switches state and mode of control speed are shown
in table
Table 8-2
.
TC-Hydraulik - R
ü
sdorfer Str. 8 - 25746 Heide - Lars Lornsen - T: +49 481 909 - 34 - [email protected] - www.tc-hydraulik.de