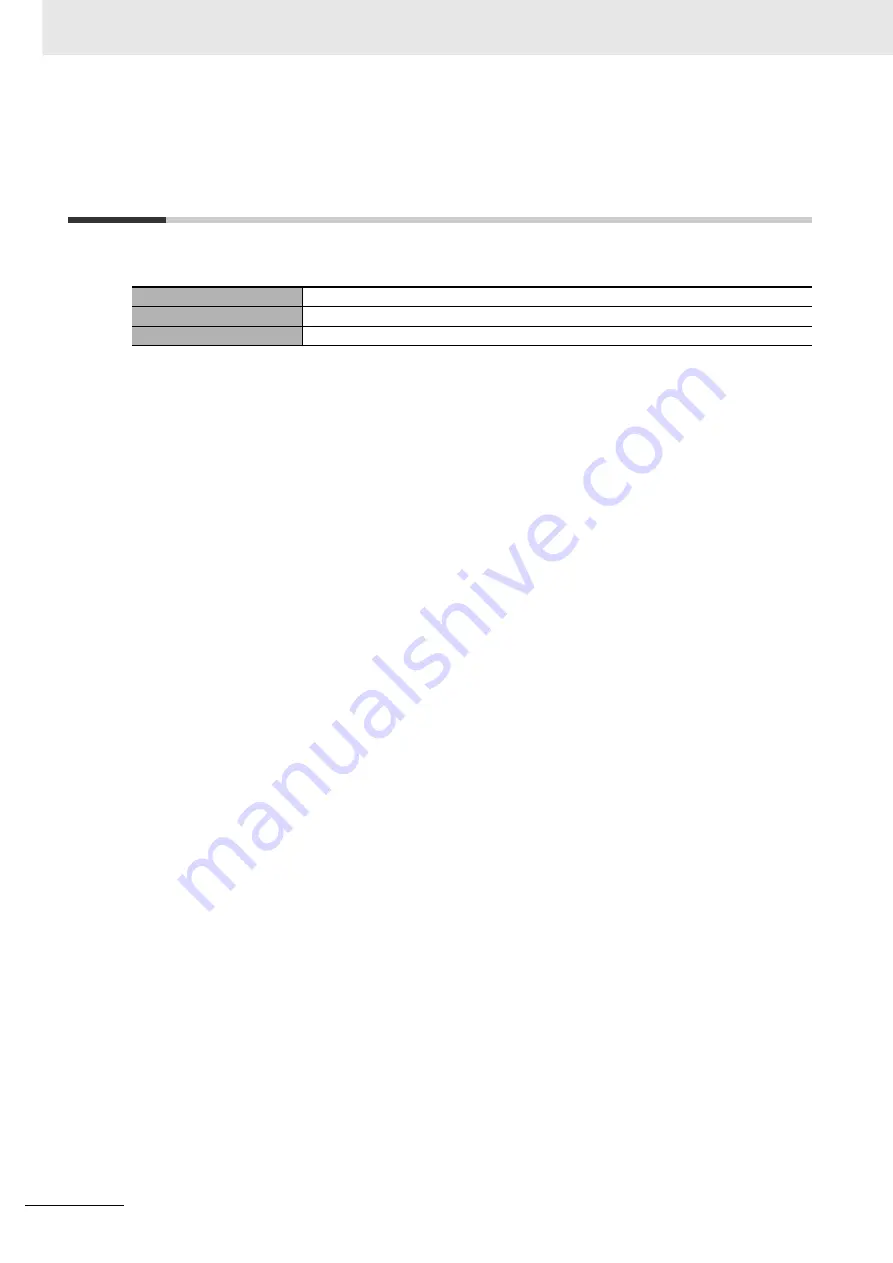
3 M Code
3 - 12
NJ/NY-series G code Instructions Reference Manual (O031)
Spindle Axis Rotation Function
(S function)
This instruction specifies a rotational speed of the spindle axis.
Specifies the rotational speed of the spindle axis with a number (0 or positive number) next to S code.
The unit of rotational speed is r/min (revolutions per minute).
The spindle axis is not operated simply by specifying the rotational speed.
To run the spindle axis, use the Auxiliary Function Output (M03/M04).
When the spindle axis is rotated by auxiliary function output (M03/M04) and if the S-code value is
changed, it is reflected on the spindle axis speed immediately.
Modal/Non-modal
Modal
Instruction format
S{data}
Relevant M codes
M03, M04
Summary of Contents for NJ501-5300
Page 13: ...11 CONTENTS NJ NY series G code Instructions Reference Manual O031...
Page 28: ...Revision History 26 NJ NY series G code Instructions Reference Manual O031...
Page 40: ...2 G Code 2 2 NJ NY series G code Instructions Reference Manual O031...
Page 72: ...2 G Code 2 34 NJ NY series G code Instructions Reference Manual O031...
Page 108: ...3 M Code 3 2 NJ NY series G code Instructions Reference Manual O031...
Page 112: ...3 M Code 3 6 NJ NY series G code Instructions Reference Manual O031...
Page 124: ...3 M Code 3 18 NJ NY series G code Instructions Reference Manual O031...
Page 128: ...3 M Code 3 22 NJ NY series G code Instructions Reference Manual O031...
Page 136: ...4 PROGRAM CODES 4 8 NJ NY series G code Instructions Reference Manual O031...
Page 141: ......