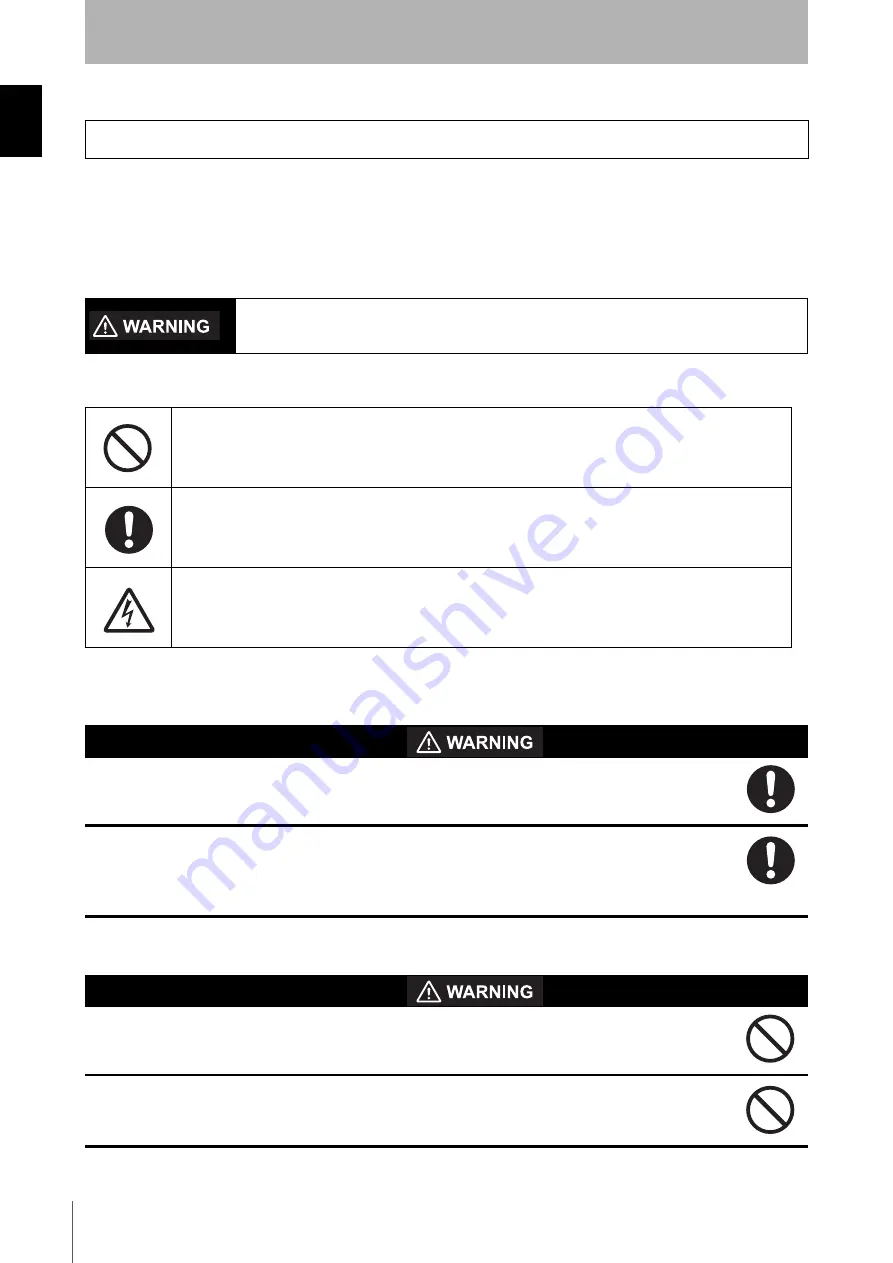
iv
Int
ro
ductio
n
F3SJ-A
User’s Manual
Precautions on Safety
Regarding the alert symbols and meanings used for the safe uses
In order to use the F3SJ safely, the precautions listed in this manual indicated by alert symbols and
descriptions must be followed. Failure to follow all precautions and alerts may result in an unsafe use or
operation.
The following indictions and symbols are used for the descriptions.
Meanimgs of Alert Symbols
Alert Statements in this Manual
For users
The F3SJ must be installed, configured, and incorporated into a machine control system by a
sufficiently trained and qualified person. An unqualified person may not be able to perform these
operations properly, which may cause a person to go undetected, resulting in serious injury.
When changes are made to each function using the setting tool (F39-GWUM or F39-MC21), the
administrator must manage the details of the changes and perform the changes. Accidental
functional setting change may cause failure of human body detection, resulting in a serious
injury.
For machines
Do not use this sensor for machines that cannot be stopped by electrical control. For example,
do not use it for a pressing machine that uses full-rotation clutch. Otherwise, the machine may
not stop before a person reaches the hazardous part, resulting in serious injury.
Do not use the auxiliary output or external indicator output for safety applications. Human body
may not be detected when F3SJ fails, resulting in serious injury.
Precautions on Safety
Indicates a potentially hazardous situation which, if not avoided, will result in minor or moderate injury, or
may result in serious injury or death. Additionally there may be significant property damage.
Indicates prohibited actions.
Indicates mandatory actions.
Indicates the risk of electric shock.
Summary of Contents for F3SJ Series
Page 1: ...F3SJ A N Series Version 2 Safety Light Curtain User s Manual Cat No SCHG 719K...
Page 19: ...xvii F3SJ A User s Manual Introduction Contents E Revision History 202...
Page 20: ...xviii Introduction Contents F3SJ A User s Manual...
Page 184: ...164 Chapter 4 Wiring F3SJ A User s Manual Wiring Installation...
Page 192: ...172 Chapter 5 Wiring Examples F3SJ A User s Manual Input Output Circuit and Applications...