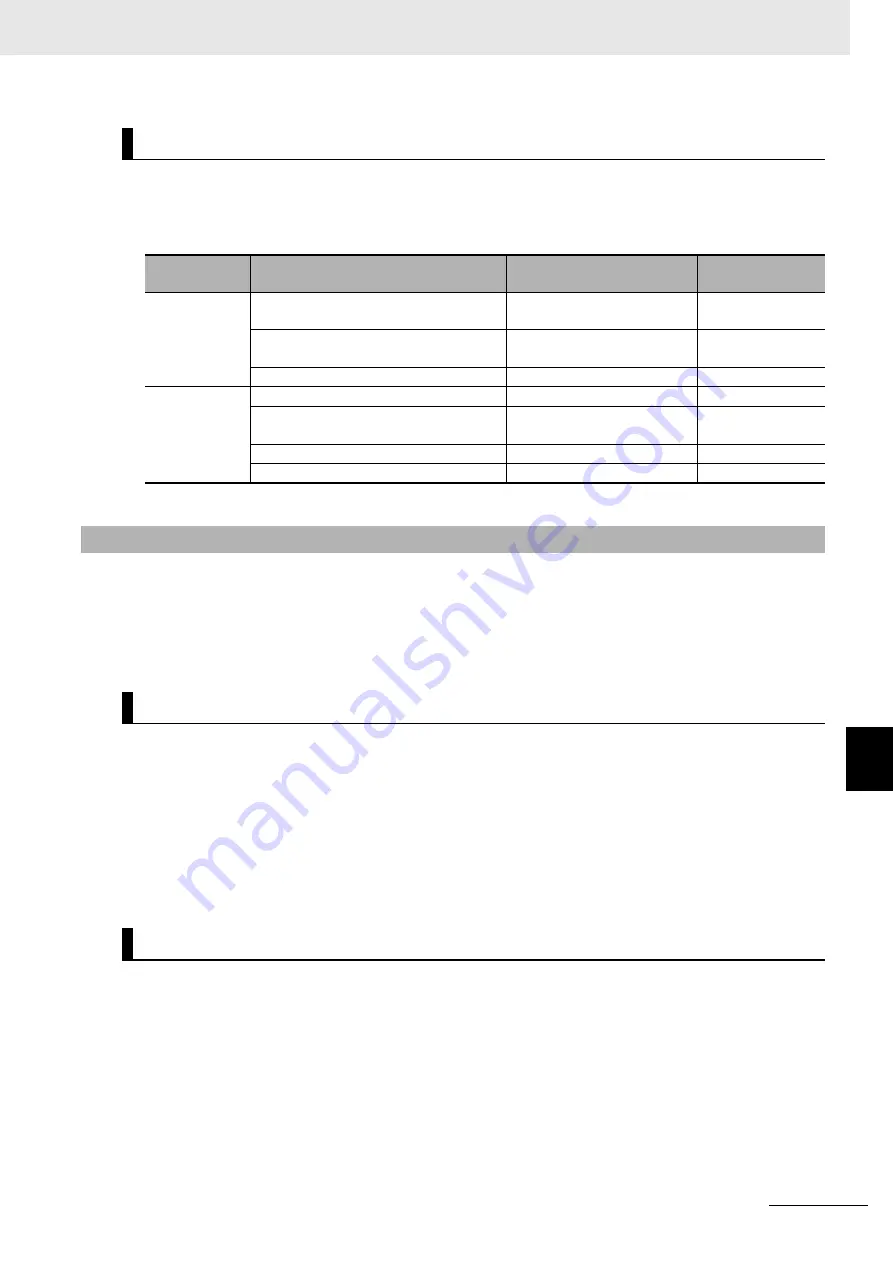
8 - 19
8 Troubleshooting and Maintenance
E3NW-ECT EtherCAT Digital Sensor Communication Unit Operation Manual (E429)
8-2
Equip
m
en
t Main
ten
ance
8
8-2-
3 Hand
ling when
Replacing Unit
s
Periodically inspect the following items to ensure that they do not deviate from the criteria.
If the items deviate from the criteria, adjust the environment so the criteria are met or adjust the Unit
itself.
Networks are constructed from an EtherCAT Master Unit and Slave Units.
If a Unit is malfunctioning, the entire network will be affected. The malfunctioning Unit must be replaced
quickly.
To restore network functions as quickly as possible, it is recommended that spare Units are kept on
hand ready to replace malfunctioning Units immediately.
Heed the following precautions when replacing nodes after a periodic inspection has revealed a
problem.
•
Check that the new Unit does not have errors after replacement.
•
If returning malfunctioning devices for repair, attach a detailed description of the malfunction to the
device and send the device to the OMRON representative listed at the end of this manual or to your
OMRON representative.
•
If contacts are defective, wipe them with a clean pure cotton cloth that has been soaked in industrial
alcohol.
After replacing a Unit, make the switch and other settings the same as before the Unit was replaced.
Inspection item
Inspection
item
Inspection details
Criteria
Inspection
method
Environment
Are the ambient and in-panel
temperatures appropriate?
0 to 55
°
C
Thermometer
Is the ambient and in-panel humidity
appropriate?
25% to 85% (with no
condensation or icing)
Hygrometer
Has dust collected?
No dust
Visual inspection
Installation
Has the Slave Unit been secured?
No looseness
Phillips screwdriver
Are the communications cable
connectors inserted properly?
No looseness
Visual inspection
Are the external wiring screws loose?
No looseness
Phillips screwdriver
Are the connection cables damaged?
No visible damage
Visual inspection
8-2-3
Handling when Replacing Units
Precautions when replacing Units
Settings after Unit replacement
Summary of Contents for E3NW-ECT
Page 1: ...E3NW ECT EtherCAT Digital Sensor Communication Unit Operation Manual E429 E1 07...
Page 3: ...E3NW ECT EtherCAT Digital Sensor Communication Unit Operation Manual Revised December 2017...
Page 4: ......
Page 170: ...Revision 2 E3NW ECT EtherCAT Digital Sensor Communication Unit Operation Manual E429...
Page 171: ......