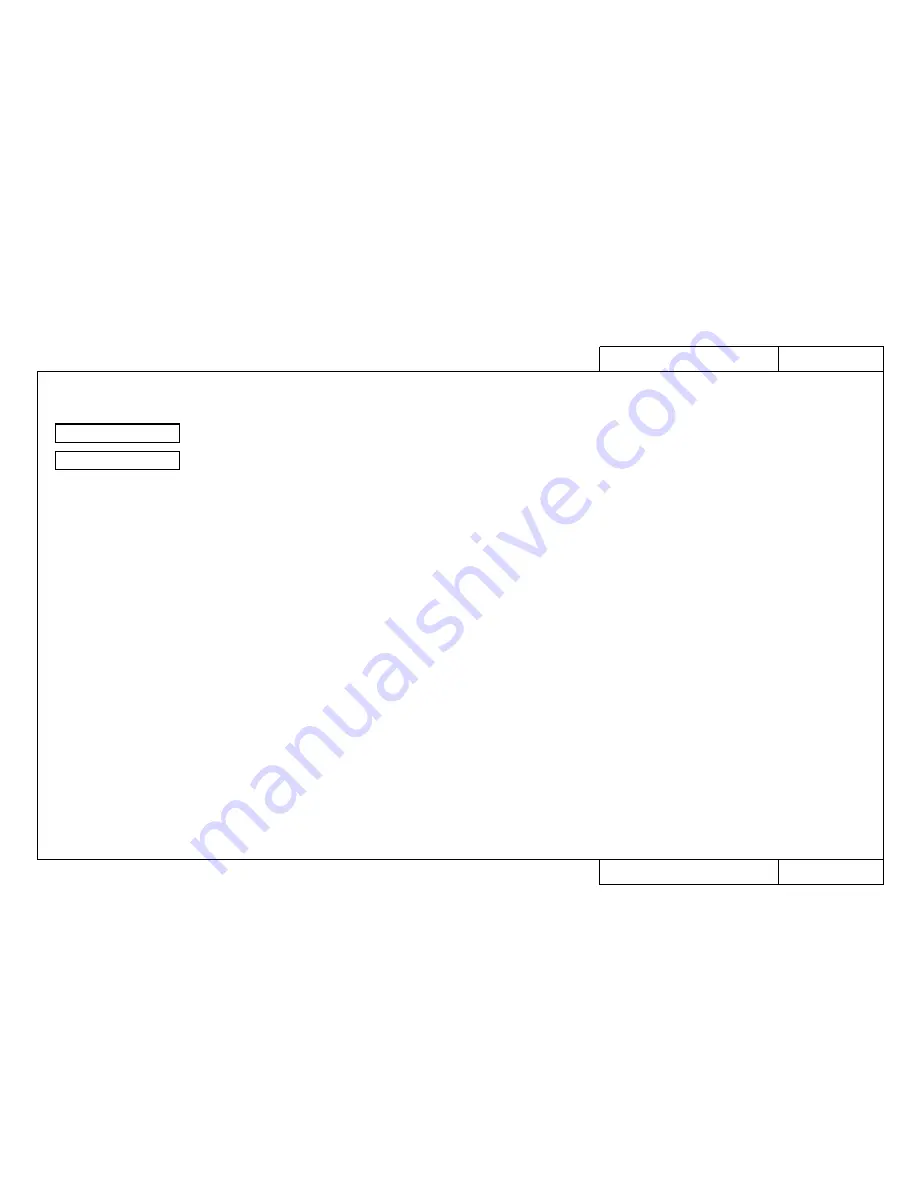
B A C 1 0 6 0
Model Name: Rockhopper-46/62
B A C 1 0 6 0
Model Name: Rockhopper-46/62
Examination: Fans
Examination: Fans
This procedure is used to verify that the fans are working by turning them on and
off.
Panel keys are ignored during fan on/off display. 5 seconds after displaying Fan Off,
the display will shift to “EXAM: Fan”.
Fan: On
Fan goes off 10 seconds after starting
Fan: Off
Displayed for 5 seconds after fan has gone off
EXAM: Fan