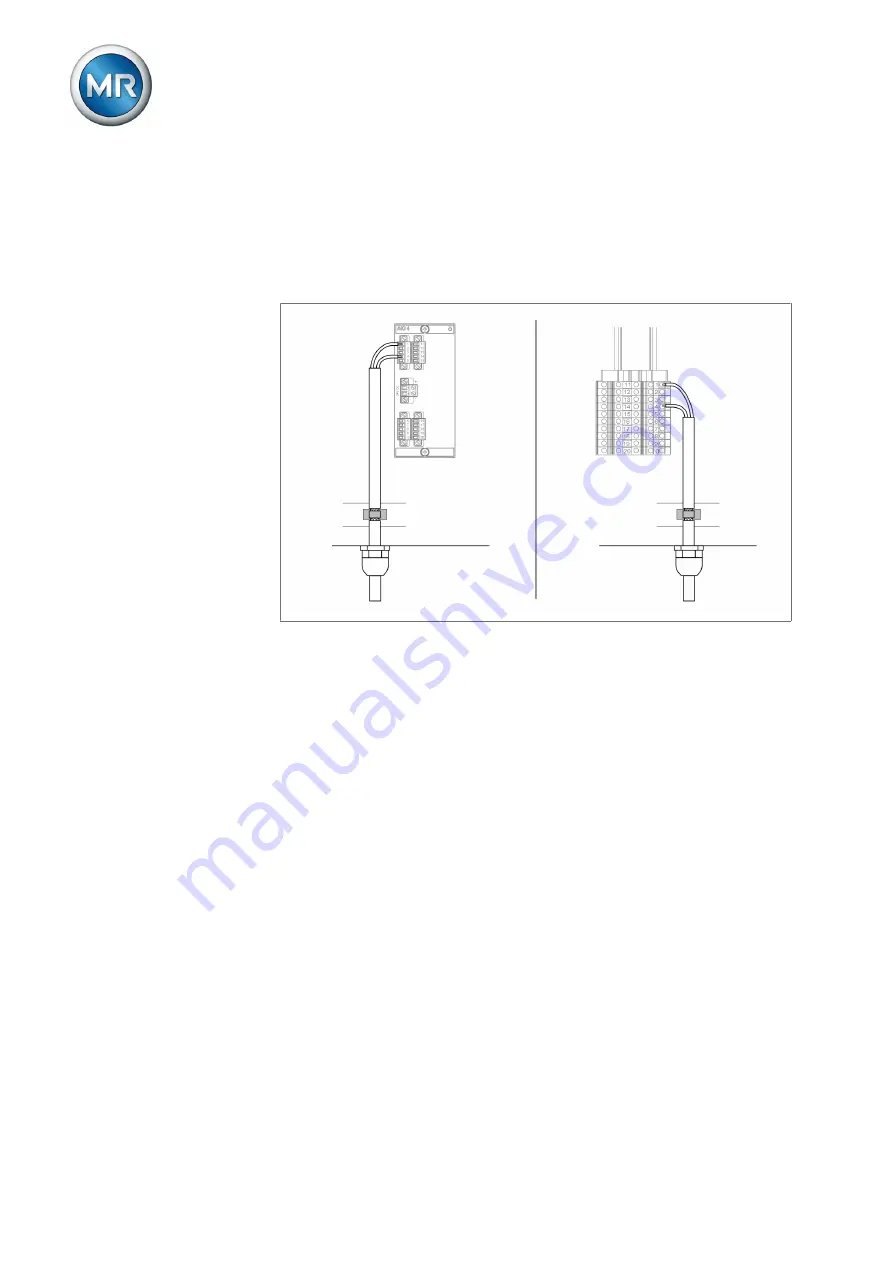
6 Mounting
Maschinenfabrik Reinhausen GmbH 2021
60
6796573/02 EN
MSENSE
®
VAM
6.3.4.4 Information about screening the cables for analog signals
In order to correctly record the analog signals, you must place the cable
screening in the motor-drive unit on the grounding bar. The cable shielding
should be removed as late as possible before connecting to keep the section
with unshielded cables as short as possible. The shielding must be con-
nected with shielding clips.
Figure 40: Examples of supporting screening on ground bar (on left: Direct connection to AIO
assembly, on right: Connection using line-up terminal)
6.3.5 Information about laying fiber-optic cable
To ensure the smooth transfer of data via the fiber-optic cable, you must en-
sure that mechanical loads are avoided when laying the fiber-optic cable and
later on during operation. Also observe the information from the manufac-
turer of the fiber-optic cable and the following instructions:
▪ Radii must not fall below the minimum permissible bend radii (do not bend
fiber-optic cable).
▪ The fiber-optic cables must not be over-stretched or crushed. Observe the
permissible load values.
▪ The fiber-optic cables must not be twisted.
▪ Be aware of sharp edges because they can damage the fiber-optic cable's
coating during laying or can place mechanical loads on the coating later
on.
▪ Provide a sufficient cable reserve near distributor cabinets. Lay the re-
serve such that the fiber-optic cable is neither bent nor twisted when tight-
ened.
Summary of Contents for MSENSE VAM
Page 1: ...Monitoring system MSENSE VAM Operating Instructions 6796573 02 EN ...
Page 172: ......
Page 173: ......