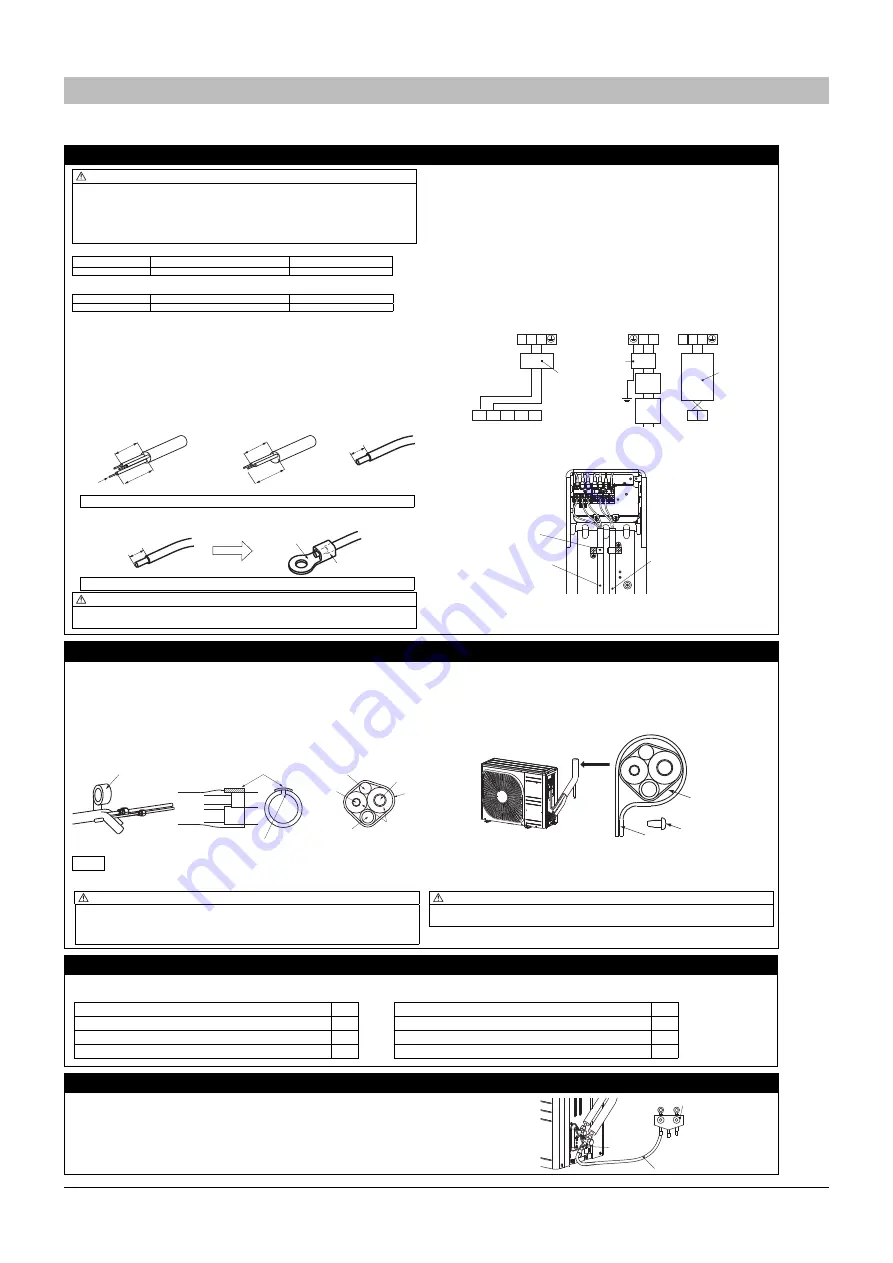
Installation
‘19 • HM-T-340
Outdoor unit installation
5. ELECTRICAL WIRING WORK
WARNING
• Make sure that all the electrical work is carried out in accordance with the national or regional
electrical standards.
• Make sure that the earth leakage breaker and circuit breaker of appropriate capacities are installed
(Refer to the table given below).
• Do not turn on the power until the electrical work is completed.
• Do not use a condensive capacitor for power factor improvement under any circumstances.
(It does not improve power factor. Moreover, it can cause an abnormal overheat accident).
Breaker specifi cations
Phase
Earth leakage breaker
Circuit breaker
Single phase
Leakage current: 30mA, 0.1sec or less
Over current: 20A
Main fuse specifi cation
Specifi cation
Parts No.
Code on LABEL,WIRING
250V 20A
SSA564A136A
F4
1.Preparing cable
(1) Selecting cable
Select the power source cable and connecting cable in accordance with the specifi cations mentioned below.
(a) Power source cable
3 cores* 2.0mm
2
or more, conformed with 60245 IEC57
When selecting the power source cable length, make sure that voltage drop is less than 2%.
If the wire length gets longer, increase the wire diameter.
(b) Connecting cable
2 cores* 1.5mm
2
, conformed with 60245 IEC57
* 1 Earth wire is included (Yellow).
(2) Arrange each wire length connecting to the outside unit as shown below.
Make sure that each wire is stripped 10mm from the end.
<Power source cable>
<Connecting cable>
<Wire end>
Earth wire
40mm or more
30mm or more
40mm or more
30mm or more
10mm
(3) Attach round crimp-type terminal to each wire connecting to the outside unit as shown in the below.
Select the size of round crimp-type terminal after considering the specifi cations of terminal block and wire
diameter.
10mm
Round crimp-type terminal
Sleeve
CAUTION
Power source cable and connecting cable must conform to the specifi cations mentioned in the manual.
Using cables with wrong specifi cations may result in unit malfunction.
2.Connecting cable
(1) Remove the service cover.
(2) Connect the cables according to the instructions and fi gures given below.
(a) Connect the earth wire of power source cable.
An earth wire must be connected before connecting the other wires of power source cable.
Keep the earth wire longer than the remaining two wires of power source cable.
(b) Connect the remaining two wires (N and L) of power source cable.
(c) Connect the wires of connecting cable. Make sure that for each wire, outdoor and indoor side ter-
minal numbers match.
(3) Fasten the cables properly with cable clamps so that no external force may work on terminal connec-
tions.
Moreover, make sure that cables do not touch the piping, etc. When cables are connected, make sure
that all electrical components within the electrical component box are free of loose connector coupling
or terminal connection.
<Circuit diagram>
N L
1 2/N 3
1 2
Circuit
breaker
Earth
leakage
breaker
Earth
Power
source
Indoor unit
(X100 terminal)
Indoor unit
(X10 terminal)
Outdoor unit
Outdoor unit
Indoor unit : HSB60-W
Connecting
cable
Power
source
cable
1 2/N 3
3
2
N
L
PE
Indoor unit : HMA60-S
Connecting
cable
Power
source
cable
Connecting
cable
Cable clamp
6. FINISHING WORK
1. Heating and condensation prevention
(1) Dress the connecting pipes (both liquid and gas pipes) with insulation to prevent it from heating
and dew condensation.
Use the heat insulating material which can withstand 120°C or higher temperature. Make sure that
insulation is wrapped tightly around the pipes and no gap is left between them.
(2) Wrap the refrigerant pipings of indoor unit with indoor unit heat insulation using tape.
(3) Cover the fl are-connected joints (indoor side) with the indoor unit heat insulation and wrap it with
an insulation pad (standard accessory provided with indoor unit).
(4) Wrap the connecting pipes, connecting cable and drain hose with the tape.
(2)
(3)
(4)
Tape
Insulation pad
Position it so that the slit area faces upward.
Connecting cable
Liquid pipe
Drain hose
Gas pipe
Insulation
Tape
NOTE
Locations where relative humidity exceeds 70%, both liquid and gas pipes need to be dressed with 20mm or
thicker heat insulation materials.
2.Finishing work
(1) Make sure that the exterior portion of connecting pipes, connecting cable and drain hose is wrapped
properly with tape. Shape the connecting pipes to match with the contours of the pipe assembly route.
(2) Fix the pipe assembly with the wall using clamps and screws. Pipe assembly should be anchored ev-
ery 1.5m or less to isolate the vibration.
(3) Install the service cover securely. Water may enter the unit if service cover is not installed properly,
resulting in unit malfunction and failure.
Pipe assembly
Screw
Clamp
CAUTION
• Improper insulation can cause condensate(water) formation during cooling operation.
Condensate can leak or drip causing damage to household property.
• Poor heat insulating capacity can cause pipe outer surface to reach high temperature during heating
operation. It can cause cable deterioration and personal injury.
CAUTION
Make sure that the connecting pipes do not touch the components within the unit. If pipes touch the
internal components, it may generate abnormal sounds and/or vibrations.
7. INSTALLATION TEST CHECK POINTS
After fi nishing the installation work, check the following points again before turning on the power.
Conduct test run (Refer to indoor unit installation manual) and ensure that the unit operates properly.
8. PUMP DOWN (IN CASE OF RELOCATION OR DISPOSAL OF UNIT)
(1) Connect charge hose of gauge manifold to service port of outdoor unit.
(2) Close the liquid service valve with hexagonal wrench key.
(3) Fully open the gas service valve with hexagonal wrench key.
(4) Carry out forced cooling operation (For forced cooling operation procedure, refer to indoor unit installation
manual).
(5) When the low pressure gauge becomes 0.01MPa, close the gas service valve and stop forced cooling
operation.
Service port
Gauge manifold
Charge hose
Power source voltage complies with the rated voltage of air-conditioner.
Earth leakage breaker and circuit breaker are installed.
Power cable and connecting cable are securely fi xed to the terminal block.
Both liquid and gas service valves are fully open.
No gas leaks from the joints of the service valves.
Indoor and outdoor side pipe joints have been insulated.
Drain hose (if installed) is fi xed properly.
Screw of the service cover is tightened properly.
Refer to the installation manual for Indoor unit when arrange each wire connecting to the Indoor unit.
Refer to the installation manual for Indoor unit when arrange each wire connecting to the Indoor unit.
- 67 -
#
Summary of Contents for FDCW100VNX-A
Page 7: ... 5 Technical data 19 HM T 340 Technical data ...
Page 36: ... 34 Technical data 19 HM T 340 Dimensions FDCW71VNX A Meaning of symbol ...
Page 38: ... 36 Technical data 19 HM T 340 FDCW140VNX A Meaning of symbol Dimensions ...
Page 41: ... 39 Technical data 19 HM T 340 Electrical circuit diagram ...
Page 42: ... 40 Technical data 19 HM T 340 Electrical circuit diagram ...
Page 43: ... 41 Technical data 19 HM T 340 Electrical circuit diagram ...
Page 44: ... 42 Technical data 19 HM T 340 Electrical circuit diagram ...
Page 45: ... 43 Technical data 19 HM T 340 Electrical circuit diagram ...
Page 46: ... 44 Technical data 19 HM T 340 Electrical circuit diagram ...
Page 47: ... 45 Technical data 19 HM T 340 Electrical circuit diagram ...
Page 48: ... 46 Technical data 19 HM T 340 Electrical circuit diagram ...
Page 49: ... 47 Technical data 19 HM T 340 Electrical circuit diagram Split box HSB60 W ...
Page 50: ... 48 Technical data 19 HM T 340 HSB100 Electrical circuit diagram ...
Page 51: ... 49 Technical data 19 HM T 340 HSB140 Electrical circuit diagram ...
Page 52: ... 50 Technical data 19 HM T 340 Electrical circuit diagram Outdoor units FDCW60VNX A ...
Page 57: ... 55 Technical data 19 HM T 340 Electrical circuit diagram POWER SOURCE RC HY20 W sheet 3 ...
Page 58: ... 56 Technical data 19 HM T 340 Electrical circuit diagram RC HY20 W sheet 4 ...
Page 61: ... 59 Technical data 19 HM T 340 Electrical circuit diagram POWER SOURCE RC HY40 W sheet 3 ...
Page 62: ... 60 Technical data 19 HM T 340 Electrical circuit diagram RC HY40 W sheet 4 ...
Page 64: ... 62 Technical data 19 HM T 340 Electrical circuit diagram RC HY40 W sheet 6 ...
Page 65: ...Installation 19 HM T 340 Installation 63 ...
Page 133: ...Control 19 HM T 340 Control 131 ...
Page 170: ... 168 Service 19 HM T 340 Service ...
Page 263: ... 258 Service 19 HM T 340 Outdoor unit FDCW60VNX FDCW71VNX Component replacement ...
Page 264: ...Service 259 19 HM T 340 FDCW100VNX FDCW140VNX LEK LEK Component replacement ...
Page 290: ... 285 Components 19 HM T 340 Components ...
Page 300: ... 295 Components 19 HM T 340 PT300 Component positions ...
Page 301: ... 296 Components 19 HM T 340 Component positions PT300 PT300 A mm 1634 B mm 743 C mm 673 ...
Page 302: ... 297 Components 19 HM T 340 PT500 Component positions ...
Page 303: ... 298 Components 19 HM T 340 PT500 Component positions PT500 A mm 1835 B mm 897 C mm 832 ...
Page 311: ...THo R THo A THo D Outside units FDCW60VNX 306 Components 19 HM T 340 Piping system ...