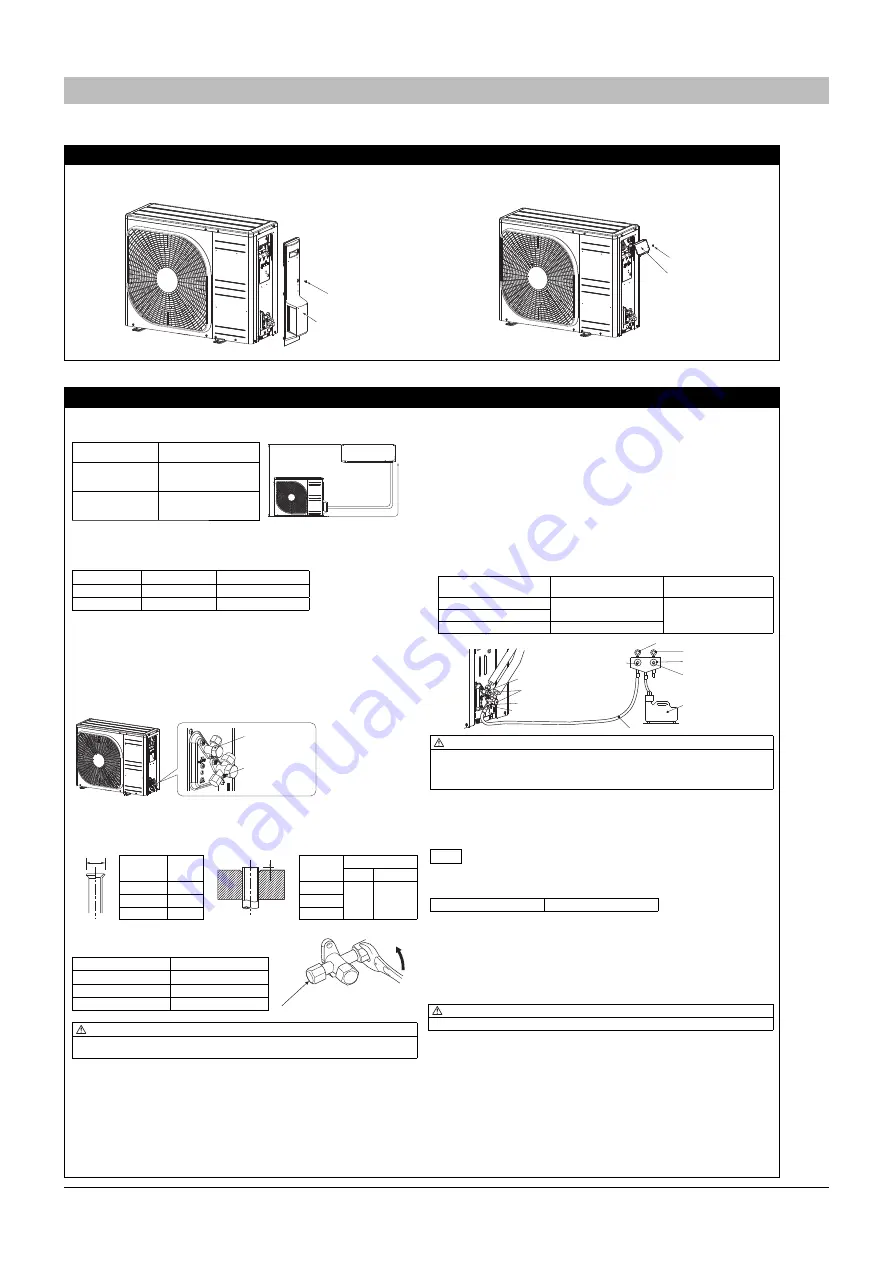
Installation
'19 • HM-T-340
Outdoor unit installation
3. PREPARATION FOR WORK
1. Removing service cover
Remove the screw. Slide service cover downwards and remove it.
2. Removing terminal cover
Remove the screw and take out terminal cover.
Screw
Service cover
Screw
Terminal cover
4. CONNECTING PIPING WORK
1. Restrictions on unit installation
Abide by the following restrictions on unit installation.
Improper installation can cause compressor failure or performance degradation.
Dimensional restrictions
H
L
Connecting pipe length(L)
30m or less
Elevation difference between
indoor and outdoor units(H)*
7m or less
* Outdoor unit installation position can be higher as well as lower than the indoor unit installation position.
2. Preparation of connecting pipe
2.1. Selecting connecting pipe
Select connecting pipe according to the following table.
Pipe diameter (mm)
Minimum thickness (mm)
Gas pipe
ø12.7
0.8
Liquid pipe
ø6.35
0.8
* Pipe material must be O-type (Phosphorus deoxidized seamless copper pipe ICS 23.040.15, ICS
77.150.30).
2.2. Cutting connecting pipe
(1) Cut the connecting pipe to the required length with pipe cutter.
(2) Hold the pipe downward and remove the burrs. Make sure that no foreign material enters the pipe.
(3) Cover the connecting pipe ends with the tape.
3. Piping work
Check that both liquid and gas service valves are fully closed.
Carry out the piping work with service valves fully closed.
Liquid service valve
Gas service valve
3.1. Flaring pipe
(1) Take out fl are nuts from the service valves of outdoor unit and engage them onto connecting pipes.
(2) Flare the pipes according to table and fi gure shown below.
Flare dimensions for R410A are diff erent from those for conventional refrigerant.
Although it is recommended to use the fl aring tools designed specifi cally for R410A, conventional fl aring
tools can also be used by adjusting the measurement of protrusion B with a fl are adjustment gauge.
A
Copper pipe
outer diameter
A 0
–0.4
B
Copper pipe
outer diameter
Rigid (clutch) type
R410A
Conventional
ø6.35
9.1
ø6.35
0–0.5
1.0–1.5
ø9.52
13.2
ø9.52
ø12.7
16.6
ø12.7
3.2. Connecting pipes
(1) Connect pipes on both liquid and gas sides.
(2) Tighten nuts to specifi ed torque shown in the table below.
Service valve size (mm)
Tightening torque (N·m)
ø6.35 (1/4")
14
–
18
ø9.52 (3/8")
34
–
42
ø12.7 (1/2")
49
–
61
Do not hold the valve cap area with a spanner
CAUTION
• Do not apply refrigerating machine oil to the fl ared surface. It can cause refrigerant leakage.
• Do not apply excess torque to the fl ared nuts. The fl ared nuts may crack resulting in refrigerant leakage.
4. Evacuation
(1) Connect vacuum pump to gauge manifold. Connect charge hose of gauge manifold to service port
of outdoor unit.
(2) Run the vacuum pump for at least one hour after the vacuum gauge shows -0.1MPa (–76cm Hg).
(3) Confi rm that the vacuum gauge indicator does not rise even if the system is left for 15 minutes or more.
Vacuum gauge indicator will rise if the system has moisture left inside or has a leakage point.
Check the system for the leakage point. If leakage point is found, repair it and return to (1) again.
(4) Close the Handle Lo and stop the vacuum pump.
Keep this state for a few minutes to make sure that the compound pressure gauge pointer does not
swing back.
(5) Remove valve caps from liquid service valve and gas service valve.
(6) Turn the liquid service valve's rod 90 degree counterclockwise with a hexagonal wrench key to open
valve.
Close it after 5 seconds, and check for gas leakage.
Using soapy water, check for gas leakage from indoor unit's fl are and outdoor unit's fl are and valve rods.
Wipe off all the water after completing the check.
(7) Disconnect charging hose from gas service valve's service port and fully open liquid and gas service
valves. (Do not attempt to turn valve rod beyond its stop.)
(8) Tighten service valve caps and service port cap to the specifi ed torque shown in the table below.
Service valve size (mm)
Service valve cap tightening
torque (N·m)
Service port cap tightening
torque (N·m)
ø6.35 (1/4")
20
–
30
10
–
12
ø9.52 (3/8")
ø12.7 (1/2")
25
–
35
Charge hose
Handle Lo
Valve cap
Liquid service valve
Gas service valve
Service port
Compound pressure gauge
Pressure gauge
Gauge manifold
Handle Hi
Vacuum pump
CAUTION
• To prevent diff erent oil from entering into the refrigeration system, do not use tools designed for any
other refrigerant type (R22, R407C, etc.).
• To prevent vacuum pump oil from entering into the refrigeration system, use a counterfl ow prevention
adapter.
5. Additional refrigerant charge
Additional refrigerant charge is required only when connecting pipe length exceeds 15 m.
5.1 Calculating additional refrigerant charge
Additional refrigerant charge can be calculated using the formula given below.
Additional refrigerant charge (g) = { Connecting pipe length (m) – Factory charged length 15 (m) } x 20 (g/m)
NOTE
• If additional refrigerant charge calculation result is negative, there is no need to remove the refrigerant.
• If refrigerant recharge is required for the unit with connecting pipe length 15m or shorter, charge the
factory charged volume as shown in the table below.
Factory charged volume(kg)
1.50
5.2 Charging refrigerant
(1) Charge the R410A refrigerant in liquid phase from service port with both liquid and gas service
valves shut. Since R410A refrigerant must be charged in the liquid phase, make sure that refriger-
ant is discharged from the cylinder in the liquid phase all the time.
(2) When it is difficult to charge a required refrigerant volume, fully open both liquid and gas service
valves and charge refrigerant, while running the unit in the cooling mode. When refrigerant is
charged with the unit being run, complete the charge operation within 30 minutes.
(3) Write the additional refrigerant charge calculated from the connecting pipe length on the label at-
tached on the service cover.
CAUTION
Running the unit with an insuffi cient quantity of refrigerant for a long time can cause unit malfunction.
- 66 -
Summary of Contents for FDCW100VNX-A
Page 7: ... 5 Technical data 19 HM T 340 Technical data ...
Page 36: ... 34 Technical data 19 HM T 340 Dimensions FDCW71VNX A Meaning of symbol ...
Page 38: ... 36 Technical data 19 HM T 340 FDCW140VNX A Meaning of symbol Dimensions ...
Page 41: ... 39 Technical data 19 HM T 340 Electrical circuit diagram ...
Page 42: ... 40 Technical data 19 HM T 340 Electrical circuit diagram ...
Page 43: ... 41 Technical data 19 HM T 340 Electrical circuit diagram ...
Page 44: ... 42 Technical data 19 HM T 340 Electrical circuit diagram ...
Page 45: ... 43 Technical data 19 HM T 340 Electrical circuit diagram ...
Page 46: ... 44 Technical data 19 HM T 340 Electrical circuit diagram ...
Page 47: ... 45 Technical data 19 HM T 340 Electrical circuit diagram ...
Page 48: ... 46 Technical data 19 HM T 340 Electrical circuit diagram ...
Page 49: ... 47 Technical data 19 HM T 340 Electrical circuit diagram Split box HSB60 W ...
Page 50: ... 48 Technical data 19 HM T 340 HSB100 Electrical circuit diagram ...
Page 51: ... 49 Technical data 19 HM T 340 HSB140 Electrical circuit diagram ...
Page 52: ... 50 Technical data 19 HM T 340 Electrical circuit diagram Outdoor units FDCW60VNX A ...
Page 57: ... 55 Technical data 19 HM T 340 Electrical circuit diagram POWER SOURCE RC HY20 W sheet 3 ...
Page 58: ... 56 Technical data 19 HM T 340 Electrical circuit diagram RC HY20 W sheet 4 ...
Page 61: ... 59 Technical data 19 HM T 340 Electrical circuit diagram POWER SOURCE RC HY40 W sheet 3 ...
Page 62: ... 60 Technical data 19 HM T 340 Electrical circuit diagram RC HY40 W sheet 4 ...
Page 64: ... 62 Technical data 19 HM T 340 Electrical circuit diagram RC HY40 W sheet 6 ...
Page 65: ...Installation 19 HM T 340 Installation 63 ...
Page 133: ...Control 19 HM T 340 Control 131 ...
Page 170: ... 168 Service 19 HM T 340 Service ...
Page 263: ... 258 Service 19 HM T 340 Outdoor unit FDCW60VNX FDCW71VNX Component replacement ...
Page 264: ...Service 259 19 HM T 340 FDCW100VNX FDCW140VNX LEK LEK Component replacement ...
Page 290: ... 285 Components 19 HM T 340 Components ...
Page 300: ... 295 Components 19 HM T 340 PT300 Component positions ...
Page 301: ... 296 Components 19 HM T 340 Component positions PT300 PT300 A mm 1634 B mm 743 C mm 673 ...
Page 302: ... 297 Components 19 HM T 340 PT500 Component positions ...
Page 303: ... 298 Components 19 HM T 340 PT500 Component positions PT500 A mm 1835 B mm 897 C mm 832 ...
Page 311: ...THo R THo A THo D Outside units FDCW60VNX 306 Components 19 HM T 340 Piping system ...