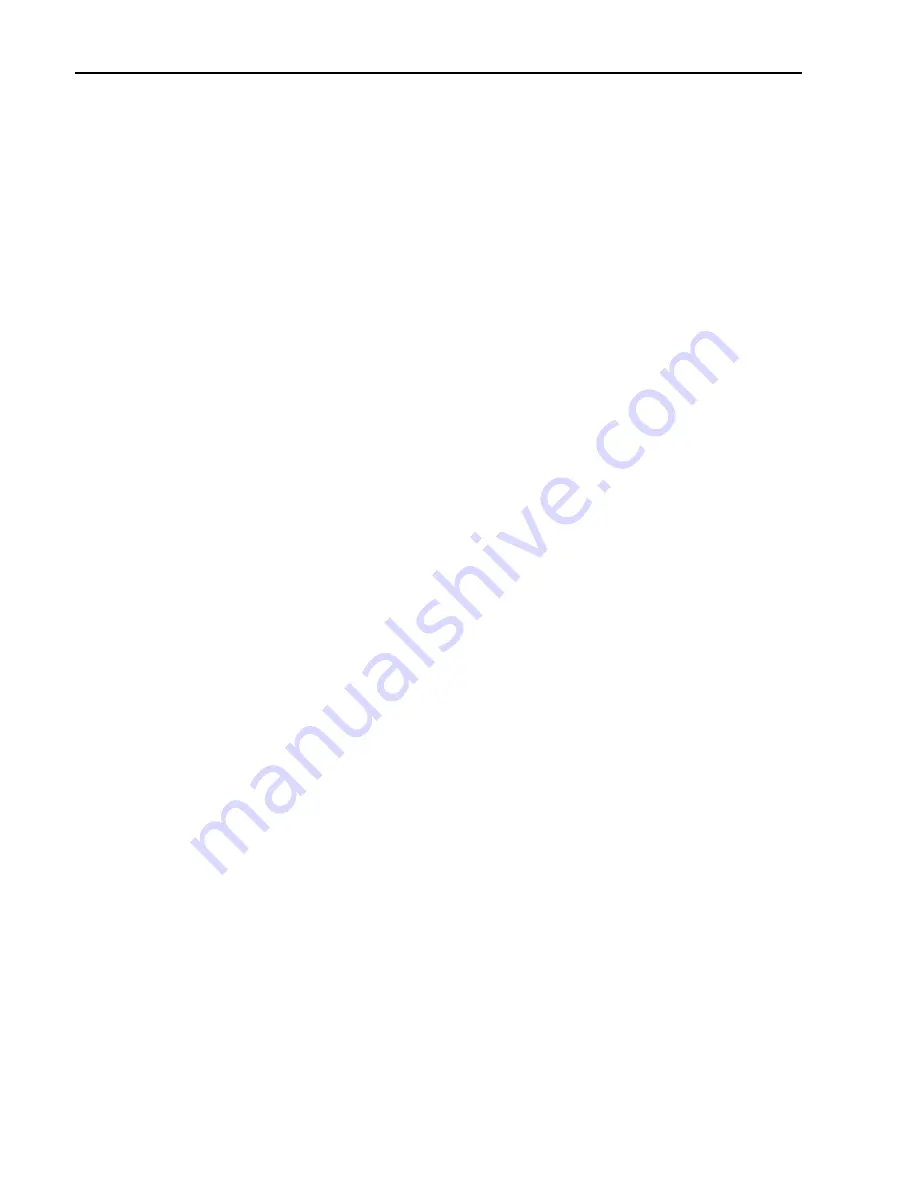
- 352 -
[
IX
Troubleshooting ]
1) Check that the main power is OFF.
When replacing the compressor due to megger failure and when the megger is 1M ohm or more, megger drop is
likely due to the liquified refrigerant entering and accumulating in the compressor. Turn the power off after powering
the crankcase heater at least 12 hours, and apply megger again.
2) Remove the fin guard, the front panel and the front partition plate on the right (as you face the front).
3) Collect the refrigerant from the service check joints on both high and low-pressure sides.
When collecting refrigerant from the accumulator, perform proper work with the reference of refrigerant collecting
method from the accumulator.
4) Collect the oil from the drain oil pipe that is located on the oil balance pipe.
Note:
When collecting the oil, prepare an approximately 10-liter container.
Keep collecting oil until the oil in the drain oil plug clears up.
Keep track of the amount of collected oil, as the same amount of oil will be added.
Do not splash oil.Do not leave the refrigerant circuit open for a long time, as the oil rapidly absorbs moisture.
The collected oil cannot be reused.
5) After draining oil from the refrigerant and the drain oil plug, remove the metal fitting-1 or the flare nuts (2 places)
that connect the compressor and the oil balance pipe, and bend the oil balance pipe so as not to apply an excess
force.
6) Close the oil balance pipe attachment point with a cap to prevent the oil from leaking.
7) Remove the compressor terminal cover, and remove the power supply wiring.
8) Remove the discharge temperature thermistor and the sound-proof material that is wrapped around the compres-
sor.
9) Remove the crankcase heater.
10) Heat the brazed part of the discharge pipe and the suction pipe, and remove the pipes.
11) Remove the compressor fixing nuts and the metal fitting-2 (3 places on compressor-2).
12) Replace the compressor with the service compressor.
13) Braze the discharge pipe and the suction pipe.
14) Attach the oil balance pipe to both compressors.Attach the oil balance pipe to both compressors.After replacing
the dryer, do not leave the refrigerant circuit open for long time.
Note:
When replacing the compressor and when the equal oil pipe is damaged or irreparably deformed, after replacing
the compressor, heat the junction of the equal oil pipe, remove the equal oil pipe, and braze the service equal oil
pipe.
15) Close the ball valves in the outdoor unit (both on the liquid and the gas side), and pressurize up to 4.15MPa [601si]
with nitrogen from the check joints for high and low-pressure service.
16) After confirming the airtightness, release the nitrogen gas.
17) Open the ball valves in the outdoor unit (both on the liquid and the gas side), and perform vacuuming.
18) While vacuuming, add the same amount of oil that is collected from the drain oil plug on the oil balance pipe in
the procedure 4).
Note:
The oil to be added must be MEL32 made by Nisseki Mitsubishi.When adding oil, the oil must not absorb moisture,
and do not use the oil that is over a year old.
Do not draw out the oil in the compressor when returning the compressor to find the cause of compressor malfunction.
19) Attach the crankcase heater.
Note: Attach the appropriate crankcase heater to the appropriate compressor.
20) Attach the soundproof material to the compressor.
21) Attach the discharge temperature thermistor, and attach the insulation.
22) Attach the power source wire to the terminal on the compressor.
23) After vacuuming, calculate the amount of added refrigerant at factory shipment and the amount of added refrig-
erant on site, and charge the system.
24) After reconfirming the power source-wiring phase, apply a megger, attach the terminal cover, turn on the main
power, and check whether the crankcase heater is powered.
25) Check that the ball valves (both on the liquid and the gas side) are open.
26) Operate all the indoor units, and check whether they run properly.
27) If there is something that needs to be improved in the installation or the usage, explain that to the customers.
Summary of Contents for PUHY-P168
Page 11: ... 2 ...
Page 23: ... 14 ...
Page 25: ... 16 ...
Page 38: ... 29 II Restrictions ...
Page 42: ... 33 II Restrictions ...
Page 46: ... 37 II Restrictions ...
Page 50: ... 41 II Restrictions ...
Page 54: ... 45 II Restrictions ...
Page 58: ... 49 II Restrictions ...
Page 75: ... 66 ...
Page 101: ... 92 ...
Page 111: ... 102 ...
Page 113: ... 104 ...
Page 127: ... 118 ...
Page 145: ... 136 ...
Page 147: ... 138 ...
Page 185: ... 176 ...
Page 187: ... 178 ...
Page 241: ... 232 ...
Page 243: ... 234 ...
Page 366: ... 357 IX Troubleshooting ...
Page 367: ... 358 ...
Page 369: ... 360 ...