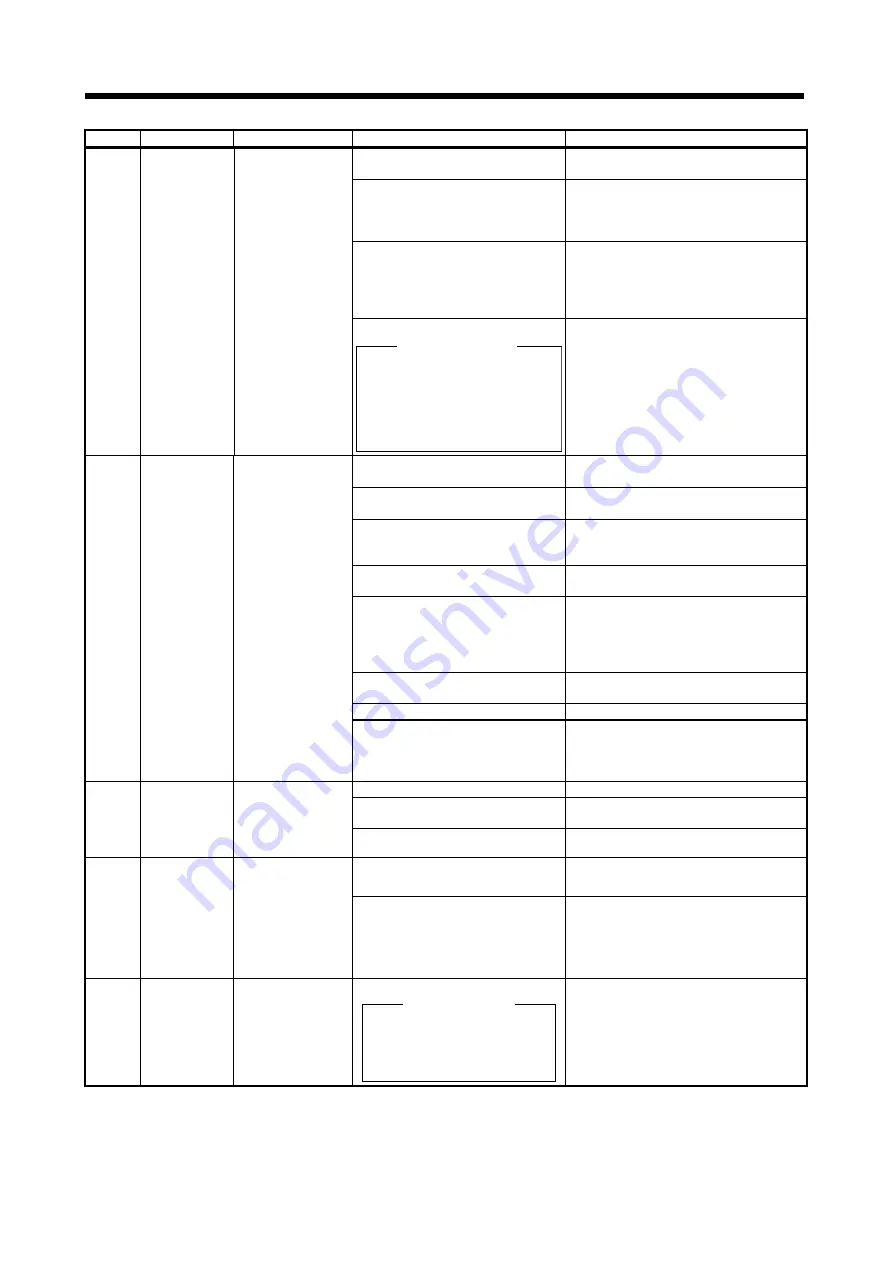
WWW.NNC.IR
10 - 12
10. TROUBLESHOOTING
Display
Name
Definition
Cause
Action
1. Machine struck something.
1. Review operation pattern.
2. Install limit switches.
2. Wrong connection of servo motor.
Servo amplifier's output terminals
U, V, W do not match servo
motor's input terminals U, V, W.
Connect correctly.
3. Servo system is instable and
hunting.
1. Repeat acceleration/deceleration to
execute auto tuning.
2. Change auto tuning response setting.
3. Set auto tuning to OFF and make gain
adjustment manually.
AL.51
Overload 2
Machine collision or
the like caused max.
For the time of the
alarm occurrence,
refer to the section
12.1.
4. Encoder faulty.
Checking method
When the servo motor shaft is
rotated with the servo off, the
cumulative feedback pulses do
not vary in proportion to the
rotary angle of the shaft but the
indication skips or returns midway.
Change the servo motor.
1. Acceleration/deceleration time
constant is too small.
Increase the acceleration/deceleration
time constant.
2. Torque limit value (parameter
No.28) is too small.
Increase the torque limit value.
3. Motor cannot be started due to
torque shortage caused by power
supply voltage drop.
1. Review the power supply capacity.
2. Use servo motor which provides larger
output.
4. Position control gain 1 (parameter
No.6) value is small.
Increase set value and adjust to ensure
proper operation.
5. Servo motor shaft was rotated by
external force.
1. When torque is limited, increase the
limit value.
2. Reduce load.
3. Use servo motor that provides larger
output.
6. Machine struck something.
1. Review operation pattern.
2. Install limit switches.
7. Encoder faulty
Change the servo motor.
AL.52
Error excessive
(Note)
The difference
between the model
position and the
actual servo motor
position exceeds 2.5
rotations.
(Refer to the
function block
diagram in section
1.2)
8. Wrong connection of servo motor.
Servo amplifier's output terminals
U, V, W do not match servo
motor's input terminals U, V, W.
Connect correctly.
1. Communication cable breakage.
Repair or change the communication cable
2. Communication cycle longer than
parameter No. 56 setting.
Set correct value in parameter.
AL.8A
Serial
communication
time-out error
RS-232C or RS-422
communication
stopped for longer
than the time set in
parameter No.56.
3. Wrong protocol.
Correct protocol.
1. Communication cable fault
(Open cable or short circuit)
Repair or change the cable.
AL.8E
Serial
communication
error
Serial
communication
error occurred
between servo
amplifier and
communication
device (e.g. personal
computer).
2. Communication device (e.g.
personal computer) faulty
Change the communication device (e.g.
personal computer).
88888 Watchdog
CPU, parts faulty
Fault of parts in servo amplifier
Checking method
Alarm (88888) occurs if power
is switched on after disconnection
of all cables but the control circuit
power supply cable.
Change the servo amplifier.
Note. The error excessive detection for 2.5 revolutions is available only when the servo amplifier of software version B0 or later is used.
For the servo amplifier of software version older than B0, an error excessive alarm occurs when the deviation (deviation counter
value) between the instructed position and the actual servo motor position exceeds 10 revolutions.
Summary of Contents for MR-J2S-*A
Page 13: ...WWW NNC IR A 12 MEMO ...
Page 117: ...WWW NNC IR 3 70 3 SIGNALS AND WIRING MEMO ...
Page 185: ...WWW NNC IR 7 12 7 GENERAL GAIN ADJUSTMENT MEMO ...
Page 195: ...WWW NNC IR 8 10 8 SPECIAL ADJUSTMENT FUNCTIONS MEMO ...
Page 197: ...WWW NNC IR 9 2 9 INSPECTION MEMO ...
Page 221: ...WWW NNC IR 11 10 11 OUTLINE DIMENSION DRAWINGS MEMO ...
Page 293: ...WWW NNC IR 13 64 13 OPTIONS AND AUXILIARY EQUIPMENT MEMO ...
Page 321: ...WWW NNC IR 14 28 14 COMMUNICATION FUNCTIONS MEMO ...
Page 389: ...WWW NNC IR 15 68 15 ABSOLUTE POSITION DETECTION SYSTEM MEMO ...