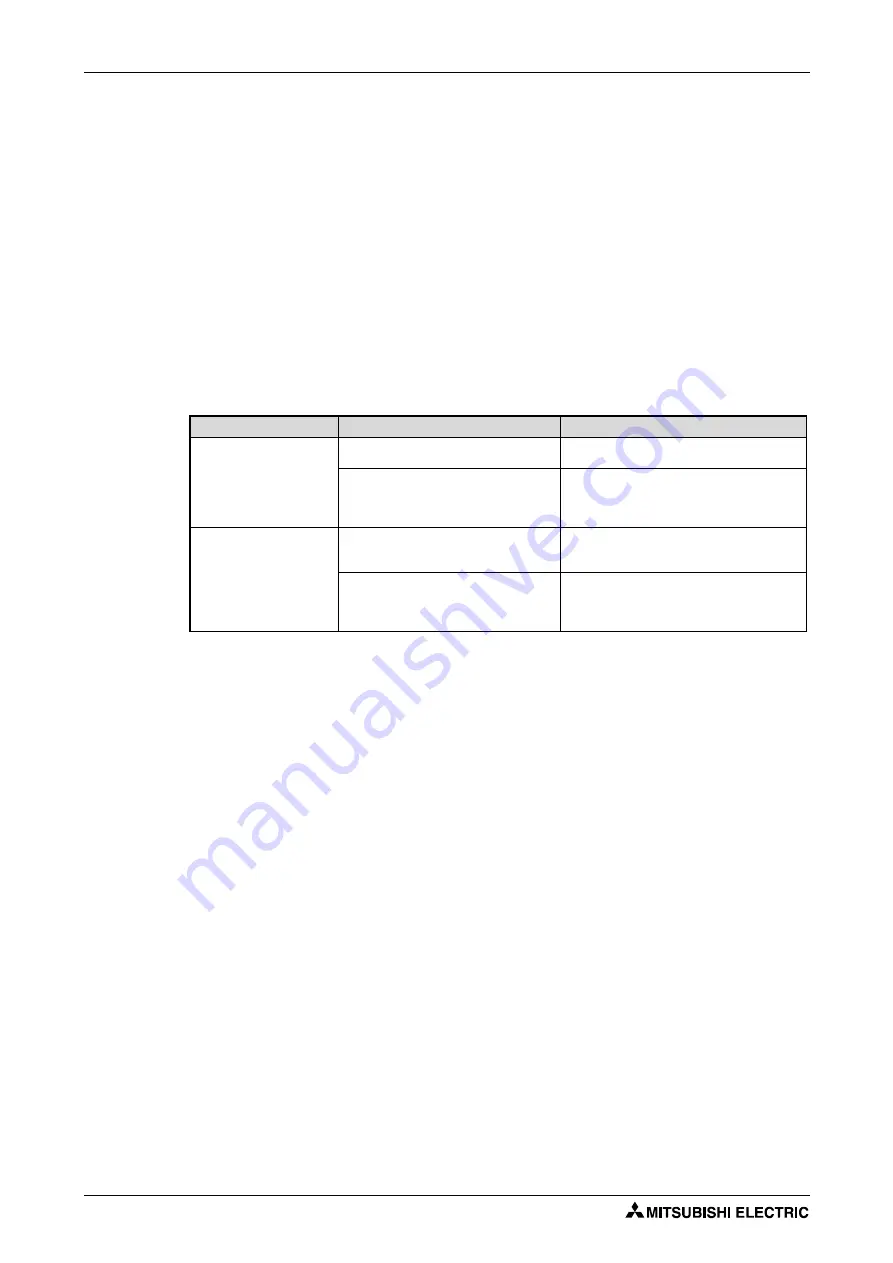
Operation
Procedures before Operation
4 - 4
Servo on
Switch the servo-on in the following procedure:
Switch on main circuit and control circuit power supply.
The controller transmits the "servo ON" command.
When placed in the "servo ON" status, the servo amplifier is ready to operate and the servo
motor is locked.
Home position return
Always perform home position return before starting positioning operation.
Stop
If any of the following situations occurs, the servo amplifier suspends the running of the servo
motor and brings it to a stop.
When the servo motor is equipped with an electromagnetic brake, refer to section 3.7.
Operation
Stopping condition
Servo system controller
"Servo OFF" command
The base circuit is shut off and the servo
motor coasts.
Emergency stop command
The base circuit is shut off and the dynamic
brake operates to bring the servo motor to
stop. The controller emergency stop warning
(E7) occurs.
Servo amplifier
Alarm occurrence
The base circuit is shut off and the dynamic
brake operates to bring the servo motor to
stop.
External EMERGENCY OFF switch
(EM1) is pressed.
The base circuit is shut off and the dynamic
brake operates to bring the servo motor to
stop. The servo forced stop warning (E6)
occurs.
Tab. 4-2:
Stopping condition
Summary of Contents for MELSERVO MRJ2S-B
Page 2: ......
Page 4: ......
Page 6: ......
Page 14: ...VIII ...
Page 18: ...Contents XII ...
Page 48: ...Introduction System configuration 1 30 ...
Page 58: ...Installation General environmental conditions 2 10 ...
Page 86: ...Connection Station number setting 3 28 ...
Page 122: ...Operation Gain 4 36 ...
Page 134: ...Absolute position detection system General description 6 6 ...
Page 146: ...Accessories Special accessories 7 12 ...
Page 148: ...Maintenance and Inspection Life 8 2 ...
Page 174: ...Specifications Standard specifications 10 16 ...
Page 176: ...EMC Directives Requirements 11 2 ...
Page 198: ...Index iv ...
Page 199: ......