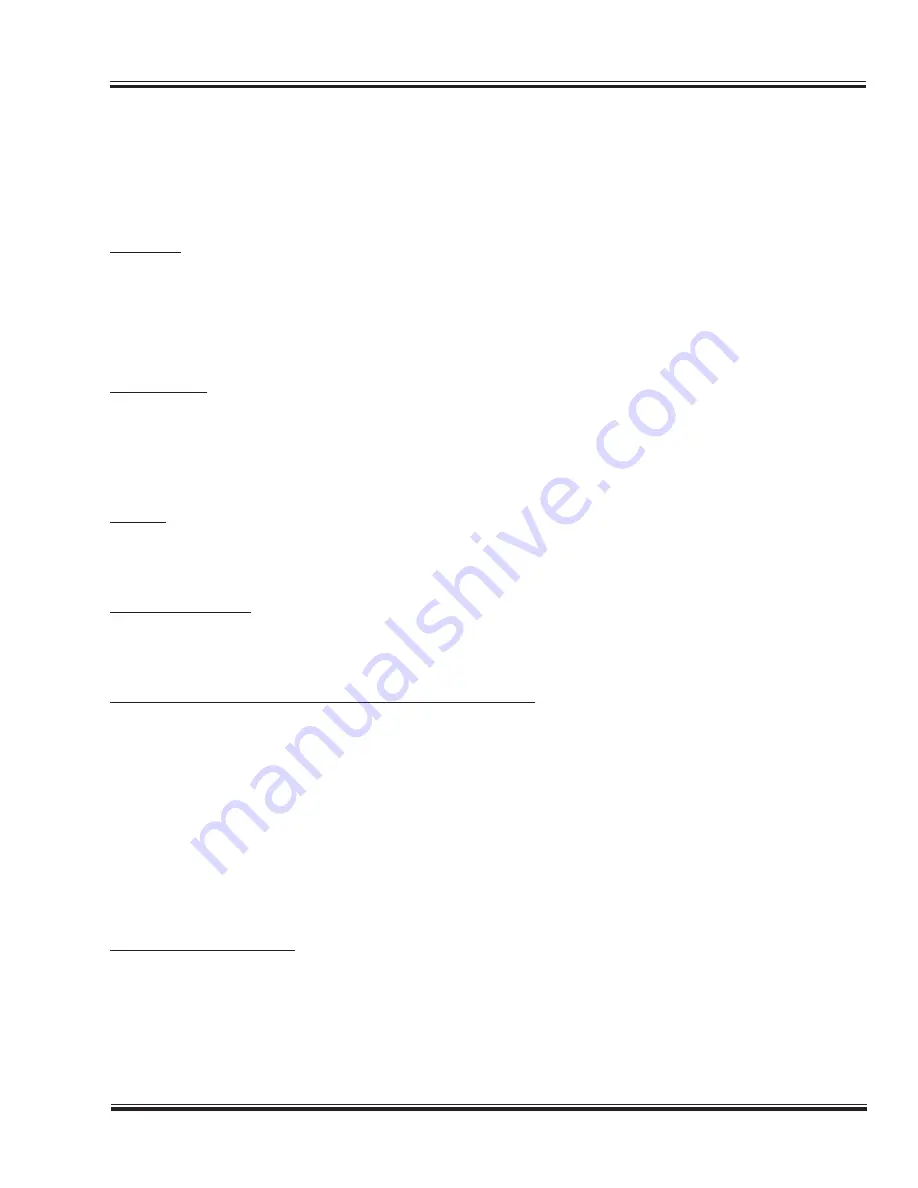
MACHINE WARRANTY
LX1214 Professional Series Bagger
MILLER-ST. NAZIANZ, INC. warrants each new Ag-Bag® LX1214 professional series bagger to be free
from defects in material and workmanship under recommended use and service, as stated in the Opera-
tor’s Manual, as follows:
Warranty
Miller will replace, F.O.B. St. Nazianz, Wisconsin, or repair, as Miller elects, any part of a new LX1214
professional series bagger which is defective in material or workmanship: Without charge for either parts
or labor during the first year following delivery to the original retail customer.
All warranties on the new LX1214 professional series bagger shall apply only to the original retail purchaser
from an authorized Ag-Bag dealer.
Repair Parts
Miller warrants that it will replace the failed part F.O.B. St. Nazianz, Wisconsin, or repair, as Miller elects,
without charge, any genuine Ag-Bag spare part purchased after the expiration of the new LX1214 profes-
sional series bagger warranty, or to any subsequent owners that is defective in material or workmanship,
within ninety (90) days of the installation date. Repair parts warranty does not cover labor to remove or
replace the failed part.
Misuse
The provisions of this warranty shall not apply to any LX1214 professional series bagger which has been
subject to misuse, negligence, alteration or accident, or which shall have been repaired with parts other
than those obtainable through Ag-Bag.
Authorized Dealer
Repairs eligible for labor warranty must be made by Ag-Bag or an authorized Ag-Bag dealer. The pur-
chaser is responsible for transportation of the equipment to the dealership for warranty service or for any
service call expense.
Exclusive Effect of Warranty and Limitation of Liability
The remedies of the customer set forth herein are exclusive. Miller neither assumes nor authorizes any
person to assume any other obligation or liability in connection with the sale of covered equipment. Cor-
rection of defects and malfunctions in the manner and for the applicable period of time provided above
shall constitute fulfillment of all responsibilities of Miller to the customer and Miller shall not be liable for
negligence, under contract, or in any other manner with respect to such equipment. IN NO EVENT SHALL
THE OWNER BE ENTITLED TO RECOVER FOR INCIDENTAL OR CONSEQUENTIAL DAMAGES SUCH
AS BUT NOT LIMITED TO: LOSS OF CROPS, LOSS OF PROFITS OR REVENUE, OTHER COMMER-
CIAL LOSSES, INCONVENIENCE OR COST OF RENTAL OF REPLACEMENT EQUIPMENT.
THIS WARRANTY IS IN LIEU OF ALL WARRANTIES OF MERCHANTABILITY, FITNESS FOR A PUR-
POSE OR OTHER WARRANTIES, EXPRESS OR IMPLIED.
Warranty Requirements
To be covered by warranty, each machine must be properly registered with Miller within 30 days of date
of original retail delivery.
Summary of Contents for AG-BAG Professional LX1214
Page 20: ...14 Safety Sign and Decal Locations...
Page 21: ...15 Safety Sign and Decal Locations continued...
Page 128: ...122 Maintenance Record Date Service Performed...
Page 129: ...123 Date Service Performed...
Page 130: ...124 Date Service Performed...
Page 158: ...2014 by Miller St Nazianz Inc...