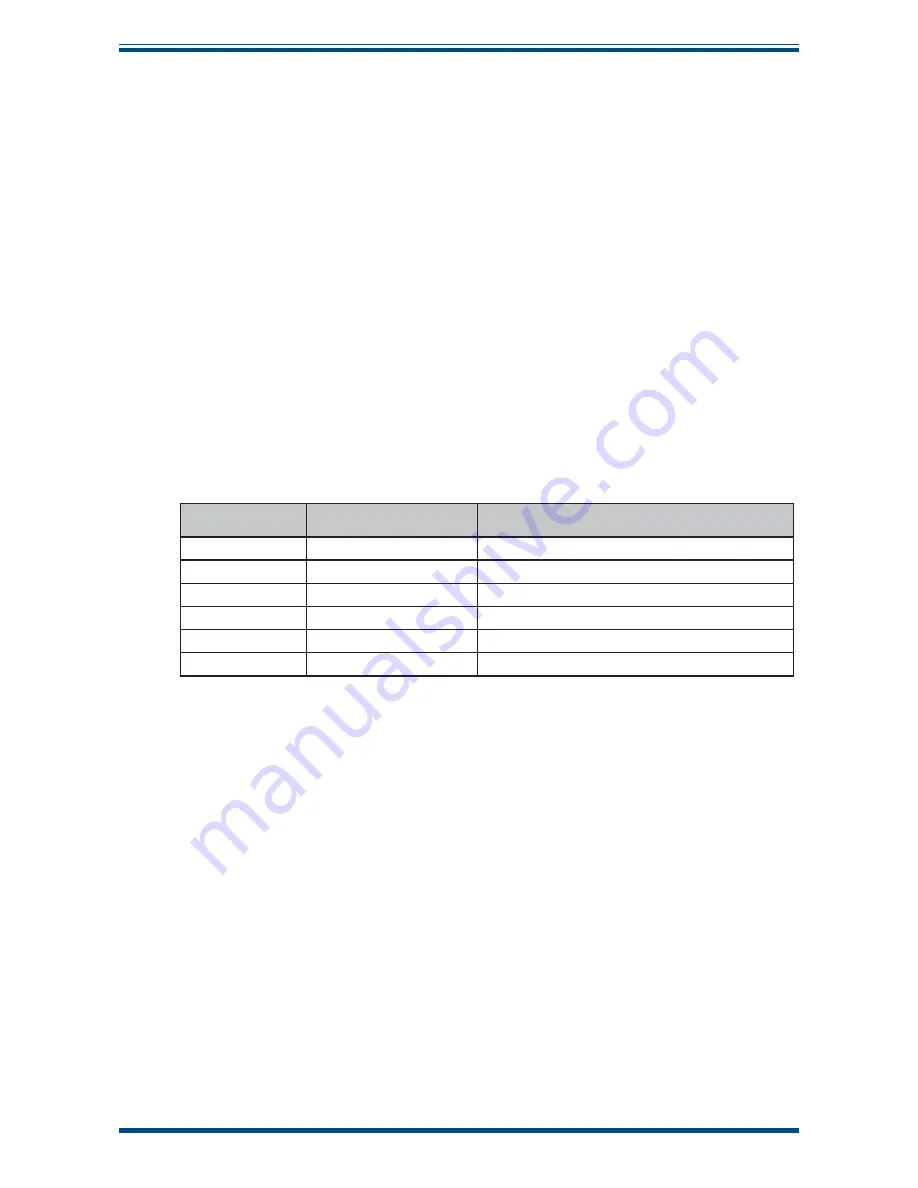
XZR500 User’s Manual
Michell Instruments
7
INTRODUCTION
• Dimensions
(mm):
Control Unit:
300 x 300 x 200 (w x h x d)
Sensor Head:
135 x 290 x 670 (w x h x d) (standard model)
Probe:
400, 600 or 900mm in length, with an outer diameter of 40mm
• Weight:
Control Unit:
Approximately 7 kg
Sensor Head:
Approximately 3 kg
Probe:
Approximately 2-6 kg (dependant upon length & material of
construction)
• Power
requirements:
230 or 115 V, -15%/+10%, 50/60 Hz
•
Operating ambient temperature and moisture:
Temperature from 0 to 55°C
Relative moisture from 5% to 90% (non-condensing)
•
Maximum temperature of the sample gases
(Table 2):
Model
Tubing Materials
Gas Properties
XZR500 /SS
304 L stainless steel
Tmax = 700°C
XZR500 /IL
Inconel 600
Tmax = 1000°C
XZR500 /HR
HR160
Tmax = 1000°C and corrosive gases
XZR500 /HC
Hastelloy C2000
Tmax = 600°C and corrosive gases
XZR500 /CC
Ceramic
Tmax = 1300°C
XZR500 /HL
Halar coating
Tmax = 150°C
Table 2
Maximum Temperature of Gases
•
Minimum speed of the sample gases:
0.5 m/s
Summary of Contents for XZR500ST
Page 1: ...XZR500ST Oxygen Analyzer User s Manual 97137 Issue 8 April 2017...
Page 55: ...XZR500 User s Manual Michell Instruments 47 APPENDIX C Appendix C Calculation of CO2...
Page 66: ...XZR500 User s Manual 58 97137 Issue 8 April 2017 APPENDIX G Appendix G Mounting Options...
Page 69: ...XZR500 User s Manual Michell Instruments 61 APPENDIX H Appendix H Second 4 20mA Output...
Page 77: ......
Page 78: ...http www michell com...