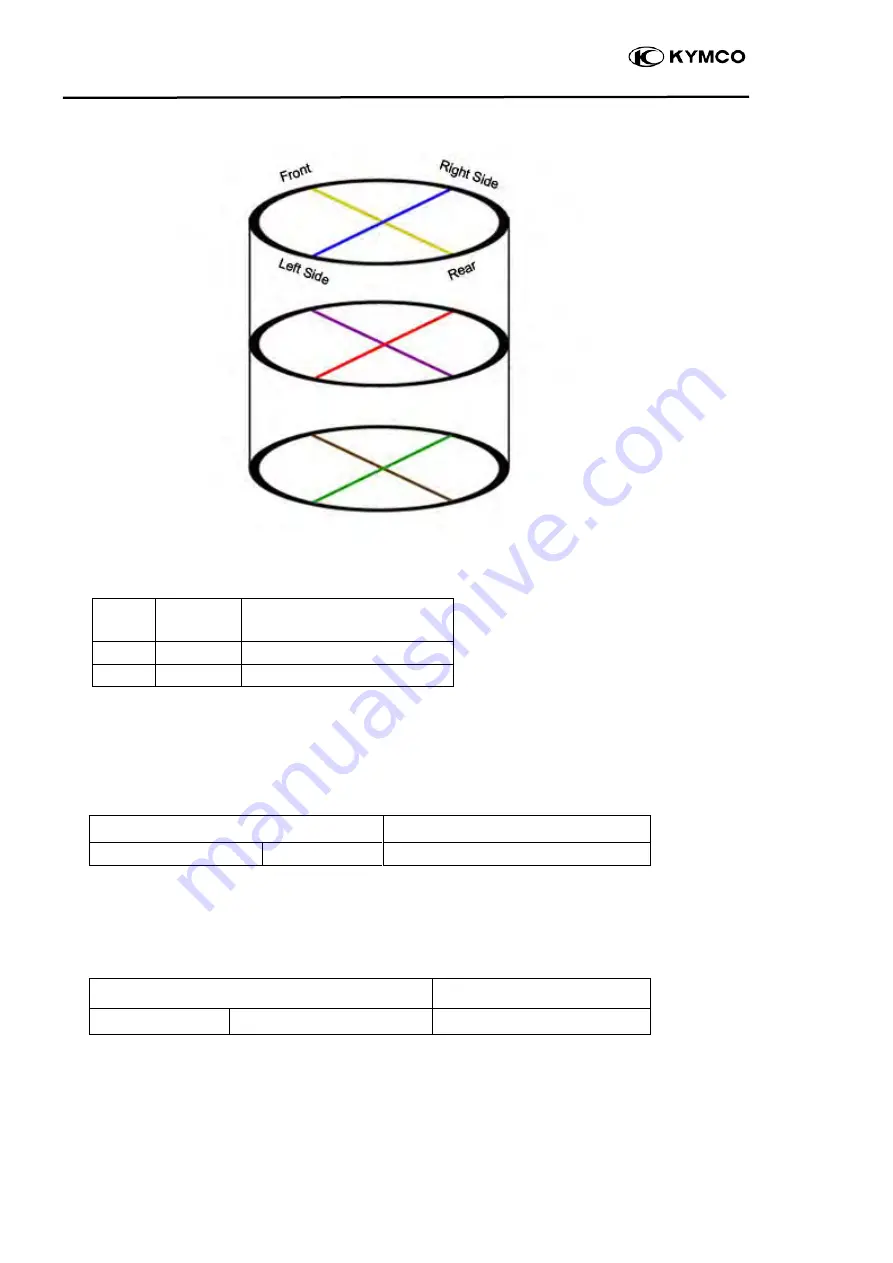
XCITING 400i
3. Engine > Cylinders and Pistons
Inspect the cylinder front to back and side to side at three different
height levels with a dial bore gauge.
No.
Mark
Cylinder I.D. (mm)
1
A
84.00 – 84.01
2
B
84.01 – 84.02
Calculate the cylinder taper. The taper is the maximum difference
between either yellow and brown or blue and green.
Item
Limit (mm)
Cylinder
Taper
0.05
Calculate the cylinder out of round. The out of round is greatest out of
yellow, purple, or brown minus the smallest of blue, red, or green.
Item
Limit (mm)
Cylinder
Out of round
0.05
3‐52
Summary of Contents for ADG5
Page 12: ...1 Quick Reference XCITING S 400 1 12 Torque Engine Specifications...
Page 13: ...1 Quick Reference XCITING S 400 1 13 Torque Frame Specifications...
Page 16: ...1 Quick Reference XCITING S 400 1 16 General Troubleshooting...
Page 17: ...1 Quick Reference XCITING S 400 1 17...
Page 18: ...1 Quick Reference XCITING S 400 1 18...
Page 19: ...1 Quick Reference XCITING S 400 1 19...
Page 20: ...1 Quick Reference XCITING S 400 1 20 VIN and Engine Number Location...
Page 23: ...2 Periodic Maintenance XCITING S 400 9 3...
Page 114: ...3 Engine Valves XCITING 400i Remove the spring retainer Remove the valve springs 3 36...
Page 329: ...9 Electrical Systems XCITING S 400 9 29 Check the circuit with the wire...
Page 340: ...10 Brake System XCITING S 400 Diagram 10 3...
Page 362: ...10 Brake System XCITING S 400 Pre diagnosis Inspection Chart 1 10 25...
Page 363: ...10 Brake System XCITING S 400 Pre diagnosis Inspection Chart 2 10 26...