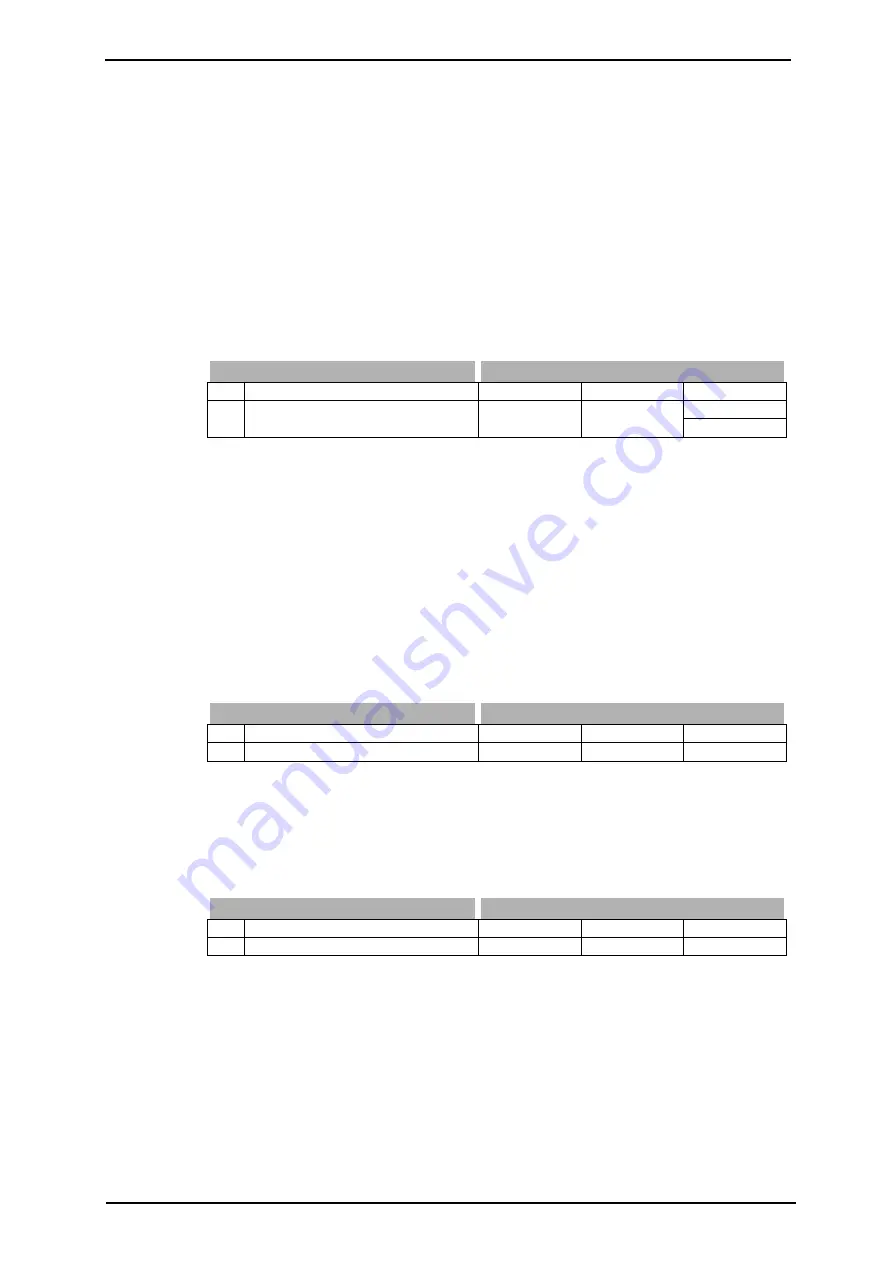
KFU 2-/4-
213
17 Special
Functions
The configurable functions of the corresponding control methods enable another field
of application of the frequency inverters. The integration in the application is made
easier by special functions.
17.1
Pulse Width Modulation
The motor noises can be reduced by changing over the parameter
Switching fre-
quency
400
. A reduction of the switching frequency should be up to a maximum ratio
of 1:10 to the frequency of the output signal for a sine-shaped output signal. The
maximum possible switching frequency depends on the drive output and the ambient
conditions. For the required technical data refer to the corresponding table and the
device type diagrams.
Parameter
Settings
No.
Description
Min.
Max.
Fact. sett.
2 kHz
1)
400 Switching frequency
2 kHz
16 kHz
4 kHz
2)
The factory setting of parameter
Switching frequency
400
depends on the setting of parame-
ter
Configuration
30
:
1)
configurations 1xx
2)
configurations 2xx / 4xx/ 5xx
The heat losses increase proportionally to the load point of the frequency inverter and
the switching frequency. The automatic reduction adjusts the switching frequency to
the current operating state of the frequency inverter in order to provide the output
performance required for the drive task at the greatest possible dynamics and a low
noise level.
The switching frequency is adapted between the limits which can be set with the pa-
rameters
Switching frequency
400
and
Min. switching frequency
401
. If the
Min.
switching frequency
401
is larger than or equal to the
Switching frequency
400
, the
automatic reduction is deactivated.
Parameter
Settings
No.
Description
Min.
Max.
Fact. sett.
401 Min. switching frequency
2 kHz
16 kHz
2 kHz
The change of the switching frequency depends on the heat sink temperature switch-
off limit and the output current. The temperature limit to be exceeded so that the
switching frequency is reduced can be set via parameter
Reduction limit heat sink
temp.
580
. If the heat sink temperature falls below the threshold set via parameter
Reduction limit heat sink temp.
Ti/Tk
580
by 5 °C, the switching frequency is in-
creased again step by step.
Parameter
Settings
No.
Description
Min.
Max.
Fact. sett.
580 Reduction limit Ti/Tk
-25 °C
0 °C
-4 °C
Note:
The limit for the switching frequency reduction is influenced by the in-
telligent current limits depending on the selected
Operation mode
573
and the output current. If they have been switched off or provide the
full overload current, the switching frequency is reduced when the
output current exceeds the limit of 87.5% of the long-term overload
current (60s). The switching frequency is increased if the output cur-
rent drops below the reference current of the next highest switching
frequency.