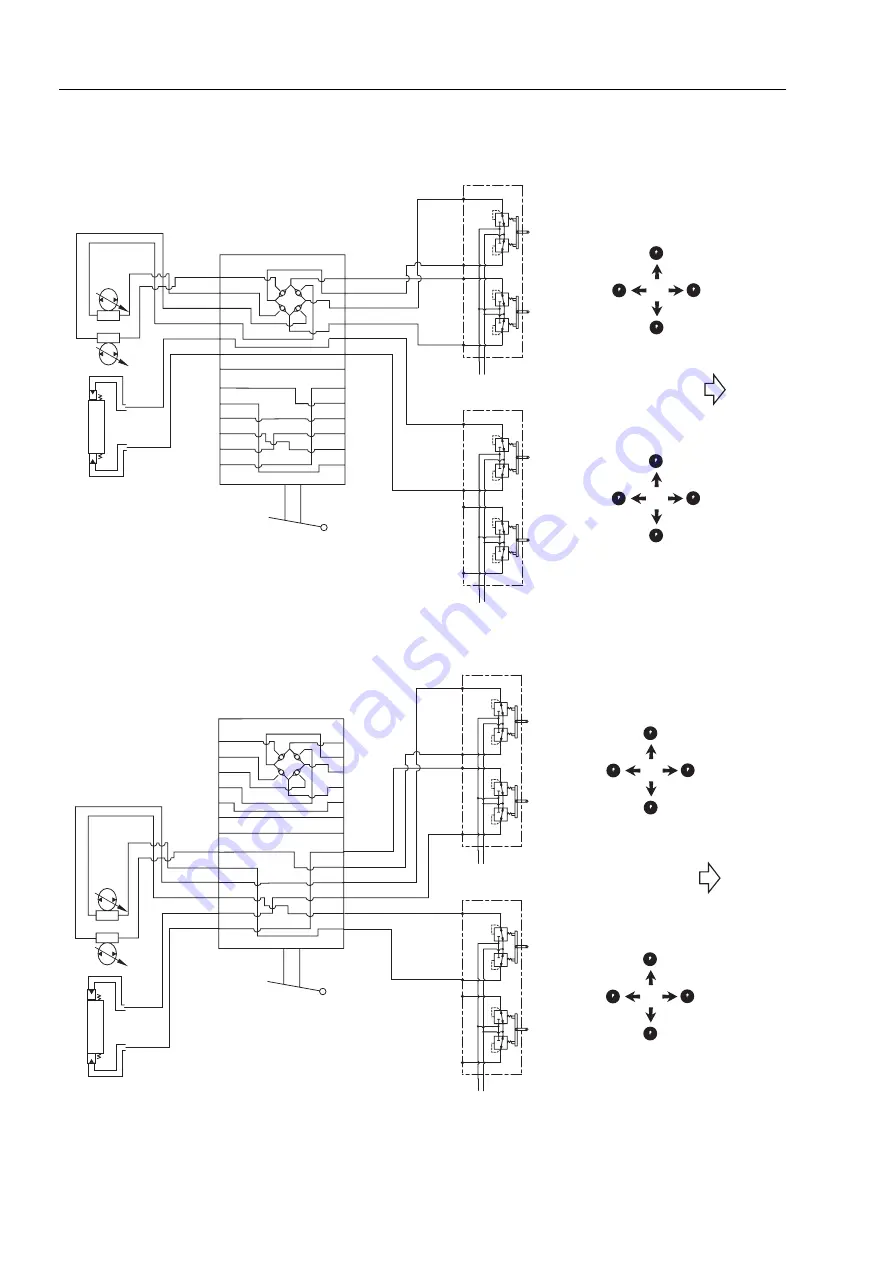
10-56
SK714-5 SK815-5 SK815-5 turbo
OPERATION
PATTERN ISO
PATTERN OPTIONAL
RKS00921
ARM
DOWN
ARM
RAISE
FRONT
BUCHET
CURL
BUCKET
DUMP
FORWARD
LEFT
STEERING
REVERSE
RIGHT
STEERING
P
P2
P3
P4
P1
P
P2
P3
P4
P1
T
T
B1
A1
B2
A2
PA1
PB1
P out 4
P out 6
P out 3
P out 2
P out 1
P out 5
P in 4
P in 6
P in 3
P in 2
P in 1
P in 5
RKS00931
L.H. FORWARD
ARM
DOWN
L.H. REVERSE
R.H. FORWARD
ARM
RAISE
R.H. REVERSE
FRONT
BUCKET
DUMP
BUCKET
CURL
P
P2
P3
P4
P1
P
P2
P3
P4
P1
T
T
B1
A1
B2
A2
PA1
PB1
P out 4
P out 6
P out 3
P out 2
P out 1
P out 5
P in 4
P in 6
P in 3
P in 2
P in 1
P in 5
STRUCTURE AND FUNCTION
PATTERN CHANGE VALVE (OPTIONAL)
Summary of Contents for SK714-5
Page 1: ...WEBM005500 ...
Page 2: ......
Page 3: ...SK714 5 SK815 5 SK815 5 turbo WEBM005500 00 1 ...
Page 18: ...PAGE INTENTIONALLY LEFT BLANK ...
Page 38: ...PAGE INTENTIONALLY LEFT BLANK ...
Page 83: ...PAGE INTENTIONALLY LEFT BLANK ...
Page 104: ...PAGE INTENTIONALLY LEFT BLANK ...
Page 108: ...PAGE INTENTIONALLY LEFT BLANK ...
Page 112: ...PAGE INTENTIONALLY LEFT BLANK ...
Page 118: ...PAGE INTENTIONALLY LEFT BLANK ...
Page 126: ...PAGE INTENTIONALLY LEFT BLANK ...
Page 172: ......
Page 174: ...PAGE INTENTIONALLY LEFT BLANK ...
Page 253: ...PAGE INTENTIONALLY LEFT BLANK ...
Page 256: ......
Page 257: ......
Page 258: ...2003 ...