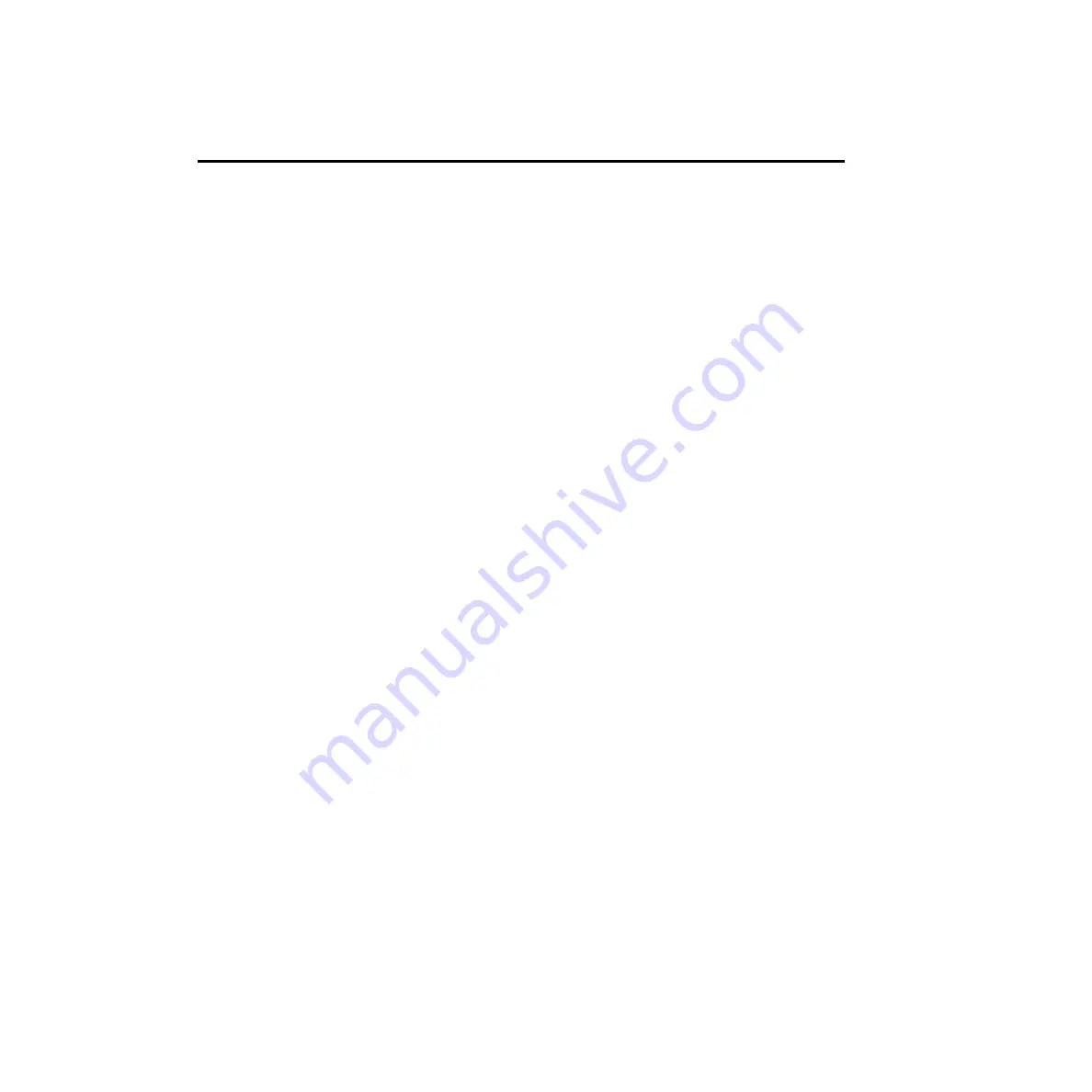
TEC control setpoints
Tolerance
TEC temperature
Control methods
Temperature
Configuration
Menus
Protection limits
Readings
Temperature control methods
On-off
Proportional (P)
Proportional-integral-derivative
Temperature control model
Terminator
Tests
Front panel
Thermistor coefficients
Thermistor sensor ranges
Initiate control/measure cycle
Trigger subsystem commands
U
V
Voltage
Configuration
Readings
W
Warranty
Warranty information
Summary of Contents for TEC SourceMeter 2510
Page 194: ...A Specifications...
Page 197: ...B StatusandErrorMessages...
Page 206: ...C IEEE 488BusOverview...
Page 221: ...D IEEE 488andSCPI ConformanceInformation...
Page 225: ...E ExamplePrograms...
Page 233: ...F GPIB488 1Protocol...