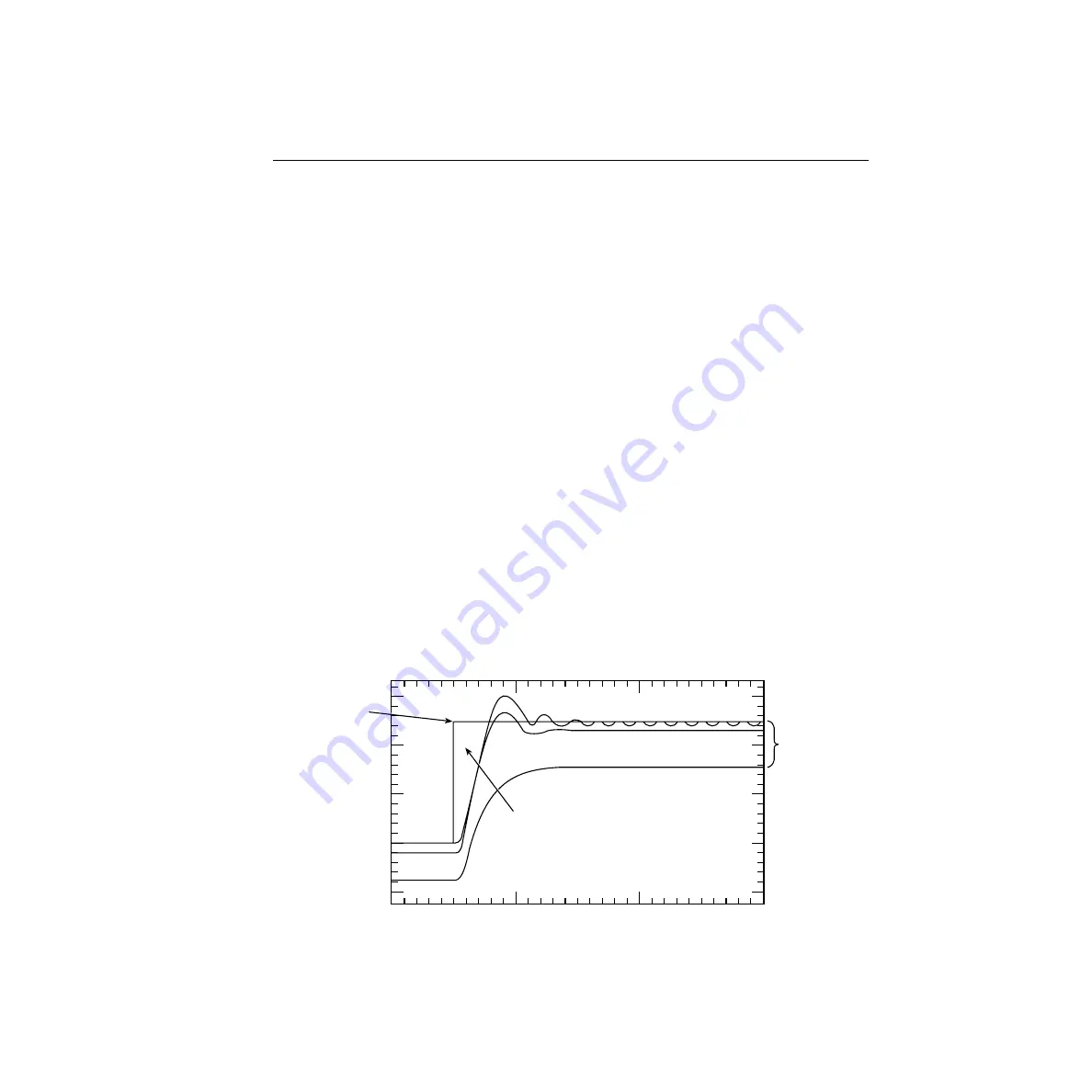
Models 2510 and 2510-AT User’s Manual
PID Control Concepts
4-3
On-off control
The on-off control method, used by many conventional thermostats, is inadequate for ther-
moelectric cooler (TEC) control situations. When the TEC is warmer than the setpoint
temperature, the TEC power is turned on to maximum. Once the TEC is cooler than the
setpoint temperature, the TEC power is turned off completely. The turn-on and turn-off
temperatures usually differ by a small amount to minimize the amount of temperature
cycling, resulting in a certain amount of hysteresis. However, temperature fluctuations are
generally too large for precise TEC temperature control due in large part to the thermal
time constant of the TEC and the hysteresis required to limit excessive temperature
cycling.
Proportional (P) control
A proportional controller usually performs better than the on-off type discussed above by
applying power, W, to the cooler in proportion to the difference in temperature between
the cooler and setpoint temperatures as follows:
W = K
p
×
(T
c
– T
s
)
Here, K
p
is the proportional gain of the controller.
As its gain is increased, the system responds faster to changes in setpoint, but it becomes
progressively underdamped and eventually unstable, as shown in
. The final
cooler temperature lies above the setpoint with this method because some temperature dif-
ference is required to maintain power to the cooler.
To use the Model 2510 as a P controller, set the derivative and integral constants to zero.
Figure 4-2
Proportional control characteristics
80
70
60
50
40
50
100
150
Time (s)
Temperature
(
°
C)
Cooler
Temperature
Increasing Gain
Setpoint
0
Summary of Contents for TEC SourceMeter 2510
Page 194: ...A Specifications...
Page 197: ...B StatusandErrorMessages...
Page 206: ...C IEEE 488BusOverview...
Page 221: ...D IEEE 488andSCPI ConformanceInformation...
Page 225: ...E ExamplePrograms...
Page 233: ...F GPIB488 1Protocol...