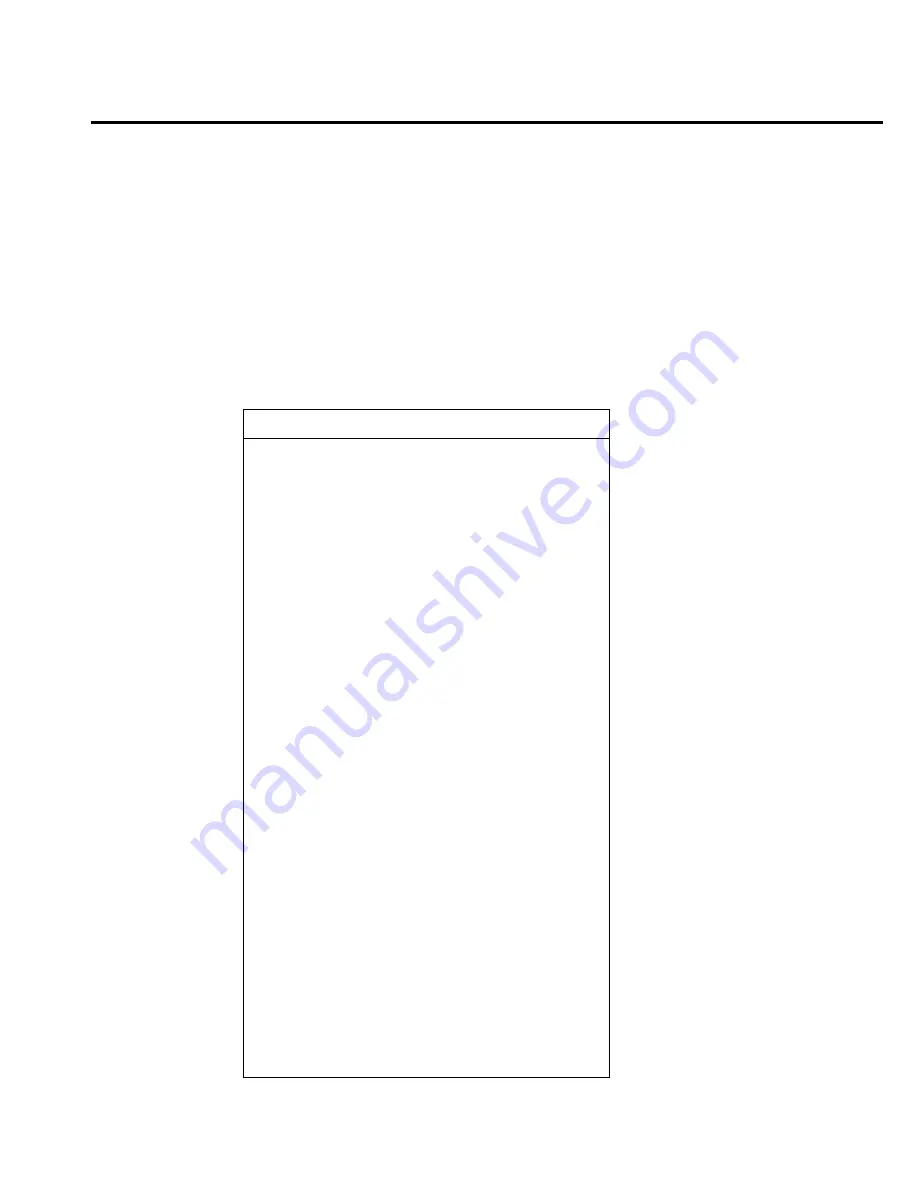
Calibration Reference
B-21
Remote error reporting
Methods to detect and determine the nature of calibration errors are discussed in the follow-
ing paragraphs.
Error summary
Table B-5
summarizes Model 2700 calibration errors.
Table B-5
Calibration error summary
Error number and description
+400, "10 vdc zero error"
+401, "100 vdc zero error"
+402, "10 vdc full scale error"
+403, "-10 vdc full scale error"
+404, "100 vdc full scale error"
+405, "-100 vdc full scale error"
+406, "1k 2-w zero error"
+407, "10k 2-w zero error"
+408, "100k 2-w zero error"
+409, "10M 2-w zero error "
+410, "10M 2-w full scale error"
+411, "10M 2-w open error"
+412, "1k 4-w zero error"
+413, "10k 4-w zero error"
+414, "100k 4-w zero error"
+415, "10M 4-w sense lo zero error"
+416, "1k 4-w full scale error"
+417, "10k 4-w full scale error"
+418, "100k 4-w full scale error"
+419, "1M 4-w full scale error"
+420, "10M 4-w full scale error"
+421, "10m adc zero error"
+422, "100m adc zero error"
+423, "10m adc full scale error"
+424, "100m adc full scale error"
+425, "1 adc full scale error"
+438, "Date of calibration not set"
+439, "Next date of calibration not set"
+450, "100m vac dac error"
Summary of Contents for 2700
Page 1: ...Contains Servicing Information Model 2700 Multimeter DataAcquisition System Service Manual...
Page 16: ......
Page 17: ...1 PerformanceVeri cation...
Page 48: ...1 32 Performance Verification...
Page 49: ...2 Calibration...
Page 72: ...2 24 Calibration...
Page 73: ...3 RoutineMaintenance...
Page 81: ...4 Troubleshooting...
Page 99: ...5 Disassembly...
Page 106: ...5 8 Disassembly...
Page 107: ...6 ReplaceableParts...
Page 121: ...A Speci cations...
Page 136: ...A 16 Specifications...
Page 137: ...B CalibrationReference...
Page 161: ...C CalibrationProgram Appendix C Page 1 Friday February 18 2000 7 45 AM...
Page 172: ...Service fm Page 2 Friday February 18 2000 7 44 AM...
Page 173: ......
Page 174: ...Keithley Instruments Inc 28775 Aurora Road Cleveland Ohio 44139 Printed in the U S A...