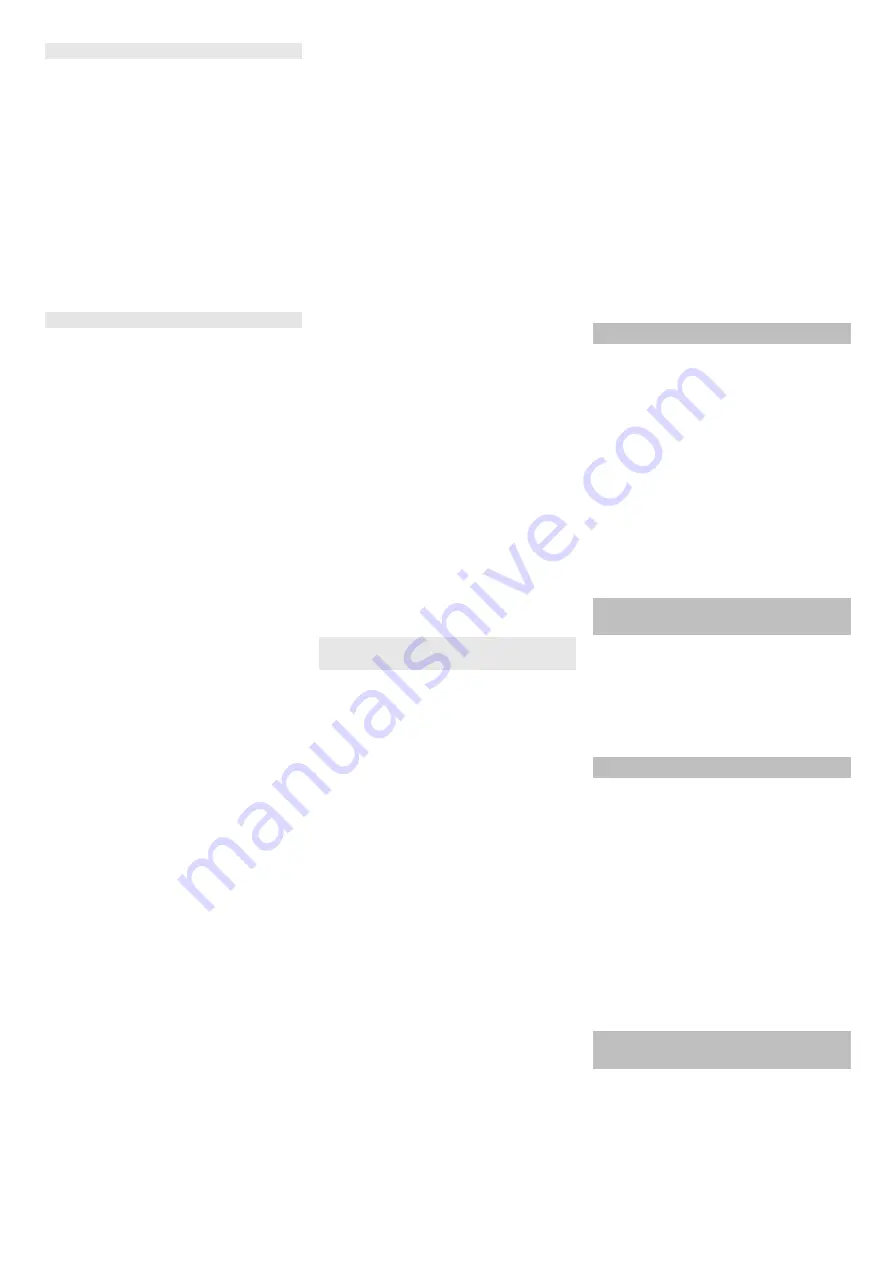
-
3
– Propellant-operated units are to be
checked at regular intervals, at least
once a year, by an expert against leaks
(according to BGG 936) and ensure
that the unit is functioning properly.
– The inspection must be certified and
documented. The inspection guidelines
are § 33 and § 37 UVV (occupation ac-
cident prevention regulations) "Use of
liquid gas" (BGV D34).
– General applicable regulations are the
guidelines for inspecting vehicles
whose engines are driven by liquefied
gases of the Federal Transportation
Minister.
– Gas must always be drawn only from
one cylinder. Drawing gas from multiple
cylinders simultaneously can cause liq-
uid gas from one cylinder flowing into
the other. This causes the over-filled
cylinder to be subjected to an unpermit-
ted excess pressure when the cylinder
valve is closed later (refer B.1 of these
guidelines).
– Note the installation position of the gas
connection during installation of the full
bottle, further information in chapter “In-
stalling the gas bottle”.
Perform the replacement of the gas cylin-
der carefully. During assembly and disas-
sembly, the gas outlet nozzle of the cylin-
der valve must be sealed by means of a
cap nut that is tightened using a wrench.
– Discontinue the use of leaky gas cylin-
ders. Such cylinders are to be emptied
by slowly letting out the gas in open
spaces by conforming to all safety reg-
ulations and are to be indicated as
leaky. Also inform the issuing company
or its representative (the filling-station
attendant) in writing about the damage
to the cylinder while delivering or re-
ceiving the cylinders.
– Before connecting the gas cylinder,
check that its connection neck is in a
proper state.
– After connecting the cylinder, regularly
check that it is not leaky by using a
foaming agent.
– Open the valves slowly. Do not use
hammers to open and close the cylin-
ders.
– Fight liquid-gas fires only from a safe
distance and with protection.
- use only dry powder carbon dioxide
extinguishers or carbon dioxide gas ex-
tinguishers.
- use abundant water to cool the gas
tank.
– The entire LPG unit must be continu-
ously checked to ensure that there are
no leaks and the unit is functioning
properly. Using the vehicle with a leaky
gas unit is strictly prohibited.
– First close the cylinder valve before
loosening the pipe or tube connection.
Unscrew and loosen the connection nut
of the gas cylinder slowly because oth-
erwise the gas under pressure in the
tube will flow out instantly.
– If the gas is refilled from a larger tank,
then ask the sales agent of the LPG
about the important regulations to be
followed.
Danger
Risk of injury!
–
LPG in a liquid state can cause frost
bites on bare skin.
–
After disconnecting the cylinder, tighten
the closing nut firmly on the connecting
threading of the cylinder.
–
Use soap water or some such foaming
agent to check whether the cylinder is
leaking. The use of open flames to illu-
minate the LPG unit is strictly prohibit-
ed.
–
Follow the manufacturer's installation
specifications while changing individual
parts of the LPG unit. Close all cylinder
and locking valves while doing so.
–
Regularly check the status of the elec-
trical unit of the LPG vehicles . Sparks
can cause explosions if the gas-carry-
ing parts of the unit are leaky.
–
If a LPG-driven vehicle has been idling
for a long time, then first ventilate the
setting room before commissioning the
vehicle or its electrical unit.
–
Immediately inform the trade associa-
tion and the concerned trade superviso-
ry authority about accidents with gas
cylinders or LPG units. Store the dam-
aged parts carefully until all investiga-
tions have been completed.
– Propellants or LPG cylinders must al-
ways be stored according to the regula-
tions of TRF 1996 (Technical Regula-
tions for Liquid Gases, refer DA to BGV
D34, Appendix 4).
– Always store the gas cylinders in a ver-
tical position. Use of open flames and
smoking at the installation site of the
cylinders and during repairs is strictly
prohibited. Protect the stored cylinders
against unauthorised access. Close all
empty cylinders properly.
– Close the cylinder and main locking
valves immediately when you switch off
the vehicle.
– Follow the regulations for garages and
the construction guidelines of the re-
spective State about the location and
structure of the parking areas for LPG-
driven vehicles.
– Gas cylinders are to be stored in sepa-
rate rooms away from the parking areas
(refer DA to BGV D34, Appendix 2).
– The electrical hand-held lamps used in
the rooms are to be equipped with
closed, sealed case and a strong pro-
tection cover.
– Close all cylinder and main valves be-
fore working in repair workshops and
protect the gas cylinders against effect
of external heat.
– A responsible person must check that
all valves, especially the cylinder
valves, are closed during operational
breaks and before closing the factory.
Do not carry out any jobs involving fire -
such as cutting and welding jobs - in the
vicinity of the gas cylinders. Do not
store gas cylinders, not even empty
ones, in the workshops.
– The parking and storage rooms and the
repair workshops must be ventilated
properly. Please note that liquefied gas-
es are heavier than atmospheric air.
They get collected on the floor, in re-
cesses and other holes in the floors and
form a gas-air mixture that can lead to
explosions.
Do not use the device at elevations of
over 1200 m.
Danger
Risk of injury!
Do not close the exhaust.
Do not bend over the exhaust or touch
it (risk of burns).
Do not touch the drive motor (risk of
burns).
Exhaust gases are poisonous and haz-
ardous to health, do not inhale them.
The engine requires approx. 3-4 sec-
onds to come to a standstill once it has
been switched off. During this time, stay
well clear of the working area.
DANGER
Risk of injury!
When working on the high emptying
system, completely lift and secure the
waste container.
Perform the safeguarding only from
outside the hazard zone.
NOTICE
The overhead guard (optional) protects the
driver against larger falling objects. Howev-
er, it does not provide rollover protection!
Check the overhead guard for damage
daily.
If the overhead guard, as well as indi-
vidual elements, should be damaged,
replace the entire overhead guard.
Any modification of the overhead guard
and installation of elements, compo-
nents and assemblies other than those
approved by Kärcher is not permitted
and may limit the function of the over-
head guard.
Observe the net weight (transport
weight) of the device during transport
on trailers or vehicles.
Disconnect the battery and securely
fasten the device for transport.
Maintenance by expert
Commissioning/Operations
In the installation and storage rooms as
well as the workshops
Appliances with combustion engine
Appliances with high emptying
system
Devices with overhead guard
Safety information concerning the
transport of the appliance
21
EN
Summary of Contents for KM 120/250 R LPG
Page 2: ...2...
Page 182: ...2 PVC 0 C K rcher 18 10 HVBG 18 182 EL...
Page 184: ...4 1200 m 3 4 K rcher 70mm 2 2 851 kg 184 EL...
Page 186: ...6 1 2 3 1 2 3 4 5 6 7 8 9 10 10 km h 1 2 1 2 3 11kg 1 2 3 1 2 3 30 mm 186 EL...
Page 187: ...7 30 mm 3 1 2 11 10 1 3 13 10 10 1 2 3 M 70 mm 70 mm 1 2 3 4 1 1 187 EL...
Page 188: ...8 2 2 3 3 4 4 1 3 4 1 3 1 3 4 1 3 1 3 4 2 4 4 2 1 3 4 0 0 4x 0 30 mm 188 EL...
Page 189: ...9 VDE 0701 0 K rcher K rcher 50 250 500 1000 1500 2000 0 1 2 189 EL...
Page 190: ...10 1 2 3 20 C 1 28 kg l 1 00 1 28 kg l 1 2 3 Min Max DOT 5 190 EL...
Page 191: ...11 1 2 MIN MAX MIN MAX 5 6 1 2 25 Nm 10 1 2 3 4 MIN MAX MIN K rcher 1 MIN MAX 20 191 EL...
Page 192: ...12 1 2 1 2 3 80 mm 1 3 10 1 3 80 85 mm 12 10 40 50 mm 1 2 192 EL...
Page 215: ...2 7 0 C K rcher 18 215 RU...
Page 216: ...3 18 10 HVBG DIN 51622 90 10 30 70 0 C 32 F BGG 936 33 37 UVV BGV D34 1 216 RU...
Page 217: ...4 Nekal TRF 1996 DA BGV D34 4 Stellplatzverordnung DA BGV D34 2 1200 3 4 K rcher 217 RU...
Page 218: ...5 70 2 2 851 218 RU...
Page 219: ...6 1 2 3 4 5 6 7 8 9 10 11 12 13 14 15 16 17 18 19 1 2 3 4 5 6 7 8 9 0 1 2 10 11 12 13 219 RU...
Page 220: ...7 1 2 3 1 2 3 4 5 6 7 8 9 10 10 1 2 1 2 3 11 1 2 3 1 2 3 30 220 RU...
Page 221: ...8 30 3 1 2 11 1 3 10 13 10 10 1 2 3 70 70 221 RU...
Page 222: ...9 1 2 3 4 1 1 2 2 3 3 4 4 1 3 4 1 3 1 3 4 1 3 1 3 4 2 4 4 2 1 3 4 0 222 RU...
Page 223: ...10 0 4 0 30 VDE 0701 0 K rcher K rcher 50 250 500 1000 1500 2000 0 223 RU...
Page 224: ...11 1 2 1 2 3 1 28 20 C 1 00 1 28 224 RU...
Page 226: ...13 Karcher 1 MIN MAX 20 1 2 1 2 3 80 1 3 10 1 3 80 85 12 226 RU...
Page 227: ...14 10 40 50 1 2 6 3 SW 13 1 3 1 2 3 1 2x 2 1 2 K rcher 10 7 9 1 2 2 1 227 RU...
Page 361: ...2 e PVC 0 C K rcher 18 18 361 BG...
Page 363: ...4 DA BGV D34 2 1200 m 3 4 K rcher 70 2 2 851 kg 363 BG...
Page 364: ...5 1 2 3 4 5 6 7 8 9 10 11 12 13 14 15 16 17 18 19 1 2 3 4 5 6 7 8 9 0 1 2 10 11 12 13 1 364 BG...
Page 365: ...6 2 3 1 2 3 4 5 6 7 8 9 10 10 1 2 1 2 3 11 1 2 3 1 2 3 30 365 BG...
Page 366: ...7 30 3 1 2 11 10 1 3 13 10 10 1 2 3 70 70 366 BG...
Page 367: ...8 1 2 3 4 1 1 2 2 3 3 4 4 1 3 4 1 3 1 3 4 1 3 1 3 4 2 4 4 2 1 3 4 0 367 BG...
Page 368: ...9 0 4 0 30 2 VDE 0701 0 K rcher Karcher 50 250 500 1000 1500 2000 0 368 BG...
Page 369: ...10 1 2 1 2 3 20 C 1 28 1 00 1 28 369 BG...
Page 370: ...11 1 2 3 Min Max DOT 5 1 2 MA 5 6 1 2 25 Nm 10 1 2 3 4 370 BG...
Page 371: ...12 K rcher 1 MIN MAX 20 1 2 1 2 3 80 1 3 10 1 3 80 85 12 371 BG...
Page 372: ...13 10 40 50 1 2 6 3 SW 13 1 3 1 2 3 1 2x 2 1 2 K rcher 10 7 9 K rcher 2 1 372 BG...
Page 426: ...2 0 C K rcher 18 10 18 426 UK...
Page 428: ...4 1200 3 4 K rcher 70 2 2 851 428 UK...
Page 429: ...5 1 2 3 4 5 6 7 8 9 10 11 12 13 14 15 16 17 18 19 1 2 3 4 5 6 7 8 9 0 1 2 10 11 12 13 429 UK...
Page 430: ...6 1 2 3 1 2 3 4 5 6 7 8 9 10 10 1 2 1 2 3 11 1 2 3 1 2 3 30 30 430 UK...
Page 431: ...7 3 1 2 11 10 1 3 13 10 10 1 2 3 50 70 1 2 3 4 1 1 431 UK...
Page 432: ...8 2 2 3 3 4 4 1 3 4 1 3 1 3 4 1 3 1 3 4 2 4 4 2 1 3 4 0 0 4 0 30 432 UK...
Page 433: ...9 VDE 0701 0 K rcher K rcher 50 250 500 1000 1500 2000 0 1 2 433 UK...
Page 434: ...10 1 2 3 1 28 20 C 1 00 1 28 1 2 3 434 UK...
Page 435: ...11 MIN MAX DOT 5 1 2 M N MAX M N MAX 5 6 1 2 25 Nm 10 1 2 3 4 M N MAX M N 1 MIN MAX 20 435 UK...
Page 436: ...12 1 2 1 2 3 80 1 3 10 1 3 80 85 12 10 40 50 436 UK...
Page 437: ...13 1 2 6 3 SW 13 1 3 1 2 3 1 2x 2 1 2 K rcher 10 7 9 1 2 1 2 1 2 FU 01 2 1 437 UK...
Page 443: ...2 PVC 0 C K rcher 18 10 HVBG DIN 51622 A B 90 10 30 70 0 C 32 F BGG 936 33 37 BGV D34 1 443 ZH...
Page 444: ...3 TRF 1996 BGV D34 4 DA BGV D34 2 DA 1200 3 4 K rcher 70mm 2 2 851 kg 444 ZH...
Page 446: ...5 8 9 10 10km h 1 2 1 2 3 11 kg 1 2 3 1 2 3 30 mm 30 mm 3 1 2 11 446 ZH...
Page 448: ...7 4x 0 30 mm 2 VDE 0701 0 K rcher K rcher 50 250 500 1000 1500 2000 0 1 2 448 ZH...
Page 449: ...8 1 2 3 20 C 1 28kg l 1 00 1 28kg l 1 2 3 DOT 5 1 2 MAX MIN MIN MAX 5 6 1 2 25 Nm 10 449 ZH...
Page 450: ...9 1 2 3 4 MAX MIN MIN K rcher 1 20 1 2 1 2 3 80 mm 1 3 10 1 3 80 85 mm 12 10 40 50mm 450 ZH...
Page 458: ...13 458 AR...
Page 460: ...11 1 2 SW 13 1 3 1 2 3 1 2x 2 1 2 K rcher 7 9 10 1 2 1 2 1 2 2 1 460 AR...
Page 461: ...10 1 MIN MAX 20 1 2 1 2 3 80 1 3 10 3 80 85 12 10 40 50 461 AR...
Page 462: ...9 1 2 3 DOT 1 2 MIN MAX MIN MAX 6 1 2 25 10 1 2 3 4 MIN MAX MIN 462 AR...
Page 463: ...8 50 250 500 1000 1500 2000 0 1 2 1 2 3 20 1 28 1 1 28 463 AR...
Page 464: ...7 1 3 4 1 3 1 3 4 2 4 4 2 1 3 4 0 0 4X 0 30 VDE 0701 0 464 AR...
Page 465: ...6 1 2 11 10 1 3 13 10 10 1 2 3 70 70 1 2 3 4 1 1 2 2 3 3 4 4 1 3 4 1 3 465 AR...
Page 466: ...5 6 7 8 9 10 10 1 2 1 2 3 11 1 2 3 1 2 3 30 30 3 466 AR...
Page 468: ...3 Nekal TRF 1996 D34 4 D34 2 1200 3 4 K rcher 70 2 851 468 AR...
Page 469: ...2 0 K rcher 18 10 A B DIN 51622 90 10 30 70 0 32 936 33 37 D34 1 469 AR...
Page 471: ......