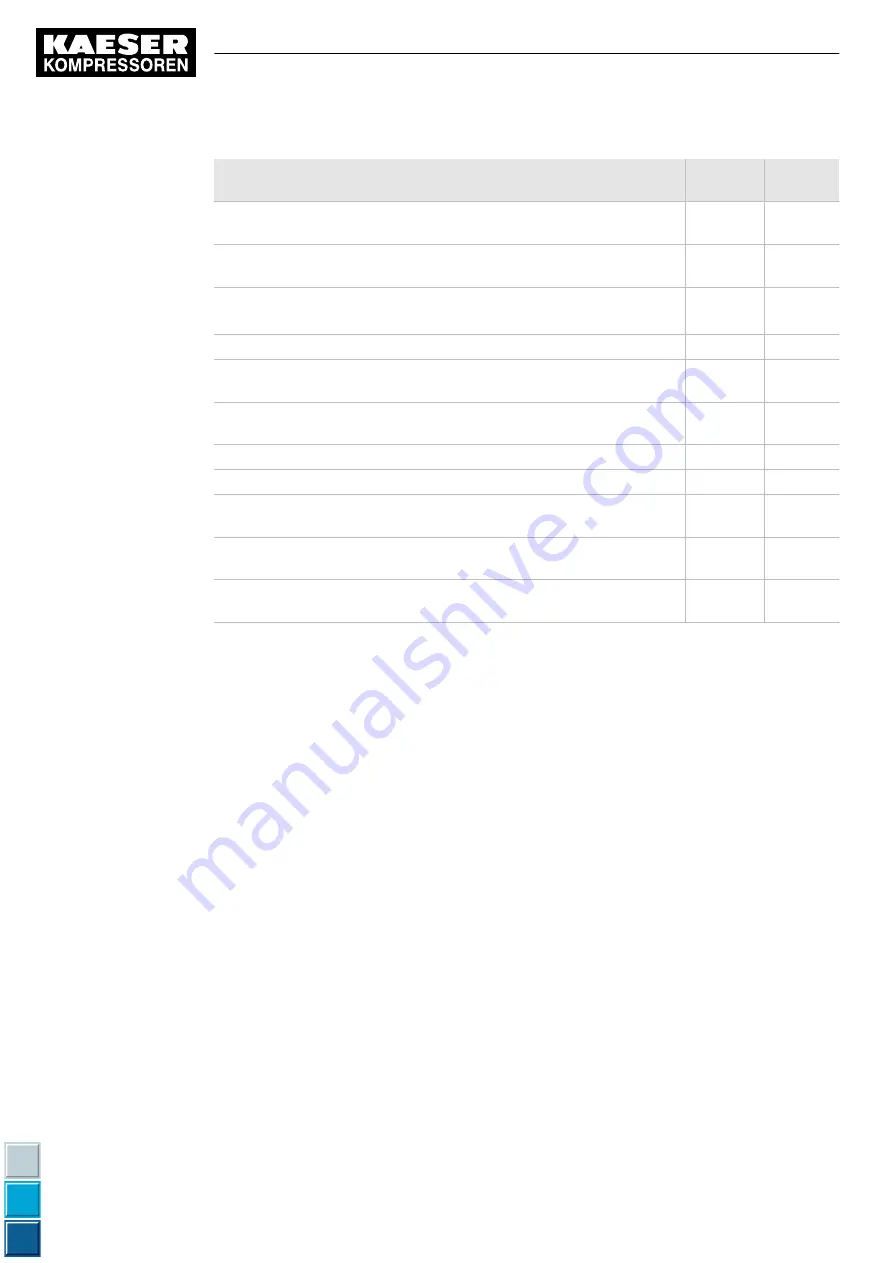
To be checked
See
chapter
Complied?
➤ Are the power supply cable conductor cross-sections and fuse ratings
adequate?
➤ Fan motor overload protection switch set according to the mains volt‐
age?
➤ Have all electrical connections been checked for tightness?
➤ Has the check been repeated after 50 operating hours?
–
➤ Is a shut-off valve fitted to gas outlet?
➤ Is the connection the gas network made with a flexible pressure line
or axial compensator?
➤ Sufficient cooling oil in the separator tank?
(oil level indicator outside the red zone)
➤ Is there sufficient cooling oil in the machine?
➤ Is there sufficient cooling oil in the airend?
➤ Is the machine firmly anchored to the floor?
(option H1)
➤ Supply of cooling water ensured?
(Option K2/K9)
➤ Are all access doors closed and latched and all removable panels in
place and secured?
–
Tab. 32 Installation conditions checklist
7.4 Commissioning the Frequency Converter
The frequency converter parameters are preset. Adjustment of parameters to suit operating condi‐
tions on site is done by trained and authorised personnel.
Changes to the factory settings may influence the whole machine. The machine may break down
or be damaged.
➤ Allow only trained and authorised personnel to make parameter changes.
7.5 Filling with cooling oil
The machine must be charged with cooling oil prior to commissioning, see chapter 10.15.
For the required cooling oil charge volume please see chapter 2.10.
7.6 Filling cooling oil into the airend
Before starting the compressor for the very first time and before re-starting after a shutdown period
of more than 3 months it is necessary to manually add a quantity of cooling oil into the airend. In
order to avoid that the cooling oil exceeds the permissible level, drain the required quantity from
the de-pressurised oil separator tank.
Chapter 10.16 provides detailed information on how to drain cooling oil from the oil separator tank.
7
Initial Start-up
7.4
Commissioning the Frequency Converter
44
Service Manual Screw Compressor
ESD 442/14 bar (abs) SFC SIGMA CONTROL 2
ESD_2C_10357405_10–LIN_00 E
Summary of Contents for ESD 352 SFC
Page 5: ......
Page 6: ......
Page 7: ......
Page 8: ......
Page 9: ......
Page 10: ......
Page 11: ......
Page 12: ......
Page 13: ......
Page 14: ......
Page 15: ......
Page 16: ......
Page 17: ......
Page 18: ......
Page 19: ......
Page 20: ......
Page 21: ......
Page 22: ......
Page 23: ......
Page 24: ......
Page 25: ......
Page 26: ......
Page 27: ......
Page 28: ......
Page 29: ......
Page 30: ......
Page 31: ......
Page 32: ......
Page 33: ......
Page 34: ......
Page 35: ......
Page 171: ...KKW SSC 2 03 en 01 BA SIGMA CONTROL FLUID KKW SSC 2 03 01 20130805 113302...
Page 173: ......
Page 175: ...Contents ii Quick user guide Controller SIGMA CONTROL 2 SCREW FLUID 1 1 3 9_9450 03 USE...
Page 215: ...Contents iv Service manual Controller SIGMA CONTROL 2 SCREW FLUID 1 1 3 9_9450 03USE...
Page 392: ...KKW GBASE 1 00 en ERSATZTEILE 10357405_10 ESD 2C 20130903 115349...