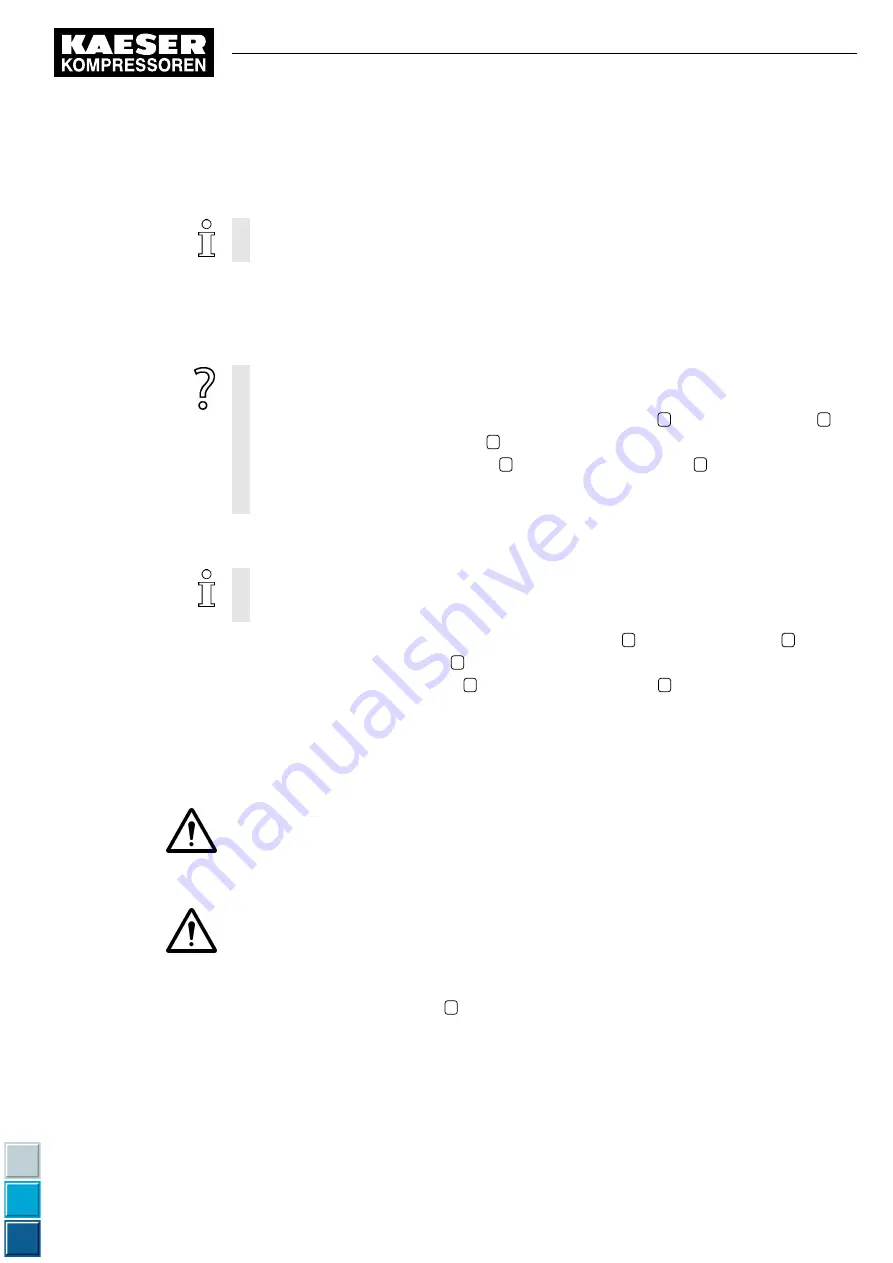
Isolate the compressor from the gas system.
➤ Close the user's shut-off valve at the inlet and outlet ends.
If no shut-off valve is provided, the complete gas network must be vented.
Vent the oil separator tank.
The oil circulation vents automatically as soon as the machine is stopped.
➤ Check that the oil separator tank pressure gauge reads 0 bar.
After automatic venting the pressure gauge does not read 0 bar?
➤ Make sure that the shut-off valve is closed or that the complete gas network is vented.
➤ With the shut-off valve closed, insert the male hose fitting
6
into the hose coupling
3
.
➤ Slowly open the shut-off valve
7
to release pressure.
➤ Disconnect the male hose fitting
6
and close the shut-off valve
7
.
➤ If manual venting does not bring the oil separator tank pressure gauge to zero: Contact
the KAESER Service.
Vent gas manually from the gas cooler.
After shutting down the compressor and venting the oil separator tank, the machine is still un‐
der pressure from the gas network or the section from the shut-off valve to the minimum pres‐
sure/check valve.
1. With the shut-off valve closed, insert the male hose fitting
6
into the hose coupling
1
.
2. Slowly open the shut-off valve
7
to release pressure.
3. Disconnect the male hose fitting
6
and close the shut-off valve
7
.
10.15.2 Topping up with cooling oil and trial run
Replenishing the cooling oil
A sticker on the oil separator tank specifies the type of oil used.
1. WARNING!
Compressed gas!
Compressed gas and devices under gas pressure can injure or cause death if the contained
energy of the gas is released suddenly or uncontrolled.
➤ Vent all pressurized components and chambers completely.
2.
NOTICE!
The machine could be damaged by unsuitable oil.
➤ Never mix different types of oil.
➤ Never top up with a different type of oil to that already used in the machine.
3. Slowly unscrew the filler plug
4
.
4. Top up to bring the oil to the correct level.
5. Renew the filler plug's gasket if necessary and screw the plug into the filler port.
Start the machine and carry out a trial run
1. Close all access doors, replace and secure all removable panels.
10 Maintenance
10.15 Replenishing the cooling oil
ESD_2C_10357405_10–LIN_00 E
Service Manual Screw Compressor
ESD 442/14 bar (abs) SFC SIGMA CONTROL 2
69
Summary of Contents for ESD 352 SFC
Page 5: ......
Page 6: ......
Page 7: ......
Page 8: ......
Page 9: ......
Page 10: ......
Page 11: ......
Page 12: ......
Page 13: ......
Page 14: ......
Page 15: ......
Page 16: ......
Page 17: ......
Page 18: ......
Page 19: ......
Page 20: ......
Page 21: ......
Page 22: ......
Page 23: ......
Page 24: ......
Page 25: ......
Page 26: ......
Page 27: ......
Page 28: ......
Page 29: ......
Page 30: ......
Page 31: ......
Page 32: ......
Page 33: ......
Page 34: ......
Page 35: ......
Page 171: ...KKW SSC 2 03 en 01 BA SIGMA CONTROL FLUID KKW SSC 2 03 01 20130805 113302...
Page 173: ......
Page 175: ...Contents ii Quick user guide Controller SIGMA CONTROL 2 SCREW FLUID 1 1 3 9_9450 03 USE...
Page 215: ...Contents iv Service manual Controller SIGMA CONTROL 2 SCREW FLUID 1 1 3 9_9450 03USE...
Page 392: ...KKW GBASE 1 00 en ERSATZTEILE 10357405_10 ESD 2C 20130903 115349...