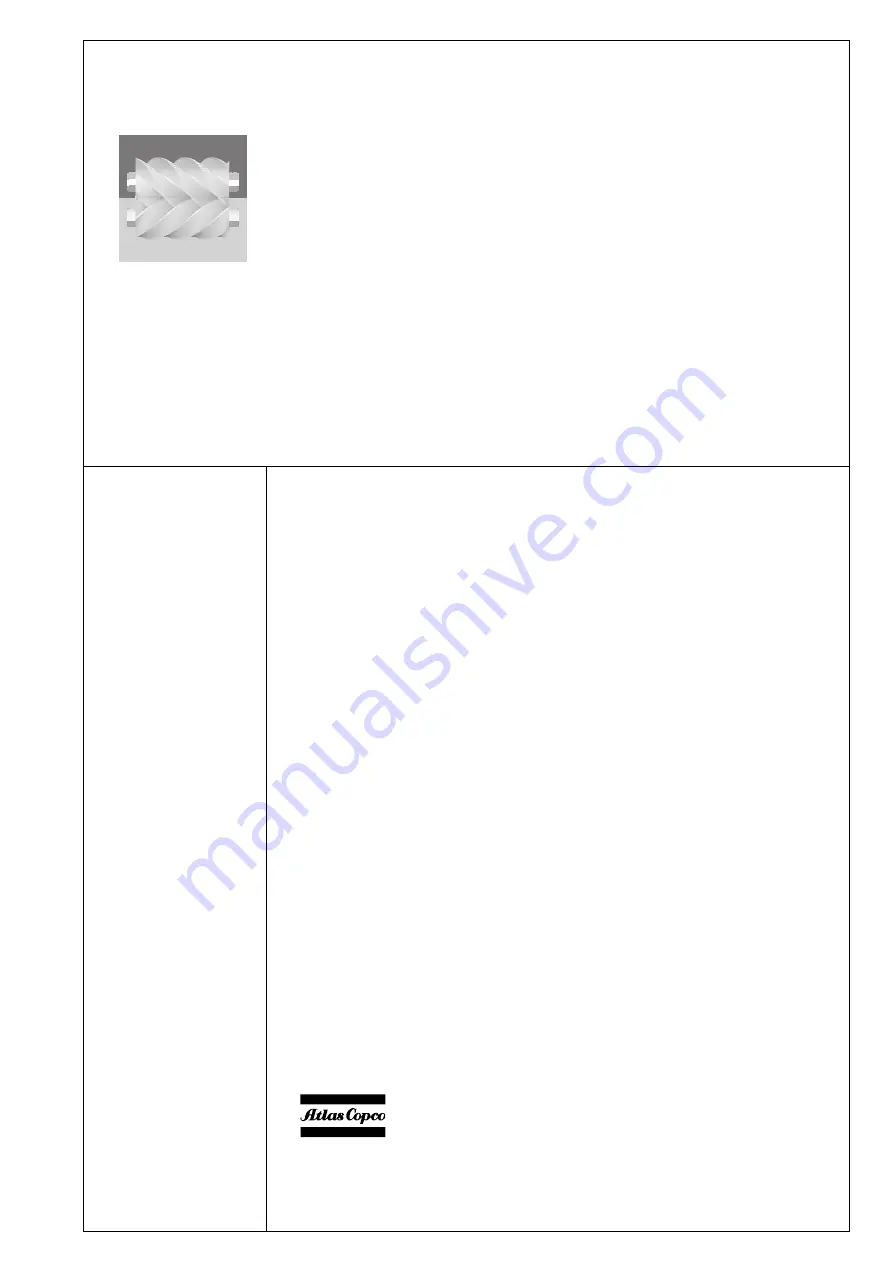
Instruction book for
stationary compressors
GA50 (W) VSD and
GA90 (W) VSD
Important: This book must be used together with the "User manual for Elektronikon®
regulator for GA50 VSD and GA90 VSD compressors"
Industrial Air Division - B-2610 Wilrijk - Belgium
Registration code
Collection: APC G VSD
Tab:
38
Sequence: 980
Replaces
No. 2920 1190 04
No. 2920 1190 05
1997-06
This instruction book meets the requirements for instructions specified by the
machinery directive 89/392/EEC and is valid for CE as well as non-CE labelled
machines
*2920119005*