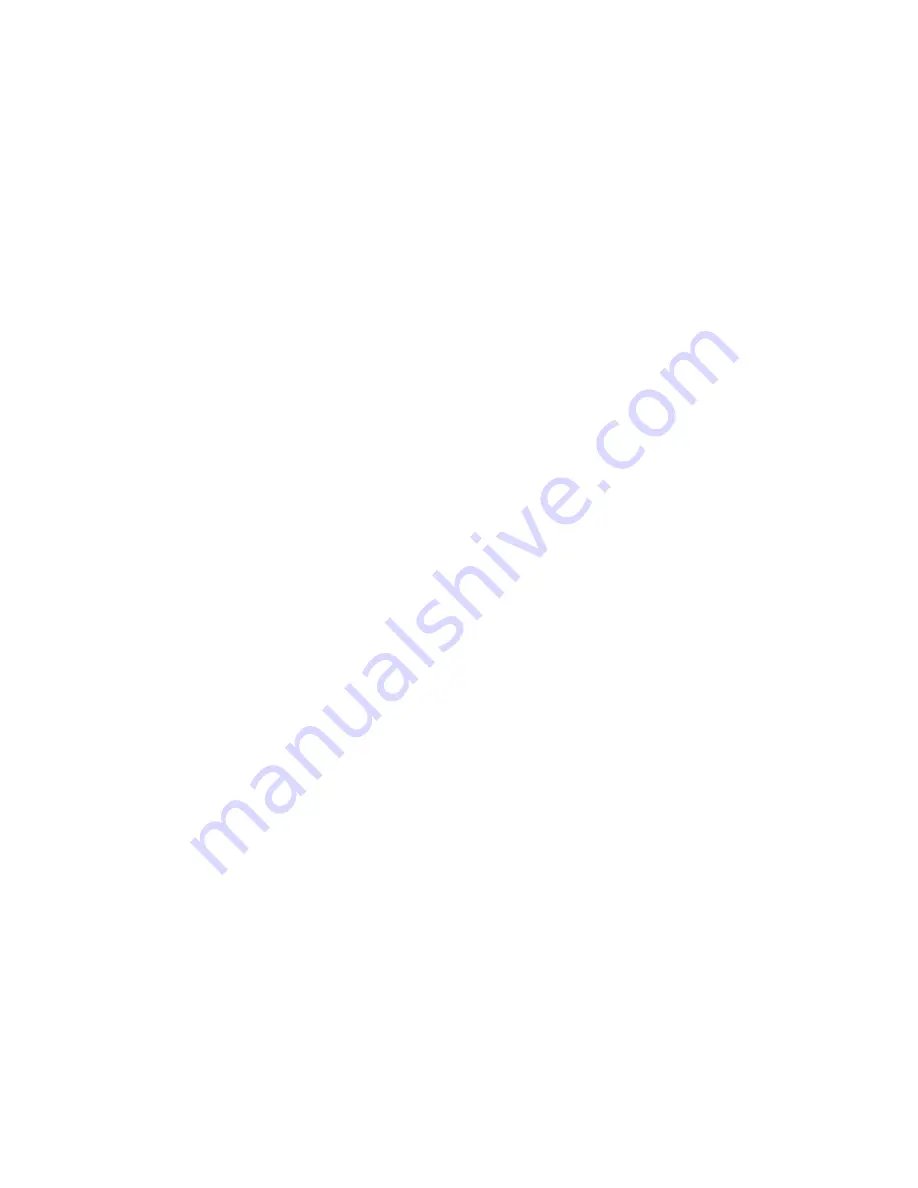
F 3
1003
.GB
3
Maintenance and Inspection
Thorough and correct maintenance is an important pre-requisite for safe operation of
the truck. If regular maintenance is neglected truck breakdowns can occur which in
turn could endanger life and limb and lead to operational failure.
M
Maintenance intervals are based on single shifts, working under normal conditions.
For more arduous conditions such as a dusty environment, extreme temperatures or
multi-shift working patterns, maintenance intervals should be reduced accordingly.
The following maintenance checklist gives the duties and intervals in which they
should be carried out. Maintenance intervals are defined as:
W1 = Every 50 Operating
hours,
however at least once a week
M3 = Every 500 Operating hours, however at least every 3 months
M6 = Every 1000 Operating hours, however at least every 6 months
M12 = Every 2000 Operating hours, however at least every 12 months
Z
Maintenance intervals W1 to be carried out by the operator
During the running in period additional tasks must also be carried out:
After the first 100 operating hours:
– Wheel nuts to be checked for tightness, tighten if necessary.
– Check tightness of bolts in drivers cab and hood, tighten if necessary.
– Check hydraulic hoses for leaks, tighten if necessary
– Change the hydraulic filter cartridge
– Tighten battery post screws and check condition of cell connector.
– Inspect all electrical and mechanical components.
– Check that the lifting chains are evenly tensioned (for aux. lift and duplex mast).
– Check the gearbox for leaks.
– Check that bolts are tight and mechanical locks are secure.
– Check mast slide pieces, adjust if required.
F 3
1003
.GB
3
Maintenance and Inspection
Thorough and correct maintenance is an important pre-requisite for safe operation of
the truck. If regular maintenance is neglected truck breakdowns can occur which in
turn could endanger life and limb and lead to operational failure.
M
Maintenance intervals are based on single shifts, working under normal conditions.
For more arduous conditions such as a dusty environment, extreme temperatures or
multi-shift working patterns, maintenance intervals should be reduced accordingly.
The following maintenance checklist gives the duties and intervals in which they
should be carried out. Maintenance intervals are defined as:
W1 = Every 50 Operating
hours,
however at least once a week
M3 = Every 500 Operating hours, however at least every 3 months
M6 = Every 1000 Operating hours, however at least every 6 months
M12 = Every 2000 Operating hours, however at least every 12 months
Z
Maintenance intervals W1 to be carried out by the operator
During the running in period additional tasks must also be carried out:
After the first 100 operating hours:
– Wheel nuts to be checked for tightness, tighten if necessary.
– Check tightness of bolts in drivers cab and hood, tighten if necessary.
– Check hydraulic hoses for leaks, tighten if necessary
– Change the hydraulic filter cartridge
– Tighten battery post screws and check condition of cell connector.
– Inspect all electrical and mechanical components.
– Check that the lifting chains are evenly tensioned (for aux. lift and duplex mast).
– Check the gearbox for leaks.
– Check that bolts are tight and mechanical locks are secure.
– Check mast slide pieces, adjust if required.
Summary of Contents for ETM/V 214
Page 1: ...Operating instructions 50314468 ETM V 214 216 G 10 03 10 03...
Page 3: ...1003 GB...
Page 5: ...0108 GB...
Page 9: ...1003 GB I 4...
Page 11: ...0600 GB A 2...
Page 31: ...1003 GB C 6...
Page 41: ...1003 GB D 10...
Page 44: ...E 3 1003 GB 3 14 15 4 5 6 7 8 9 11 12 13 10 16 17 1 2...
Page 46: ...E 5 1003 GB 3 14 15 4 5 6 7 8 9 11 12 13 10 16 17 1 2...
Page 83: ...1003 GB E 42...
Page 97: ...1003 GB F 14...