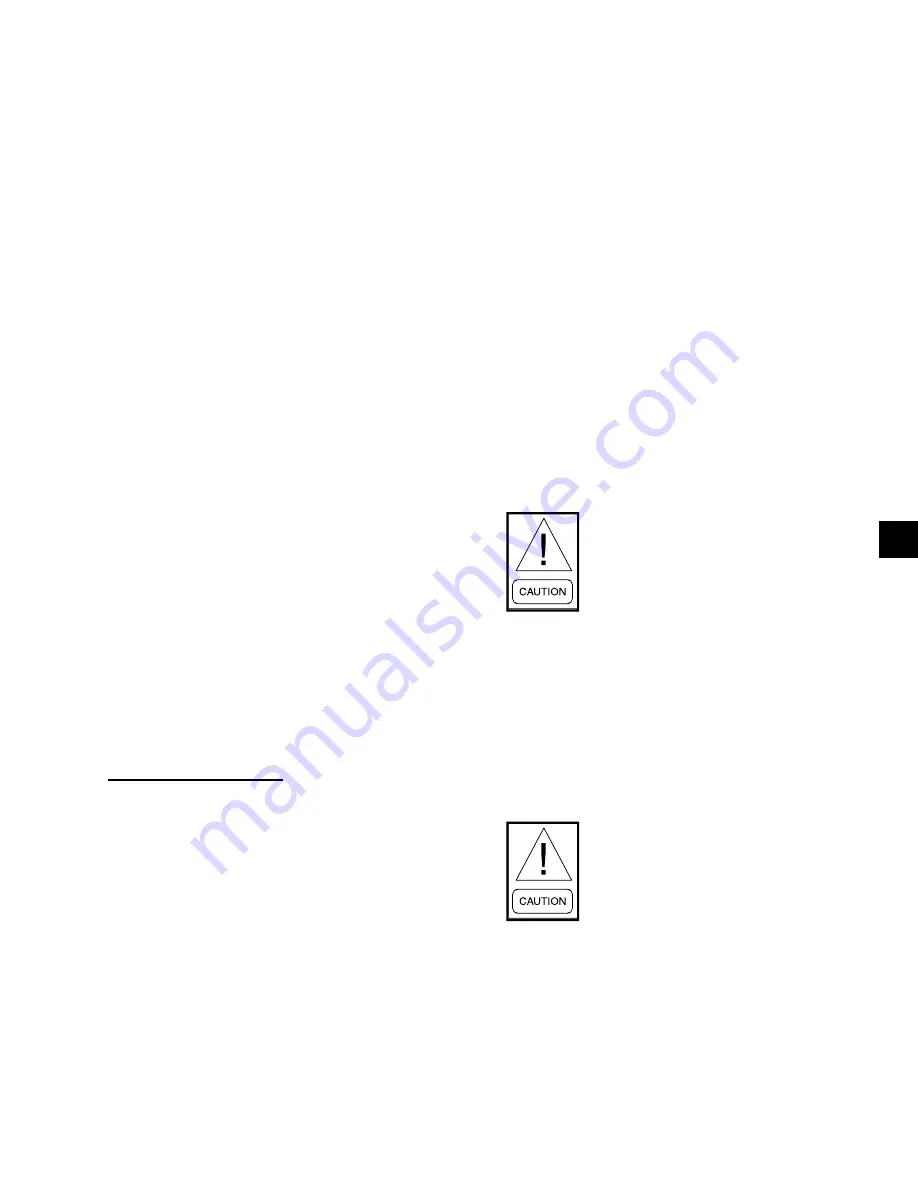
43
There are various degrees of self-alignment in bearings
of the same manufacturer. The force required for the self-
alignment of the bearings used in YORK manufactured
units has been specified and is closely monitored at the
factory. If it is necessary to purchase a bearing locally,
be sure it can be worked around in the housing with a
short shaft made of wood or other soft material placed
in the bearing.
Prior to installing the bearing on the shaft, it should
be worked around in the housing to make sure that
self-alignment will be obtained where the bearing is
installed. After the shaft journal has been inspected for
cleanliness, metal chips or burrs, the bearing is slipped,
not forced, onto the shaft. Forcing the bearing onto the
shaft by the use of flange, pillow block, or outer ring
will damage the bearing internally. Force applied in this
way transmits the load to the inner race through the balls
in the bearing. Since the bearings are not designed for
axial loading, the sides of the races in which the balls
turn can be damaged. If the bearing cannot be made to
slip onto the shaft by pressing on the inner ring of the
bearing, check the shaft for burrs. Install the bearing so
the part of the inner race, which receives the locking
collar or contains setscrews, is toward the outside of
the unit.
If the grease fitting must be changed on bearings that
utilize a locking pin under the fitting, it is important
to properly replace it. If an adapter or grease fitting of
improper size and length is used, the locking pin may
be either too tight or loose and can affect the alignment
and re-lubrication of the bearing.
Bearing Locking Devices
Various types of locking devices are used to secure
bearing(s) to the fan shaft.
Refer to the instructions
packed with bearings for special information.
The
various locking devices can be classified under basic
types: setscrew-type locking type, eccentric locking
type, concentric locking type, and Skwezloc type.
Condenser Coil Cleaning
The condenser water pressure drop tables contained
below can be used to determine proper water flow during
unit start up. In addition, they can he used as one of
several factors, refrigerant pressures, compressor amps,
etc. in determining if the unit has a build up of scale
and sludge in the condenser. The following procedure
should be used to clean the waterside of the condenser
section if required:
•
Shut down the unit
•
Utilize the appropriate lock out tag out pro-
gram.
•
Close the shut off isolation valves.
•
Open the low point drain to remove water from
the condenser.
•
Remove the condenser access panel.
•
Remove the compressor clean out plugs.
A back up wrench must be utilized on
the condenser tube while removing the
clean out plug to prevent damage to the
condenser tube.
•
Clean the condenser tubes with a cable type tube
cleaner and a 9/16” nylon brush
•
Inspect the O-ring gasket on the clean out plugs.
Replace if there are any signs of damage or per-
manent set.
•
Reinstall the condenser clean out plugs using a
back up wrench.
Do not over tighten.
•
Refill the water side of the condenser and purge
the air.
•
Open the shut off isolation valves.
•
Inspect the condenser coil for leaks.
•
Reinstall the condenser access panel.
•
Return the unit to normal operation.
4
JOHNSON CONTROLS
FORM 145.05-NOM1 (708)
Summary of Contents for York VERSECON YSWD 012
Page 12: ...12 JOHNSON CONTROLS FORM 145 05 NOM1 708 THIS PAGE INTENTIONALLY LEFT BLANK ...
Page 58: ...58 JOHNSON CONTROLS FORM 145 05 NOM1 708 THIS PAGE INTENTIONALLY LEFT BLANK ...
Page 106: ...106 JOHNSON CONTROLS FORM 145 05 NOM1 708 THIS PAGE INTENTIONALLY LEFT BLANK ...
Page 112: ...112 JOHNSON CONTROLS FORM 145 05 NOM1 708 THIS PAGE INTENTIONALLY LEFT BLANK ...