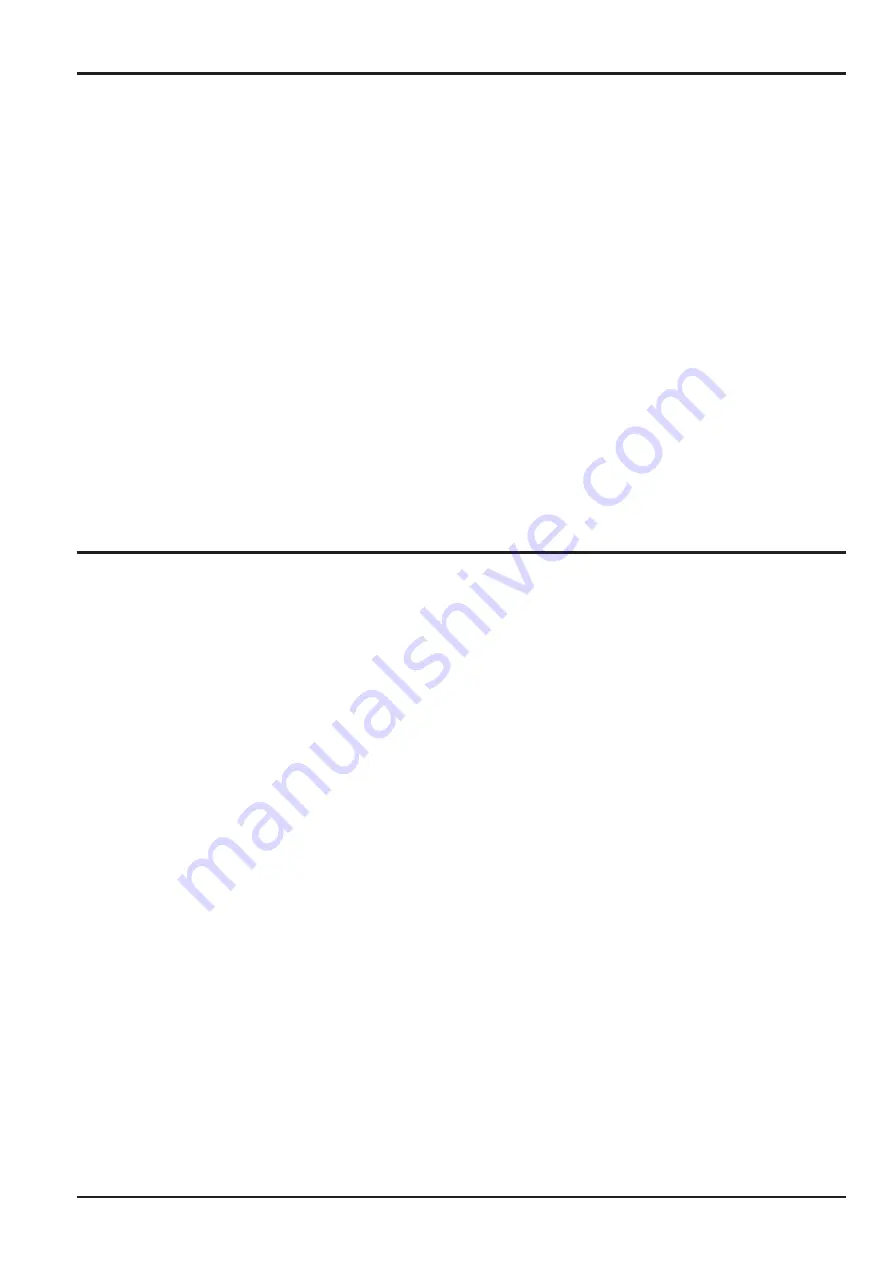
1 - 9
Rams
Boom Lift
Crowd
(80 x 40)
(100 x 50)
Compensating
(60 x 30)
(50 x 25)
Ram Torque Settings
Piston Head:
Boom Lift
Crowd
(80 x 40)
(100 x 50)
Compensating (60 x 30)
(50 x 25)
End Cap:
Boom Lift
Crowd
(80 x 40)
(100 x 50)
Compensating (60 x 30)
(50 x 25)
Bore
Rod Dia
Stroke
mm
in
mm
in
mm
in
70
2.75
40
1.57
677
26.65
80
3.15
40
1.57
233
9.17
100
3.94
50
1.97
234
9.21
60
2.36
30
1.18
264
10.39
50
1.97
25
0.98
288
11.32
Nm
lbf ft
Kg fm
405
299
41.3
405
299
41.3
405
299
41.3
300
221
30.6
250
184
25.5
678
500
69.2
678
500
69.2
678
500
69.2
450
331
45.9
400
295
40.8
Section E
Hydraulics
9803/8500
Section E
1 - 9
Issue 2*
Technical Data
General Description
The main components of the hydraulic circuit are the tank, pumps, drive motors, control valves, filters, cooler, and rams. Two
types of control system are used, servo and manual. On servo machines, hydraulic joystick controls are used to operate the
loader and drive functions.
The pumps are driven by the engine and are mounted in tandem. They deliver pressurised oil to the valves and motors.
Servo Machines
When a drive control is operated, oil is fed from the joystick to the transmission pump servo-controls. The pump swashplate
moves to vary or change the flow direction to the motors and hence the speed or direction of rotation. When a loader control is
operated, servo oil is fed from the joystick to a loader valve spool which then moves to direct pressurised oil to operate the
appropriate ram. Relief valves in the loader and transmission circuits prevent system pressure from rising too far.
On machines prior to serial number 678000, hydraulic pressure for the joysticks is regulated by the Pressure Reducing Solenoid
Valve which, together with its associated electrical circuitry, is designed to ensure that the controls cannot be operated without
the operator being seated correctly, with the Safety Restraint Bar in the operating position and the door closed and latched.
On machines from serial number 678000, hydraulic pressure for the joysticks is regulated by the transmission pump charge
valve and is fed to the joysticks via the solenoid operated Brake Valve. The Brake Valve, together with its associated electrical
circuitry, is designed to ensure that the controls cannot be operated without the operator being seated correctly, with the Safety
Restraint Bar in the operating position and the door closed and latched.
Manual Machines
The control levers are mechanically connected to the transmission pump and to the loader valve block. When a drive control is
operated, the pump swashplate is moved to change or reverse the flow direction to the motors. When a loader control is
operated, the loader valve spool moves to direct pressurised oil to operate the appropriate ram. Relief valves in the loader and
transmission circuits prevent system pressure from rising too far.
As an option on machines after serial number 678000, the loader functions can be controlled by dual foot pedals.
A mechanical interlock prevents the controls from being moved unless the Safety Restraint is in the operating position. In
addition, on machines after serial number 678000, solenoid operated lockout valves also prevent the boom service from being
operated until the operator is seated correctly in his seat, with the door closed and latched.
*
Summary of Contents for ROBOT 150
Page 2: ......
Page 21: ...5 2 Safety Decals cont d Section 2 Care and Safety 9803 8500 Section 2 5 2 Issue 2...
Page 77: ...Attachments Section A Section A 7 7 9803 8500 Issue 1 Backhoe...
Page 97: ...4 3 Section C Electrics 9803 8500 Section C 4 3 Issue 1 Alternator S213570...
Page 123: ...1 1 Section D Controls 9803 8500 Section D 1 1 Issue 1 Safety Restraint Bar S168160 1...
Page 125: ...2 1 Section D Controls 9803 8500 Section D 2 1 Issue 1 Throttle Controls S168150D...
Page 142: ...Hydraulics 9803 8500 Issue 1 4 1 4 1 Descriptions Section E Section E...
Page 145: ...Hydraulics 9803 8500 Issue 2 5 2 5 2 Descriptions Section E Section E...
Page 146: ...Hydraulics 9803 8500 Issue 2 5 3 5 3 Descriptions Section E Section E...
Page 149: ...Hydraulics 9803 8500 Issue 2 5 6 5 6 Descriptions Section E Section E...
Page 152: ...Hydraulics 9803 8500 Issue 1 5 9 5 9 Descriptions Section E Section E...
Page 163: ...10 1 Section E Hydraulics 9803 8500 Section E 10 1 Issue 1 Pumps 168150...
Page 165: ...10 3 Section E Hydraulics 9803 8500 Section E 10 3 Issue 1 Pumps 168030...
Page 167: ...10 5 Section E Hydraulics 9803 8500 Section E 10 5 Issue 1 Pumps 168160...
Page 175: ...11 1 Section E Hydraulics 9803 8500 Section E 11 1 Issue 2 Pumps 167750...
Page 179: ...13 1 Section E Hydraulics 9803 8500 Section E 13 1 Issue 1 Drive Motors 167720 S167720A...
Page 183: ...13 5 Section E Hydraulics 9803 8500 Section E 13 5 Issue 1 Drive Motors S243720 X X S243870...
Page 212: ...18 1 Section E Hydraulics 9803 8500 Section E 18 1 Issue 2 Valves S204980 X X 3 B A 4 2 1 5...
Page 215: ...20 1 Section E Hydraulics 9803 8500 Section E 20 1 Issue 1 Servo Joysticks S167960...
Page 217: ...20 3 Section E Hydraulics 9803 8500 Section E 20 3 Issue 1 Servo Joysticks 167950...
Page 221: ...23 3 Section E Hydraulics 9803 8500 Section E 23 3 Issue 1 Rams S167800...
Page 241: ...1 2 Section F Transmission 9803 8500 Section F 1 2 Issue 2 Tyres and Wheels 167861 167811...
Page 243: ...1 4 Section F Transmission 9803 8500 Section F 1 4 Issue 2 Tyres and Wheels 167851...
Page 253: ...2 1 Section K Engine 9803 8500 Section K 2 1 Issue 1 Removal and Replacement S167990...